Manufacturing processes have evolved significantly over the years, providing a diverse range of techniques to produce components for various industries. Among these, casting and machining are two of the most prominent methods, each with unique strengths and applications. While both processes aim to create functional parts, they differ greatly in execution, costs, and suitability for specific tasks. In this comprehensive guide, we explore the differences between casting and machining, delving into their processes, advantages, and typical applications.
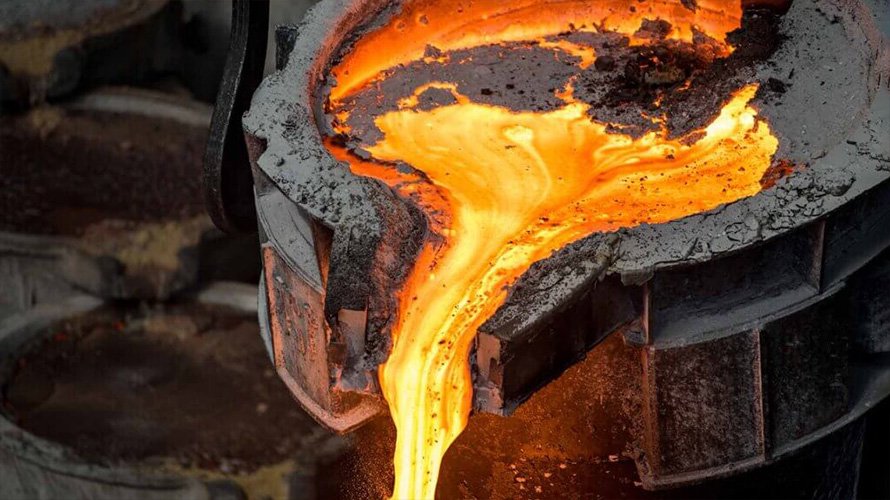
Understanding Casting
Casting is one of the oldest known manufacturing techniques, with a history dating back thousands of years. It involves shaping molten material into a desired form using molds.
The Casting Process
The casting process begins with the preparation of a mold. Molds can be made from sand, metal, or ceramic, depending on the type of casting being performed. Once the mold is ready, molten metal or other material is poured into the cavity. After cooling and solidifying, the mold is removed, revealing the final component. This method is especially effective for creating large or complex parts.

Types of Casting Methods
There are several casting techniques, each suited to specific needs:
Sand Casting: Ideal for producing large, simple components with rough finishes.
Die Casting: A high-pressure method used for creating intricate, high-volume parts with smooth finishes.
Investment Casting: Known for its precision, it’s used for small, detailed parts requiring excellent surface quality.
Continuous Casting: Commonly used for producing sheets, rods, and billets in large quantities.
Advantages of Casting
Casting offers several advantages, such as:
The ability to create complex shapes and large parts.
Cost-effectiveness for high-volume production.
Compatibility with a wide range of materials, including metals and alloys.
Exploring Machining
Machining, a subtractive manufacturing process, shapes components by removing material from a solid workpiece through cutting, grinding, or drilling.
The Machining Process
Machining starts with a solid block or rod of material. Using tools like lathes, mills, and drills, the material is cut away to create the desired shape. Computer Numerical Control (CNC) machining has revolutionized this process, providing unparalleled precision and efficiency.
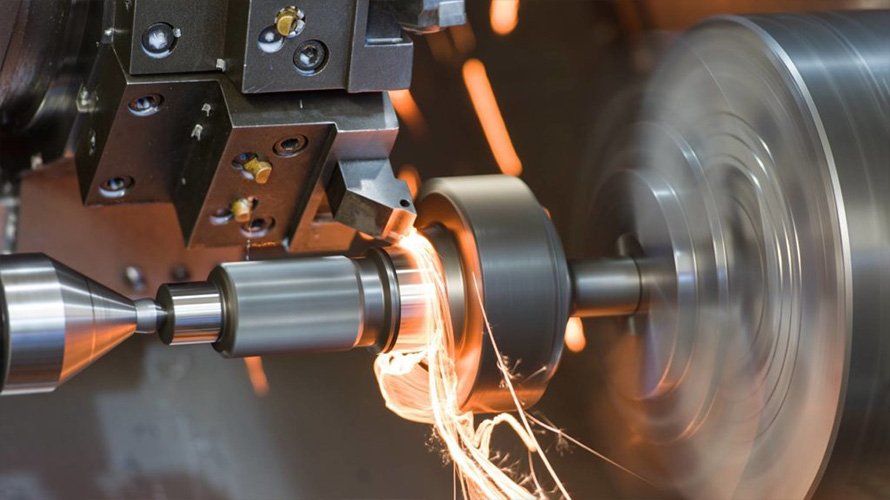
Types of Machining Techniques
Machining encompasses various methods:
Turning: Uses a lathe to create cylindrical parts.
