I. Introduction
Valve castings, as the crucial control components in various industrial piping systems, have a direct impact on the safety and stable operation of the entire system. After the casting process, the surface treatment of valve castings is of vital importance. It not only concerns the appearance of the valve but also has a profound influence on its performance and durability under different environmental conditions. This article will deeply explore the two main surface treatment processes for valve castings - dry cleaning and wet cleaning, analyze their principles, characteristics, and application status. Combining with the technical advantages of EATHU in the field of valve castings, we will also explore the optimization directions and development trends of surface treatment processes, providing a comprehensive technical reference for improving the overall quality of valve castings.
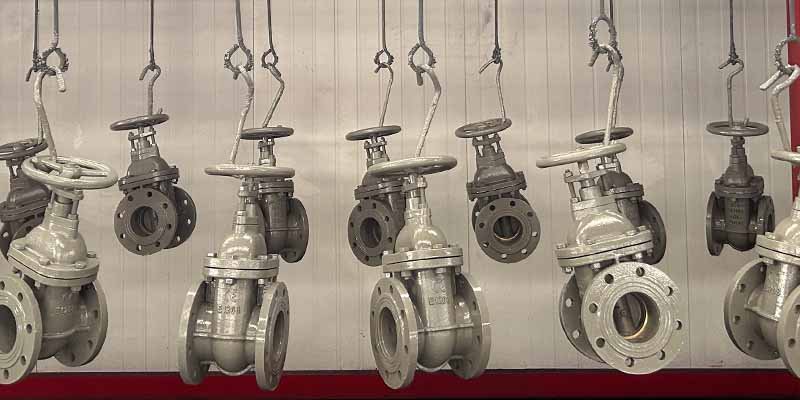
II. Necessity of Valve Casting Surface Treatment
During the casting process of valve castings, due to the interaction between the molten metal and air, molding materials, etc., various impurities inevitably adhere to their surfaces. These impurities mainly include oxide scales, sand grains, metal splashes, etc. The presence of oxide scales will affect the surface finish of valve castings, making their appearance rough and dull, which does not meet the requirements of modern industry for product appearance quality. In some application scenarios with high requirements for aesthetics, such as valves for building decoration and valves for high-end instrument and meter systems, the unattractive surface will reduce the overall grade of the product.
From the perspective of environmental suitability, the adhesion of impurities may lead to problems such as corrosion and accelerated wear of valve castings in specific environments. For example, in the chemical industry, valve castings may come into contact with various corrosive media. If the surface impurities are not thoroughly cleaned, these impurities will become the initiation points of corrosion, accelerating the corrosion process of the valve, reducing its service life, and may even cause serious safety accidents such as medium leakage. In high-temperature and high-pressure environments, sand grains and other impurities on the surface may damage the sealing surface of the valve, affecting its sealing performance and thus failing to meet the sealing requirements of the system. Therefore, surface treatment of valve castings is a necessary step to ensure their quality and performance.
III. Dry Cleaning Process
(I) Principle and Operation Procedure
Dry cleaning mainly adopts the methods of shot blasting or grit blasting, using highly compressed air to eject shot at a high speed onto the surface of valve castings. The shot usually selects metal or non-metal materials with high hardness, such as steel shot, glass shot, etc. When the shot hits the surface of the valve casting, based on the principle of kinetic energy transfer, the impurities such as oxide scales and sand grains on the surface are knocked off, thus achieving the purpose of cleaning.
During the operation, first, the valve casting needs to be placed in a special cleaning device, which has a sealed working chamber and a shot recycling and circulation system. Then, start the compressed air system to make the shot form a high-speed jet under the drive of high-pressure air and shoot towards the surface of the valve casting. The operator needs to reasonably adjust the type, size, ejection pressure, ejection angle, and time of the shot according to factors such as the material, shape, size of the valve casting, and the degree of impurity adhesion. For example, for valve castings with a softer material, a shot with a relatively lower hardness should be selected to avoid damaging the casting body; for valve castings with complex shapes and more recesses and holes, the ejection angle needs to be adjusted to ensure that the shot can reach all the areas that need to be cleaned.
