Prototype casting is an essential step in product development, allowing manufacturers to test, refine, and validate designs before committing to full-scale production. Whether you're in the automotive, aerospace, medical, or consumer goods industry, prototype casting provides a cost-effective and efficient way to bring ideas to life.
In this article, we’ll explore the fundamentals of prototype casting, the different methods used, its applications, and the benefits it offers to manufacturers and product developers.
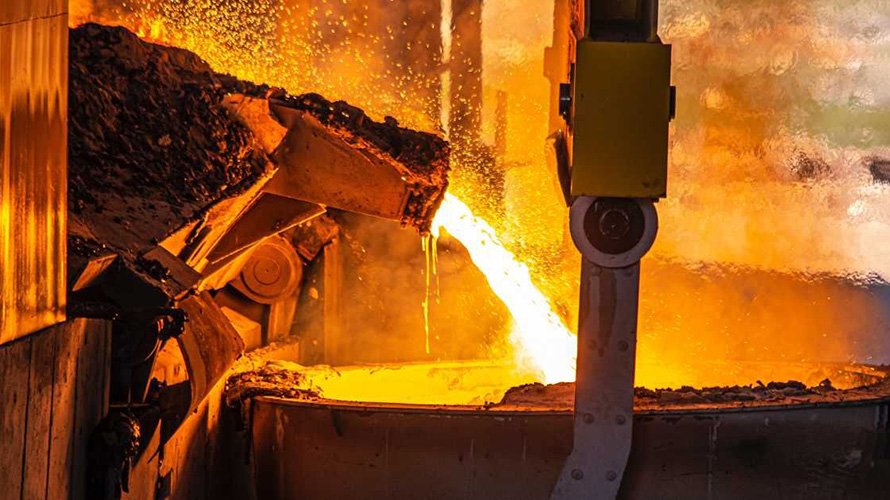
What is Prototype Casting?
Prototype casting is the process of creating a small batch of metal or plastic parts using casting techniques to test a design before mass production. Unlike traditional manufacturing, which focuses on high-volume production, prototype casting emphasizes speed, flexibility, and precision.
This process is crucial for industries that require functional prototypes to evaluate performance, material properties, and design feasibility. By casting prototypes, manufacturers can identify potential issues, make necessary modifications, and avoid costly errors in mass production.
Why is Prototype Casting Important?
Prototype casting plays a critical role in product development for several reasons:
· It enables rapid design iterations and refinements.
· It helps detect design flaws before large-scale manufacturing.
· It reduces costs by preventing expensive tooling modifications later.
· It allows engineers to test different materials and casting techniques.
· It provides stakeholders with tangible samples for evaluation.
By investing in prototype casting, businesses can ensure their final product meets quality, durability, and performance requirements.
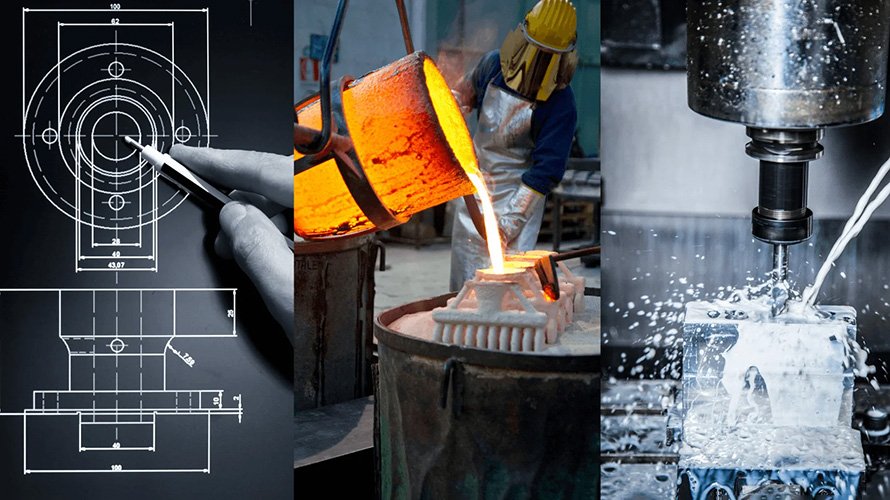
Methods of Prototype Casting
There are several casting methods used to create prototypes, each with its own advantages and applications. The choice of method depends on factors such as material selection, part complexity, lead time, and budget.
Sand Casting
Sand casting is one of the oldest and most widely used prototype casting methods. It involves creating a mold from sand and then pouring molten metal into the cavity to form the desired shape.
Advantages of Sand Casting:
· Cost-effective for low-volume prototypes.
· Suitable for large and complex parts.
