The world of metal casting is undergoing a transformation with the integration of 3D printing technologies. While traditional methods like sand casting and die casting have been the cornerstone of metal manufacturing for decades, 3D printing has opened new avenues for efficiency, precision, and innovation. By combining the advantages of additive manufacturing with the robustness of metal casting, industries are now able to produce complex, high-performance metal parts with reduced lead times and greater design flexibility. In this blog, we’ll dive deep into the role of 3D printing in metal casting, its processes, advantages, and applications.
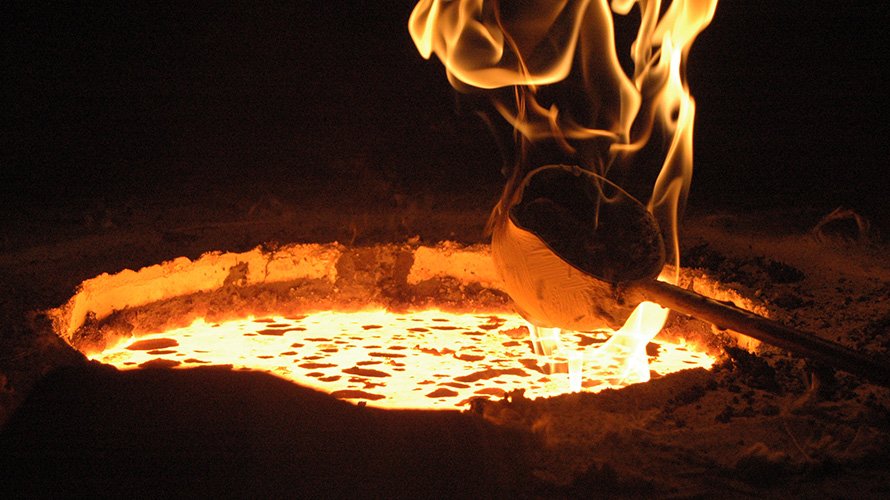
Understanding 3D Printing in Metal Casting
3D printing for metal casting is an additive manufacturing process that uses 3D printers to create patterns or molds for metal castings. Unlike traditional casting methods where molds are made from sand, metal, or other materials, 3D printing uses digital designs to create highly detailed and precise molds layer by layer. The resulting mold can then be filled with molten metal to produce complex parts that would be difficult or impossible to create with conventional methods.
The Role of 3D Printing in the Casting Process
In traditional metal casting, the mold is typically created by shaping a material (like sand or metal) around a pattern of the final part. With 3D printing, however, the pattern or mold is created directly from a digital 3D model. This method eliminates the need for some of the traditional steps, like tooling and pattern making, significantly reducing time and cost. Additionally, 3D-printed molds often provide higher accuracy and finer detail.
Key Technologies Used in 3D Printing for Metal Casting
Several 3D printing technologies are used in metal casting, each with unique capabilities:
· Binder Jetting: This method uses a binder to bind powdered metal or sand, which is then sintered to create a strong mold.
· Selective Laser Sintering (SLS): SLS uses a laser to fuse metal powder particles into a solid mold.
· Fused Deposition Modeling (FDM): FDM is commonly used for creating investment casting patterns, where thermoplastic materials are used to print the patterns.
Advantages of 3D Printing in Metal Casting
One of the most significant benefits of 3D printing in metal casting is the ability to create highly intricate and complex designs. Traditional casting methods often struggle with geometric complexities, such as undercuts or hollow sections. With 3D printing, however, these complexities can be incorporated directly into the design, allowing manufacturers to create parts with geometries that were previously impossible or prohibitively expensive to produce.
Reduced Lead Time and Faster Prototyping
With traditional metal casting, the process of making molds can be time-consuming, especially for custom or small-batch production. 3D printing dramatically reduces lead time by allowing rapid prototyping of molds and patterns. Since 3D printers can produce molds directly from a digital file, the turnaround time for creating a pattern or mold can be cut down from weeks to days. This is particularly valuable in industries where quick iteration and prototype testing are critical.
Cost Savings in Low-Volume Production
For small production runs or highly customized parts, the costs of traditional metal casting molds can be prohibitively expensive. The need for complex tooling and pattern-making adds significant overhead. With 3D printing, these costs are reduced, making it an ideal solution for low-volume or custom metal casting. Additionally, the process eliminates the need for specialized tooling, further reducing costs.
