Casting is a widely used manufacturing process that turns liquid metal into solid components, and selecting the right type of casting is crucial for the success of your project. Whether you're manufacturing complex parts for industrial machinery, automotive components, or agricultural equipment, understanding the various types of casting techniques will help you make an informed decision.
In this blog, we will explore the different casting methods available, their strengths, and the types of projects best suited for each technique. By understanding your project’s requirements, material needs, and production volume, you can choose the ideal casting method for optimal results.
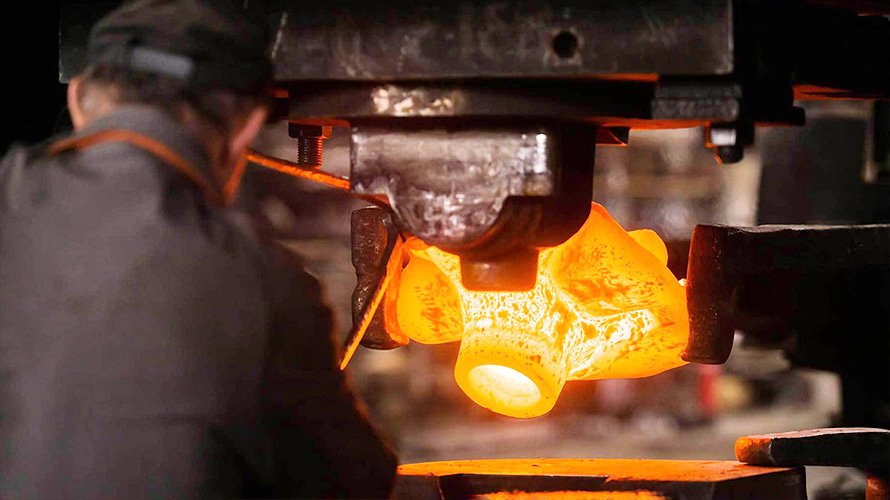
Sand Casting
Sand casting is one of the oldest and most versatile casting methods. It involves creating a mold from sand mixed with a binding agent (like clay) to hold the shape. The mold is then filled with molten metal, which solidifies to form the desired component. After cooling, the mold is broken to remove the casting.
When to Use Sand Casting
Sand casting is ideal for:
Large Parts: Sand casting can handle large components, making it perfect for heavy-duty machinery parts, automotive components, and even architectural elements.
Low to Medium Production Volumes: If you're producing medium to large quantities but do not need the precision required by other casting methods, sand casting is an affordable option.
Benefits of Sand Casting:
Cost-effective for both small and large parts.
Capable of producing complex geometries and large components.
Flexible in terms of material choice, including ferrous and non-ferrous metals.
Limitations:
Die Casting
Die casting is a high-pressure casting process in which molten metal is forced into a steel mold (die) under high pressure. This method is typically used for manufacturing high-precision, small-to-medium-sized components made from non-ferrous metals like aluminum, zinc, and magnesium.
When to Use Die Casting
Die casting is perfect for:
High-Volume Production: This method is most suitable for mass production, as the high-pressure system allows for quick cycles and consistent quality.
Precise, Small Parts: It’s ideal for parts that require high precision, smooth surface finishes, and intricate details, such as automotive parts, electronics housings, and medical device components.
Benefits of Die Casting:
High precision and repeatability, making it ideal for tight tolerances.
Excellent surface finish and minimal need for post-processing.
High production efficiency, reducing cost per part in large runs.
Limitations:
Investment Casting (Lost Wax Casting)
Investment casting, also known as lost wax casting, is a precise casting method where a wax pattern is coated with a ceramic shell. Once the shell hardens, the wax is melted and drained, leaving a cavity into which molten metal is poured. This process is ideal for parts requiring extreme detail and complex shapes.
When to Use Investment Casting
Investment casting is best for:
Precision Components: It’s highly effective for creating intricate parts with fine details, such as turbine blades, jewelry, medical implants, and aerospace components.
High-Performance Alloys: This method is commonly used for materials that need to withstand extreme conditions, such as superalloys for turbines or stainless steel for food processing equipment.
Benefits of Investment Casting:
Exceptional accuracy, suitable for parts with complex geometries.
High-quality surface finishes and minimal need for machining.
Ideal for high-strength, high-performance alloys.
Limitations:
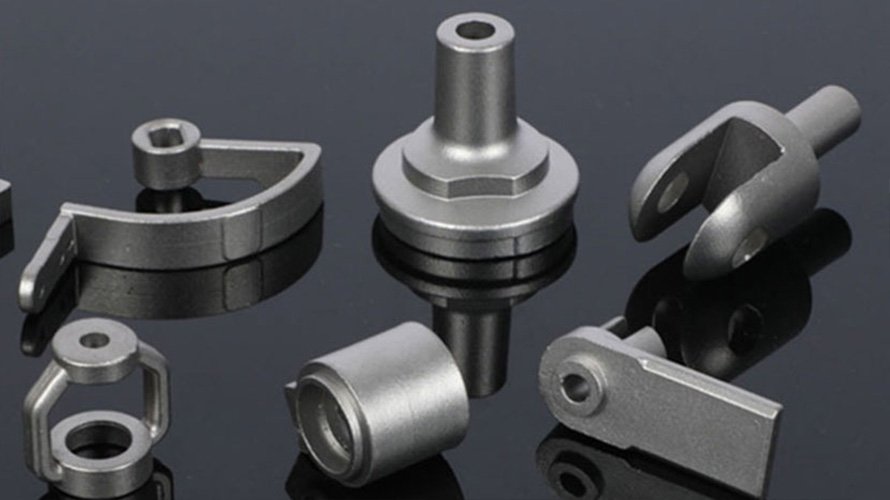
Shell Mold Casting
Shell mold casting is similar to investment casting but uses a metal pattern and a ceramic shell to form the mold. This method is commonly used for small to medium production runs and is well-suited for parts that need high dimensional accuracy and excellent surface finishes.