(II) Advantages and Disadvantages Analysis
Advantages
Relatively simple equipment: The dry cleaning equipment mainly consists of a compressed air source, a shot ejection device, a working chamber, and a shot recycling system. The structure is relatively simple, the floor area is small, and the initial investment cost is relatively low.
Relatively fast cleaning speed: Under appropriate parameter settings, the shot can quickly hit the surface of the valve casting and remove impurities in a large area. For some valve castings with a large area and loosely adhered impurities, the preliminary cleaning work can be completed in a relatively short time.
Less environmental impact: Since no liquid medium is involved, the dry cleaning process will not produce wastewater, waste liquid, and other pollutants, and the environmental pollution risk is low, which is suitable for some occasions with high environmental protection requirements but relatively less strict requirements for surface treatment uniformity.
Disadvantages
Uneven surface treatment: Due to the influence of various factors during the shot ejection process, such as the stability of compressed air, the difference in the shape and quality of the shot, and the deviation of the ejection angle, it is easy to cause an uneven cleaning effect on the surface of the valve casting. Some parts may be over-cleaned, resulting in surface damage, while some hidden parts or recesses may not be thoroughly cleaned, leaving residual impurities.
Limited cleaning efficiency: For some situations where a high surface roughness is required and the impurities are tightly combined with the casting surface, simple dry cleaning is difficult to completely remove the impurities. It requires repeated cleaning or combination with other processes, which increases the processing time and cost and reduces the overall cleaning efficiency.
Dust pollution: When the shot hits the surface of the valve casting, a large amount of dust will be generated. If this dust is not effectively treated, it will diffuse in the working environment, endangering the health of the operators, and may also affect the normal operation of the equipment and the cleanliness of the surrounding environment.
IV. Wet Cleaning Process
(I) Principle and Operation Procedure
The wet cleaning process is to place the valve casting in a specific liquid medium and then use the vibration frequency difference between the valve casting and impurities generated by discharging to remove the impurities. This process is based on electrochemical and physical vibration principles.
Specifically, first, a suitable liquid medium needs to be prepared. This medium usually contains components such as electrolyte solution, buffer, and surfactant. The electrolyte solution is used to provide a conductive environment and promote the occurrence of the discharging process; the buffer is used to stabilize the pH value of the solution and prevent corrosion of the valve casting; the surfactant helps to reduce the surface tension of the liquid, making it easier for the impurities to separate from the surface of the valve casting. After the valve casting is completely immersed in the liquid medium, a certain frequency and voltage of alternating current or pulsed current are applied through the electrodes. When the current passes through the liquid medium, a small arc discharge phenomenon will occur between the surface of the valve casting and the impurities. The instantaneous high temperature, high pressure, and accompanying physical vibration generated by the discharge break the binding force between the impurities and the surface of the valve casting, and the impurities are separated from the casting surface under the scouring and vibration of the liquid medium. During the cleaning process, the liquid medium needs to be continuously stirred to ensure that the impurities can be taken away in time. At the same time, according to the material and impurity situation of the valve casting, the discharging parameters such as voltage, current, frequency, and discharge time need to be precisely controlled.
(II) Advantages and Disadvantages Analysis
Advantages
Good surface treatment uniformity: Since the liquid medium can evenly wrap the valve casting, the discharging process occurs relatively evenly on the entire casting surface, making the impurity removal effect more uniform and consistent. It can effectively avoid the problems of local over-cleaning or incomplete cleaning, thereby obtaining a higher surface finish.
Good cleaning effect: For some impurities that are tightly combined with the surface of the valve casting, such as the complex compounds formed between the oxide scale and the casting matrix, the wet cleaning process can completely decompose and remove them through the high temperature, high pressure, and vibration generated by discharging, greatly improving the quality and depth of surface treatment and meeting the application needs with high requirements for the surface quality of valve castings, such as high-precision hydraulic valves and nuclear power valves.