· Compatible with various metals, including aluminum, iron, and bronze.
Limitations of Sand Casting:
· Surface finish may require post-processing.
· Not ideal for high-precision components.
Investment Casting
Investment casting, also known as lost-wax casting, involves creating a wax or resin pattern, coating it with ceramic, and then melting away the pattern to leave a cavity for metal casting.
Advantages of Investment Casting:
· Produces highly detailed and precise prototypes.
· Suitable for complex geometries and thin-walled parts.
· Works well with a wide range of metals, including steel, aluminum, and titanium.
Limitations of Investment Casting:
· Longer production time compared to other methods.
· Higher cost due to labor-intensive processes.
Die Casting for Prototyping
Die casting involves injecting molten metal into a reusable metal mold under high pressure. Although die casting is primarily used for high-volume production, rapid tooling techniques allow for prototype development.
Advantages of Die Casting:
· High precision and excellent surface finish.
· Suitable for intricate parts with tight tolerances.
· Ideal for aluminum, zinc, and magnesium alloys.
Limitations of Die Casting:
· Expensive initial tooling costs.
· Limited flexibility for design changes.
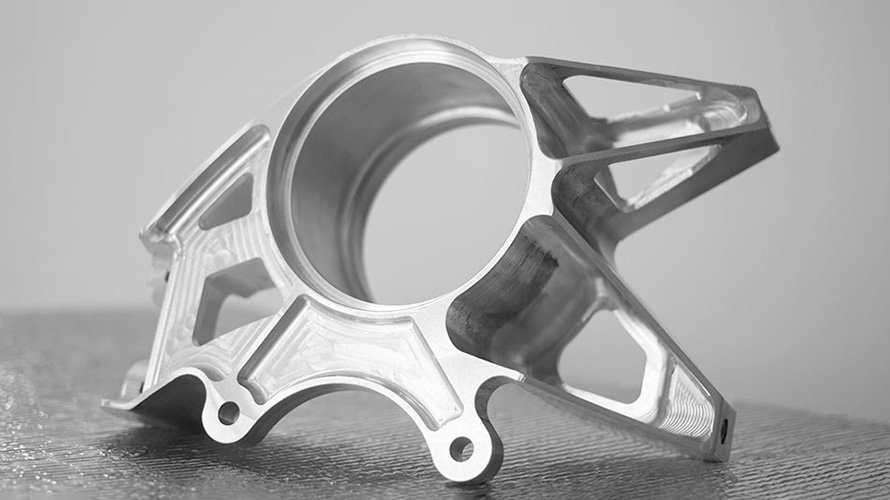
3D Printed Casting Patterns
With advancements in 3D printing, manufacturers can create patterns for casting prototypes quickly and cost-effectively. This hybrid approach combines additive manufacturing with traditional casting techniques.
Advantages of 3D Printed Casting Patterns:
· Rapid prototyping with reduced lead time.
· Lower cost compared to traditional tooling.
· Suitable for highly complex and customized designs.
Limitations of 3D Printed Casting Patterns:
· Material selection may be limited.
· Surface finish may require additional refinement.
Each of these methods has its strengths and is chosen based on the project’s requirements, budget, and timeline.
Applications of Prototype Casting
Prototype casting is widely used across various industries, from automotive and aerospace to healthcare and consumer goods.
Automotive Industry
In the automotive sector, prototype casting is essential for developing engine components, transmission housings, and structural parts. Engineers use cast prototypes to evaluate strength, weight reduction, and heat resistance before full-scale production.
With the rise of electric vehicles (EVs), manufacturers are using prototype casting to develop lightweight aluminum and magnesium components that enhance performance and efficiency.
Aerospace and Defense
The aerospace industry demands high-precision parts that withstand extreme conditions. Prototype casting allows engineers to test turbine blades, airframe components, and structural elements before committing to large-scale production.
Investment casting is particularly valuable in this industry due to its ability to produce intricate parts with minimal material waste.
Medical and Healthcare
Prototype casting is widely used in the medical industry to develop surgical tools, orthopedic implants, and prosthetics. Titanium and stainless steel castings are commonly used for their biocompatibility and durability.
With rapid prototyping techniques, medical device manufacturers can create and test patient-specific implants before final production, ensuring a perfect fit and optimal performance.
Industrial Equipment and Machinery
Many industrial components, such as pump housings, gearboxes, and valves, are developed using prototype casting. Manufacturers rely on this process to test parts under real-world operating conditions before committing to large production runs.
Casting prototypes help ensure that critical machinery components meet durability, performance, and safety standards.