Milling: Removes material using rotating cutting tools to create flat or contoured surfaces.
Drilling: Creates precise holes in a workpiece.
Grinding: Enhances surface finish and achieves tight tolerances.
Advantages of Machining
The benefits of machining include:
High precision and tight tolerances.
Superior surface finishes.
Flexibility for low-volume production and prototyping.
Compatibility with a wide range of materials, including metals, plastics, and composites.
Comparing Casting and Machining
While both processes aim to produce high-quality components, they differ significantly in execution and application. Here’s a detailed comparison:
Material Utilization
Casting is an additive process where molten material is poured into a mold. This minimizes material wastage, making it efficient for large-scale production. Machining, being subtractive, often results in significant material waste, especially for parts requiring extensive cutting.
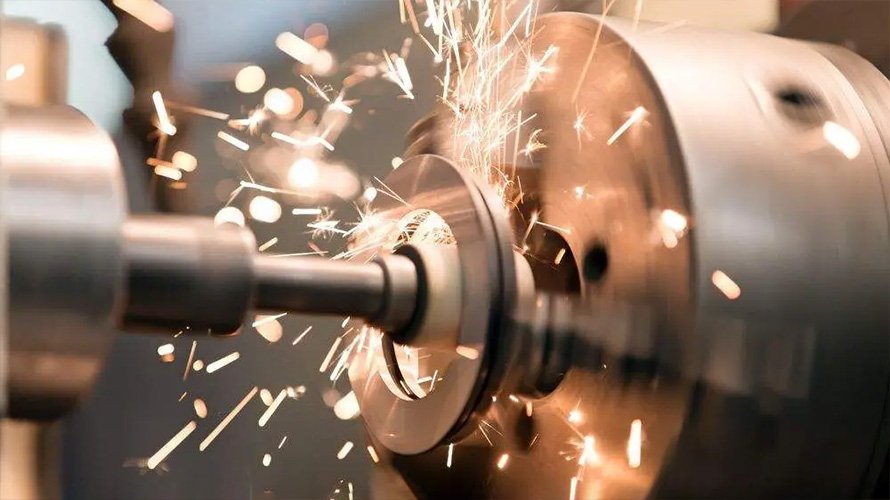
Precision and Complexity
Machining excels in precision, achieving tight tolerances and intricate details that casting may struggle to replicate. However, casting is more suitable for creating complex geometries, such as hollow sections, that are difficult or impossible to machine.
Production Volume
Casting is highly efficient for high-volume production due to reusable molds. Machining, though more costly for large-scale production, is ideal for small runs, custom parts, or prototypes.
Cost Considerations
Casting generally has higher upfront costs due to mold creation but becomes more economical for large quantities. Machining has lower setup costs but higher per-unit costs, especially for complex or labor-intensive parts.
Lead Times
Casting often requires longer lead times due to mold preparation and cooling. Machining offers quicker turnaround, particularly for custom or low-volume projects.
Applications of Casting and Machining
Both casting and machining are integral to modern manufacturing, but their applications differ based on the nature of the components being produced.
Applications of Casting
Casting is widely used in industries requiring large or complex parts, including:
Automotive: Engine blocks, transmission housings, and wheels.
Construction: Structural components, pipe fittings, and frames.
Aerospace: Turbine blades, housings, and high-strength components.
Industrial Equipment: Large gears, pumps, and valves.