No dust pollution: Compared with dry cleaning, the wet cleaning process will not produce a large amount of dust. The working environment is relatively clean, which is beneficial to the health of the operators and also reduces the dust pollution to the surrounding environment, meeting the environmental protection requirements of a relatively high production environment standard.
Disadvantages
Complex process: The wet cleaning process involves multiple links such as the preparation of the liquid medium, the setting of electrodes, the precise control of discharging parameters, and the liquid circulation and filtration system. The process is relatively complex and requires operators to have a relatively high professional technical level and rich experience. The requirements for production management and quality control are also high.
High equipment cost: Due to the complex process, the corresponding equipment composition is also relatively complex, including a power supply system, an electrolytic cell, a stirring device, a liquid circulation filtration system, etc. The purchase, installation, and maintenance costs of the equipment are all high, increasing the production cost and investment risk of the enterprise.
Waste liquid treatment problem: The liquid medium used in the wet cleaning process will contain a large amount of impurities and pollutants after a period of use and requires special waste liquid treatment. Waste liquid treatment not only requires additional equipment and processes but also has a high treatment cost. If not properly treated, it will also cause secondary pollution to the environment, which is also an important challenge faced by the wet cleaning process.
V. EATHU's Technical Advantages and Innovative Practices in Valve Casting Surface Treatment
(I) Advanced Equipment and Process Optimization
EATHU has invested a large amount of resources in equipment research and development and process optimization for the surface treatment process of valve castings. In terms of dry cleaning, the company has independently developed a high-precision shot ejection control system, which can monitor and adjust the shot ejection parameters in real-time, effectively improving the uniformity of surface treatment. By using advanced sensor technology, parameters such as compressed air pressure, shot flow rate, and ejection angle are accurately measured and fed back to the control system. The control system automatically adjusts various parameters according to the preset algorithm and the real-time processing situation of the valve casting to ensure that the impact force and coverage of the shot on the surface of the valve casting are uniform. For example, when processing a batch of complex-shaped stainless steel valve castings, this system can dynamically adjust the shot ejection angle according to the shape change of the casting, so that each part can be properly cleaned, and the deviation of surface roughness is controlled within a very small range.
In terms of wet cleaning, EATHU has developed an intelligent wet cleaning device, integrating an advanced power management system and a liquid medium monitoring and control system. The power management system can accurately output a stable discharge voltage, current, and frequency according to the material and treatment requirements of the valve casting, ensuring the high efficiency and stability of the discharging process. The liquid medium monitoring and control system can monitor parameters such as electrolyte concentration, pH value, and impurity content in the liquid medium in real-time and automatically add corresponding chemical agents for adjustment to ensure that the liquid medium is always in the best working state. For example, when processing high-strength alloy steel valve castings, this device can automatically adjust the discharging parameters according to the alloy composition of the casting, so that oxide scales and other impurities can be completely removed in the shortest time while avoiding any damage to the casting matrix.
(II) Practice of Environmental Protection and Sustainable Development Concepts
EATHU deeply recognizes the importance of environmental protection in modern industrial production and actively practices environmental protection and sustainable development concepts in the surface treatment process of valve castings. In the dry cleaning process, the company adopts an efficient dust collection and purification system. This system uses multi-stage filtration and electrostatic adsorption technology to collect almost all the dust generated during the shot ejection process and purify it. After reaching the environmental protection emission standard, it is discharged. At the same time, the collected dust is recycled. The metal dust is separated and reprocessed into shot or other metal products, realizing the recycling of resources and reducing the generation of waste.
In the wet cleaning process, EATHU is committed to researching and developing green and environmentally friendly liquid medium formulations and waste liquid treatment technologies. The company's R & D team has developed biodegradable electrolyte solutions and surfactants through a large number of experiments, greatly reducing the harm of the liquid medium to the environment. In terms of waste liquid treatment, a method combining advanced membrane separation technology and chemical precipitation technology is adopted, which can efficiently separate harmful substances in the waste liquid, convert them into harmless solid precipitates for recovery or safe disposal, and the treated clear water can be recycled, improving the utilization rate of water resources and minimizing the impact of waste liquid discharge on the environment.