Consumer Goods and Electronics
Prototype casting is used to develop components for electronics, appliances, and decorative products. From smartphone casings to intricate jewelry designs, casting techniques provide precision and design flexibility.
Manufacturers in the consumer goods sector benefit from rapid iteration and customization, allowing them to bring innovative products to market faster.
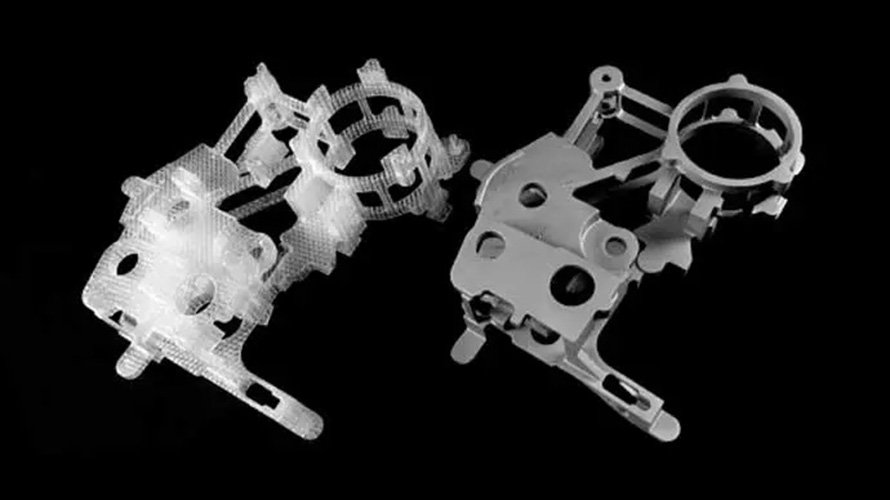
Benefits of Prototype Casting
Prototype casting significantly accelerates product development by enabling rapid iterations. Engineers can test multiple design variations without the long lead times associated with traditional manufacturing.
Cost-Effective Prototyping
Compared to full-scale production, prototype casting is a cost-effective way to refine designs before investing in expensive tooling. Manufacturers can identify flaws early, reducing the risk of costly rework.
Enhanced Design Flexibility
Prototype casting allows for intricate and complex designs that would be challenging to achieve with other methods. Engineers can test different materials and geometries to optimize performance.
Real-World Performance Testing
By casting functional prototypes, manufacturers can evaluate how a part performs under actual working conditions. This helps ensure the final product meets industry standards for strength, durability, and functionality.
Reduced Time to Market
With advancements in rapid prototyping and casting techniques, businesses can bring products to market faster. This competitive advantage is crucial in industries where innovation and speed are key factors.
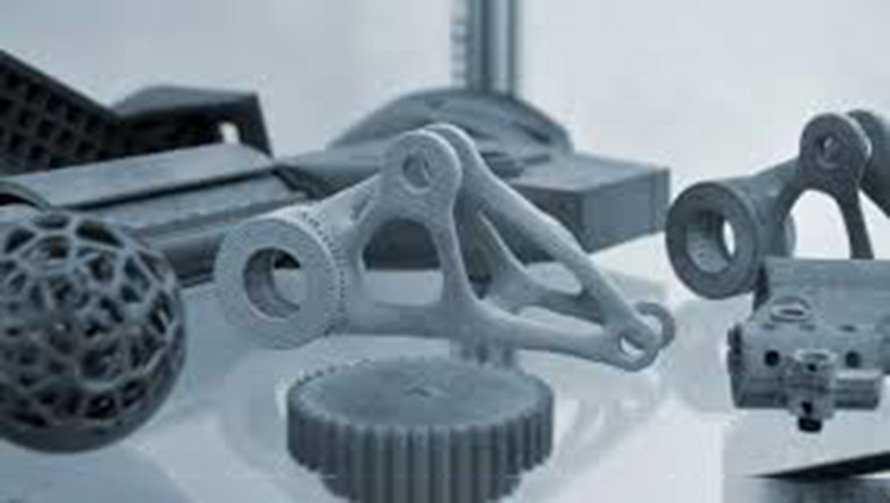
Conclusion
Prototype casting is an invaluable tool in modern manufacturing, bridging the gap between concept and production. By leveraging various casting techniques, industries can develop and refine products with greater efficiency, precision, and cost-effectiveness.
Whether you're in the automotive, aerospace, medical, or consumer goods industry, prototype casting provides a reliable method for testing and validating designs before mass production. As technology advances, the integration of 3D printing, digital modeling, and rapid casting techniques will further enhance the prototyping process, making it more accessible and efficient than ever before.
Investing in prototype casting ensures that products are not only functional but also optimized for performance, durability, and market success.