When to Use Shell Mold Casting
Shell mold casting is ideal for:
Medium-Volume Production: This method is often used for parts that require high precision and can be produced in moderate quantities.
Complex Part Geometry: If your components have intricate shapes that would be difficult to create with traditional sand casting, shell mold casting is a viable solution.
Benefits of Shell Mold Casting:
Better surface finish and tighter tolerances than sand casting.
Ideal for small to medium-sized parts with intricate details.
Efficient for high-performance materials such as stainless steel.
Limitations:
Centrifugal Casting
Centrifugal casting is a process where molten metal is poured into a rotating mold, which forces the metal to solidify under centrifugal force. This method is primarily used for cylindrical parts, such as pipes, tubes, and bushings, and ensures uniform material distribution and density.
When to Use Centrifugal Casting
Centrifugal casting is best for:
Hollow Cylindrical Parts: This method is ideal for producing parts like pipes, rollers, and bearings that require uniform strength and density across the entire component.
High-Volume Production: If you need to produce a large number of components with consistent quality, centrifugal casting can be highly efficient.
Benefits of Centrifugal Casting:
Produces uniform, dense components with minimal defects.
Ideal for parts requiring strength and resistance to wear.
Reduced porosity, making it ideal for pressure vessels and components that must withstand high mechanical stress.
Limitations:
Not suitable for non-cylindrical parts.
High equipment costs, making it less ideal for small-scale production.
Permanent Mold Casting
In permanent mold casting, molten metal is poured into a reusable mold made of steel, iron, or other durable materials. The mold is designed to withstand high temperatures and can be used for multiple cycles, making this process ideal for medium to high production runs.
When to Use Permanent Mold Casting
Permanent mold casting is best suited for:
Medium-Volume Production: This method is ideal when you need to produce a moderate quantity of components with consistent quality.
Non-ferrous Materials: It works best for materials like aluminum, magnesium, and copper alloys.
Benefits of Permanent Mold Casting:
Consistent and repeatable quality, suitable for medium to large production runs.
Good for parts requiring high surface finish and dimensional accuracy.
Cost-effective for producing non-ferrous metal parts in medium quantities.
Limitations:
Limited to producing smaller parts, as larger molds become cost-prohibitive.
Higher upfront tooling costs compared to sand casting.
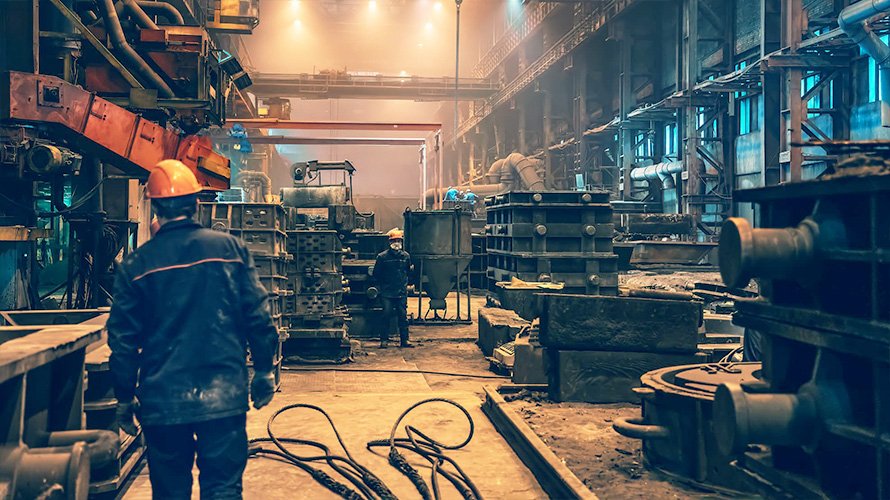
Choosing the Right Casting Method for Your Project
Material. The type of metal required can significantly influence your choice of casting method. For example, non-ferrous metals like aluminum and zinc are best suited for die casting, while ferrous metals are often cast using sand casting or investment casting.
Part Complexity. If your part requires intricate details or a complex geometry, investment casting or shell mold casting might be the best option. For simpler, larger parts, sand casting might be sufficient.
Production Volume. High-volume, mass-produced components are best suited for die casting, while small to medium batches may be more cost-effective with permanent mold or sand casting.
Budget. Upfront tooling costs for methods like die casting and permanent mold casting are higher but often lead to lower per-unit costs in mass production. If you have a smaller budget or lower volume, sand casting or investment casting might be more appropriate.
Conclusion
Choosing the right type of casting for your project depends on factors like material, part complexity, production volume, and budget. Whether you’re looking for the precision of investment casting or the cost-effectiveness of sand casting, understanding the advantages and limitations of each method will help you make the right decision.
At the end of the day, the ideal casting method is one that balances your specific needs—whether that’s low-cost production, high-precision components, or the ability to handle large parts. Consult with a casting expert to find the best solution tailored to your project’s requirements.