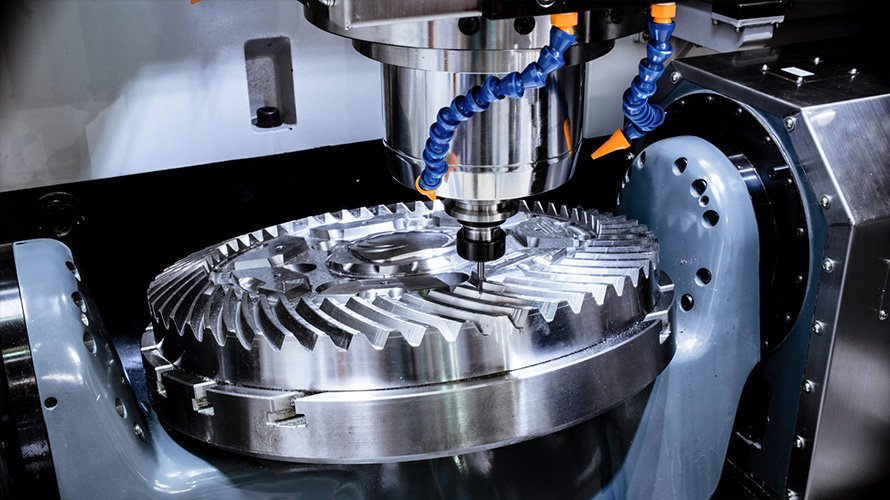
Applications of Machining
Machining is preferred for components requiring precision and tight tolerances, such as:
Medical Devices: Surgical tools, implants, and prosthetics.
Aerospace: High-precision engine parts and fittings.
Electronics: Custom heat sinks and connectors.
Prototyping: Creating test components for design validation.
Choosing Between Casting and Machining
Deciding which process to use depends on several factors, including design requirements, budget, and production volume.
Design Requirements
For intricate designs with hollow sections or complex geometries, casting is often the better choice. Machining is ideal for components requiring detailed features, tight tolerances, and smooth finishes.
Material Considerations
Certain materials, such as high-strength alloys, may be better suited for machining, as they can be difficult to melt for casting. Conversely, casting works well with metals and alloys that flow easily in liquid form.
Cost and Volume
Casting is cost-effective for high-volume production due to reusable molds. For low-volume production or prototypes, machining offers greater flexibility and lower initial costs.
Lead Times and Speed
Machining generally offers faster turnaround times, making it suitable for urgent or custom projects. Casting, with its mold preparation and cooling requirements, may take longer but can handle large production runs more efficiently.
The Future of Casting and Machining
Advancements in technology are reshaping both casting and machining, enhancing their efficiency, precision, and sustainability.
Additive Manufacturing Integration
3D printing is increasingly being integrated with casting and machining. In casting, 3D-printed molds and patterns reduce lead times and costs. In machining, additive manufacturing complements subtractive methods by creating pre-forms that require minimal finishing.
Sustainability Initiatives
Both processes are adopting greener practices, such as using recycled materials and energy-efficient equipment. Casting facilities are exploring ways to reduce waste by reusing molds, while machining shops focus on recycling metal shavings and optimizing tool life.
Automation and AI
Automation and artificial intelligence are revolutionizing production in both casting and machining. Automated casting systems improve consistency and reduce labor costs, while AI-powered machining tools enhance precision and reduce material waste.
Improved Materials
Innovations in material science are expanding the capabilities of casting and machining. New alloys and composites offer enhanced strength, corrosion resistance, and lightweight properties, meeting the demands of industries such as aerospace and automotive.
Conclusion
Casting and machining are two cornerstone manufacturing processes, each with distinct advantages and applications. Casting’s ability to produce complex shapes and large parts makes it ideal for industries like automotive, aerospace, and construction. Machining, with its unmatched precision and versatility, is indispensable for medical devices, electronics, and custom prototypes.
Understanding the differences between these processes helps manufacturers select the right method for their needs. Factors such as design complexity, material properties, production volume, and budget play critical roles in this decision.
At EATHU, we specialize in both casting and machining, offering tailored solutions to meet diverse manufacturing requirements. Whether you need high-volume cast components or precision-machined parts, our expertise ensures top-quality results. Contact us today to learn more about how we can support your next project.