In recent years, 3D printing has significantly impacted multiple industries, including metal casting. The advent of 3D printing technology has opened new possibilities for prototyping, production, and improving workflows. When combined with metal casting techniques, it enhances efficiency, reduces costs, and enables the creation of complex parts that were previously unimaginable.
This guide explores how 3D printing can be integrated into metal casting workflows, its benefits, applications, and real-world examples of the synergy between these two advanced manufacturing technologies.
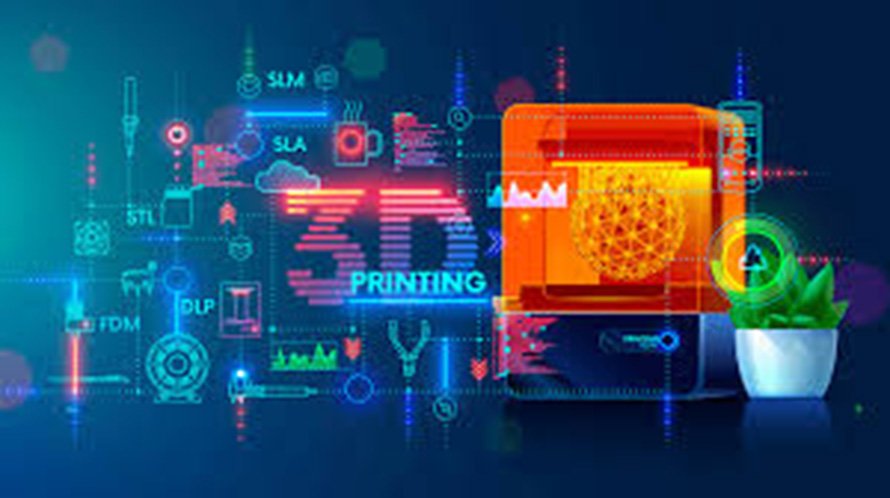
Understanding 3D Printing in Manufacturing
Before delving into the integration of 3D printing with metal casting, it’s essential to understand what 3D printing is and how it works in a manufacturing context.
What is 3D Printing?
3D printing, also known as additive manufacturing, is a process of creating three-dimensional objects by adding material layer by layer based on digital models. Unlike traditional subtractive methods, where material is removed from a larger block, 3D printing builds objects from the ground up, allowing for intricate designs with minimal material waste.
Types of 3D Printing Technologies
There are various 3D printing technologies that are commonly used in manufacturing:
· Fused Deposition Modeling (FDM): Works by extruding thermoplastic material layer by layer. It’s primarily used for prototyping.
· Stereolithography (SLA): Uses a laser to solidify liquid resin, ideal for creating detailed prototypes.
· Selective Laser Sintering (SLS): Uses a laser to sinter powdered materials, such as nylon or metal, into solid structures.
· Binder Jetting: Uses a liquid binder to fuse powdered material, allowing for metal 3D printing in the case of metal powders.
Advantages of 3D Printing in Metal Casting
Incorporating 3D printing into metal casting offers several benefits, including:
· Rapid Prototyping: 3D printing enables fast iterations of designs, allowing for quick adjustments before proceeding to casting.
· Complex Geometries: 3D printing can produce complex shapes that would be difficult or impossible to achieve with traditional metal casting methods.
· Reduced Waste: The additive nature of 3D printing minimizes material waste compared to subtractive manufacturing methods.