(III) Personalized Customization Service and Quality Assurance
EATHU provides personalized surface treatment customization services according to the special requirements of different customers for valve castings. The company has a professional technical team that can deeply understand the application scenarios, performance expectations, and quality standards of customers and tailor the most suitable surface treatment plan for them. For example, for valve castings used in the marine environment, considering the high salt spray corrosion risk they face, EATHU will adopt a special passivation treatment process after wet cleaning to form a dense passivation film on the surface of the valve casting, effectively improving its corrosion resistance; for valve castings used in the food processing industry, in addition to requiring a high surface finish and no residual impurities, they also need to meet strict hygienic standards. EATHU then adopts a food-grade liquid medium and cleaning process to ensure that the surface of the valve casting meets the food safety requirements.
In terms of quality assurance, EATHU has established a complete quality management system, strictly controlling every link from raw material inspection, surface treatment process monitoring to finished product inspection. During the surface treatment process, advanced testing equipment such as a three-dimensional profilometer and a scanning electron microscope is used to monitor the surface roughness, impurity residue, and microstructure of valve castings in real-time to ensure that the surface treatment quality meets the customer requirements and relevant standards. For products that do not meet the quality standards, they will not be allowed to leave the factory. The reasons will be analyzed in a timely manner, and improvement measures will be taken to continuously improve the stability and reliability of product quality.
VI. Development Trends and Prospects of Valve Casting Surface Treatment Processes
With the continuous progress of industrial technology and the increasingly strict environmental requirements, the surface treatment processes of valve castings will develop in a more efficient, environmentally friendly, and intelligent direction. In terms of dry cleaning, it is expected to develop new shot materials and ejection technologies in the future to further improve the cleaning efficiency and surface treatment quality. For example, developing self-repairing shot, which can automatically adjust its shape and hardness according to the wear situation of the surface of the valve casting when hitting the surface, prolong the service life of the shot and improve the cleaning effect; exploring the use of laser-assisted shot blasting technology, using the energy of the laser to form a small shock wave on the surface of the valve casting to enhance the ability of the shot to remove impurities and reduce the damage to the casting body.
In terms of wet cleaning, the focus will be on the research and development of the green and harmless of the liquid medium and the innovation of waste liquid treatment technology. Develop more environmentally friendly and efficient electrolyte solutions and surfactants to reduce the amount and toxicity of chemical agents; study new waste liquid treatment technologies, such as biological waste liquid degradation methods based on biotechnology, using the metabolic action of microorganisms to decompose and convert harmful substances in the waste liquid into harmless substances to achieve zero waste liquid discharge.
At the same time, intelligent technology will be more widely used in the surface treatment processes of valve castings. By introducing artificial intelligence algorithms and big data analysis, the automatic control of surface treatment equipment and the intelligent optimization of process parameters will be realized. For example, according to data such as the material, shape, size, and surface quality requirements of valve castings, the intelligent system can automatically select the best surface treatment process and parameters and monitor and adjust them in real-time during the treatment process to ensure that each valve casting can obtain the optimized surface treatment, improving production efficiency and the consistency of product quality.
In addition, with the continuous improvement of the performance requirements of valve castings, surface treatment processes will be combined with other surface modification technologies, such as surface coating technology and ion implantation technology. While improving the surface finish of valve castings, more functional characteristics such as wear resistance, corrosion resistance, and lubricity will be to meet the increasingly demanding application requirements of valve castings in different industries.
In conclusion, the surface treatment process of valve castings is a key link to ensure the quality and performance of valves. The dry cleaning and wet cleaning processes have their own advantages and disadvantages, and in practical applications, they need to be selected according to the specific requirements and production conditions of valve castings. EATHU, with its advantages in advanced equipment and process optimization, the practice of environmental protection and sustainable development concepts, and personalized customization service and quality assurance in the field of valve casting surface treatment, has set a good example for the valve casting industry. Looking ahead, the surface treatment processes of valve castings will continue to develop and progress under the impetus of technological innovation, providing strong support for the wider application of valve castings.