Improved Precision and Accuracy
3D printing technologies offer unmatched precision, which leads to highly accurate molds and, consequently, parts with superior dimensional consistency. In traditional casting, even slight imperfections in the mold can lead to defects in the final part. With 3D printing, the process is digital and controlled, significantly reducing the risk of defects and improving the overall quality of the cast part.
Applications of 3D Printing in Metal Casting
The aerospace industry has long been at the forefront of adopting advanced manufacturing technologies, and 3D printing for metal casting is no exception. 3D-printed molds are used to create lightweight, high-performance parts that are essential in aerospace applications, such as turbine blades, engine components, and airframe parts. The ability to produce intricate internal geometries—like cooling channels within engine parts—allows for more efficient designs that improve performance and reduce weight.
Automotive Industry
In the automotive industry, 3D printing for metal casting is helping manufacturers produce complex engine components, exhaust systems, and transmission parts. The automotive sector benefits from the ability to quickly iterate designs and create custom, low-volume parts for prototype vehicles. With the demand for lighter, stronger, and more fuel-efficient vehicles, 3D-printed metal castings help achieve these goals while reducing manufacturing costs.
Healthcare and Medical Devices
In healthcare, 3D printing is used for custom metal parts like surgical tools, implants, and prosthetics. 3D printing allows for highly precise and customized parts tailored to individual patient needs. Metal casting using 3D-printed molds can create components with complex geometries, such as porous structures for implants, which can promote better integration with bone tissue in orthopedic surgeries.
Tooling and Mold Making
Beyond casting finished parts, 3D printing also offers significant benefits in tooling and mold making. The ability to quickly produce casting molds or investment patterns with 3D printing enables faster tooling changes and more efficient production workflows. For example, manufacturers can print sand molds for casting parts or create wax patterns for investment casting.
Challenges and Considerations of 3D Printing for Metal Casting
While 3D printing for metal casting is evolving, the materials used in 3D printing can still be relatively expensive. Metal powders and materials, while offering exceptional strength and thermal properties, are costly compared to traditional casting materials. Additionally, the range of metals available for 3D printing is still somewhat limited compared to the wide variety of alloys that can be used in conventional casting.
Post-Processing Requirements
3D printing produces highly detailed molds, but the resulting cast parts often require significant post-processing. This can include removing support structures, polishing surfaces, or performing heat treatments to ensure the part meets its final specifications. These additional steps add time and cost to the process, which must be carefully considered in the overall production strategy.
Size and Scale Limitations
Although 3D printing provides a great deal of flexibility in design, it still has some size limitations. Many 3D printers can only produce parts within a certain size range, and for larger casting molds, several sections may need to be printed separately and then assembled. This can complicate the process for manufacturers needing large parts and may impact the efficiency of the process.
Future of 3D Printing in Metal Casting
As the technology behind 3D printing continues to advance, we can expect to see even greater capabilities in terms of material options, printing speeds, and precision. New alloys and advanced metal powders will likely expand the range of applications for 3D printing in metal casting, particularly in industries requiring high-strength, high-temperature materials.
Integration with Smart Manufacturing
In the coming years, 3D printing for metal casting will likely become an integral part of smart manufacturing systems. With advancements in AI, machine learning, and robotics, the entire process—from digital design to post-processing—could become more automated and optimized, leading to faster production times, lower costs, and fewer errors.
Sustainability and Eco-Friendly Practices
Another promising development is the potential for 3D printing to promote sustainability in metal casting. The ability to produce only the required amount of material, reduce waste, and optimize designs for energy efficiency could help mitigate the environmental impact of traditional casting processes. As industries place greater emphasis on sustainability, 3D printing could play a crucial role in making metal casting more eco-friendly.
Conclusion
3D printing for metal casting is a transformative technology that is reshaping industries by offering more efficient, cost-effective, and innovative ways to produce complex metal parts. With its ability to reduce lead times, improve precision, and enable the creation of intricate geometries, 3D printing has proven itself to be a valuable tool in modern manufacturing. As the technology continues to evolve, the possibilities for its application in metal casting are boundless. From aerospace to healthcare, 3D printing is helping companies stay competitive in an increasingly demanding market, while opening new opportunities for design and production.