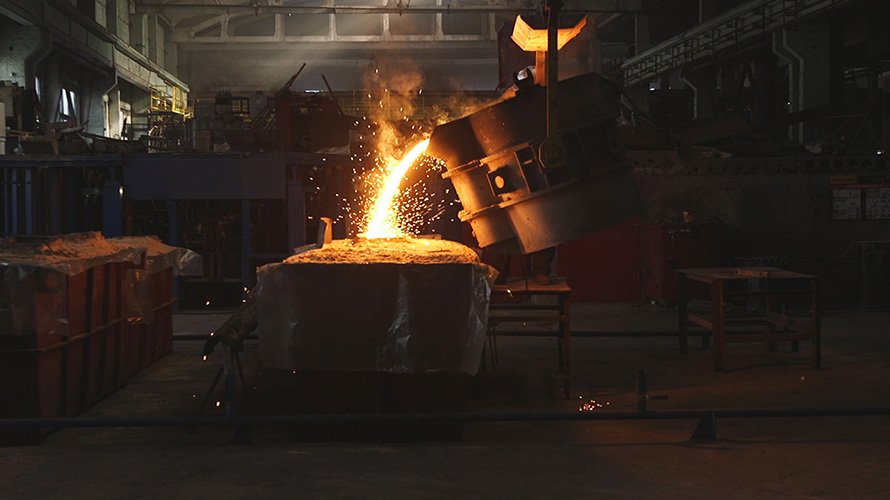
Integrating 3D Printing with Metal Casting Workflows
The combination of 3D printing and metal casting can streamline the production process, reduce costs, and improve the quality of the finished product. Here’s how these technologies can work together effectively.
3D Printing as a Tool for Mold Creation
One of the most significant advantages of combining 3D printing with metal casting is the ability to create complex molds that would be difficult or costly to produce using traditional methods.
Benefits of 3D Printed Molds
· Speed and Precision: 3D printing allows for rapid production of molds, reducing lead times and ensuring greater precision.
· Complex Internal Features: 3D printing can create intricate internal features, like cooling channels, which improve the performance of the final cast metal part.
· Customization: Designers can make design changes quickly and cost-effectively, allowing for more flexible production schedules.
Case Studies of 3D Printed Molds
Many industries have embraced the use of 3D-printed molds, such as aerospace and automotive, where the need for high-precision and lightweight components is critical. A notable example is how GE Aviation uses 3D-printed molds to create turbine blades with complex cooling channels, which cannot be created using traditional mold-making techniques.
3D Printing for Investment Casting
Investment casting, also known as lost-wax casting, is a metal casting process that involves creating a mold from a pattern that is then melted away. 3D printing can be a game-changer for this process.
How 3D Printing Supports Investment Casting
· Pattern Creation: 3D printing can be used to create highly detailed and complex patterns for investment casting. These patterns can be directly printed in materials like wax or plastic, eliminating the need for traditional pattern-making processes.
· Reduced Lead Times: The traditional investment casting process can take a significant amount of time to create molds. With 3D printing, this time can be drastically reduced, speeding up the entire production cycle.
· Enhanced Design Flexibility: 3D printing allows designers to experiment with intricate shapes, internal channels, and fine features that would have been difficult to replicate with traditional techniques.
Real-World Example: Aerospace Components
In the aerospace industry, companies like Siemens have successfully integrated 3D printing into their investment casting process. For instance, 3D-printed metal parts such as turbine blades and brackets have been produced using this combined approach, achieving superior strength-to-weight ratios and enhanced performance.
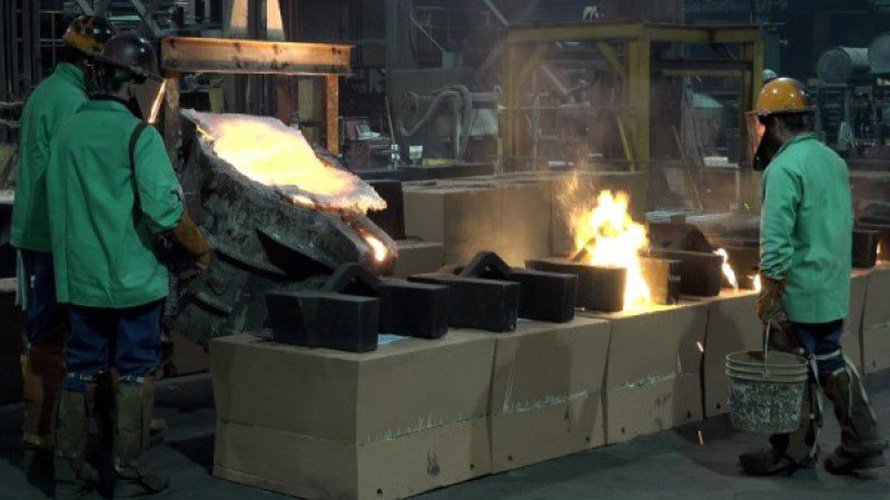
Benefits and Challenges of Combining 3D Printing with Metal Casting
While the integration of 3D printing into metal casting workflows offers many advantages, there are also certain challenges that need to be addressed.
Key Benefits of the Integration
· Improved Efficiency: By combining 3D printing and metal casting, manufacturers can speed up the entire production process, reducing downtime and increasing throughput.
· Cost Savings: Reducing material waste, eliminating the need for traditional molds, and shortening lead times can result in significant cost savings in production.
· Design Freedom: 3D printing opens up new possibilities for creating complex and intricate designs that would be expensive or impossible with traditional casting methods.
· Quality Control: The combination of these technologies ensures high-quality parts with fewer defects, as 3D printing allows for precise control over geometry and material properties.
Challenges to Consider
· Material Limitations: While 3D printing can use a wide variety of materials, including metals, it may still be limited by the specific materials available for casting. Not all metals are suitable for 3D printing.
· Investment in Equipment: Incorporating 3D printing into metal casting workflows requires significant investment in 3D printing equipment and software, as well as staff training.
· Post-Processing Requirements: After 3D-printed parts are cast, they may require additional post-processing steps, such as cleaning, polishing, or heat treatment, which can add time and cost to the process.
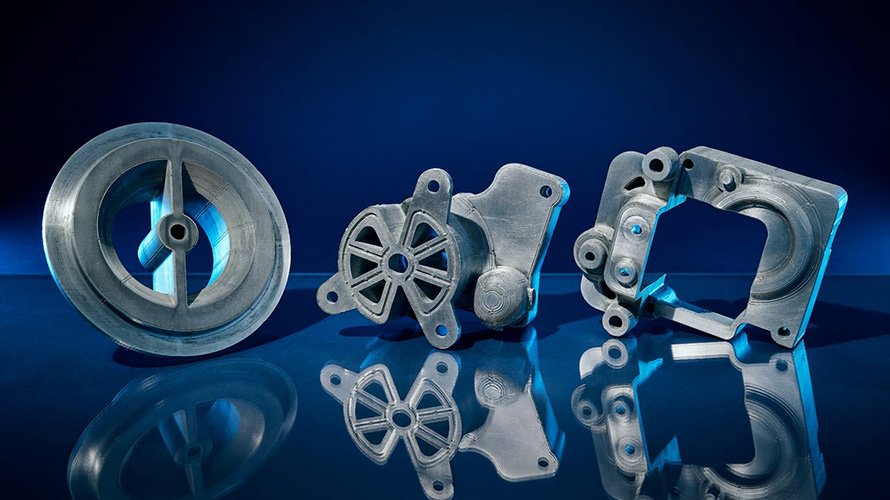
The Future of 3D Printing and Metal Casting Integration
The future of 3D printing and metal casting is incredibly promising. As 3D printing technology continues to evolve, its applications in metal casting will only expand, offering even greater design flexibility, efficiency, and quality.
Advancements in Material Science
Ongoing advancements in material science are expected to unlock new possibilities for 3D printing with metals, especially in industries that require specialized alloys or high-performance materials, such as aerospace and automotive.
Hybrid Manufacturing Systems
The rise of hybrid manufacturing systems, which combine 3D printing and traditional manufacturing techniques, will allow companies to take advantage of both technologies. For instance, 3D printing could be used to create intricate parts that are then finished using traditional casting, or vice versa.
Greater Automation and AI Integration
The integration of artificial intelligence and automation into 3D printing and metal casting workflows will further enhance productivity, precision, and cost efficiency. AI can help optimize designs, predict potential issues, and ensure smoother production processes.
Conclusion
The combination of 3D printing and metal casting represents the next frontier in manufacturing. By leveraging the strengths of both technologies, manufacturers can enhance the production of metal components, improve design flexibility, reduce waste, and achieve better quality and performance. As the technologies continue to evolve, the potential for innovation in industries ranging from aerospace to automotive will be boundless.
Manufacturers who embrace this hybrid approach will position themselves for success in the increasingly competitive global market, enabling faster, more efficient, and cost-effective production.