Brass is an alloy primarily made of copper and zinc, although it can also contain small amounts of other metals like lead, tin, or iron. The ratio of copper to zinc determines the brass’s properties, such as its strength, corrosion resistance, and color. Typically, brass contains anywhere from 55% to 95% copper, with the remaining percentage being zinc.
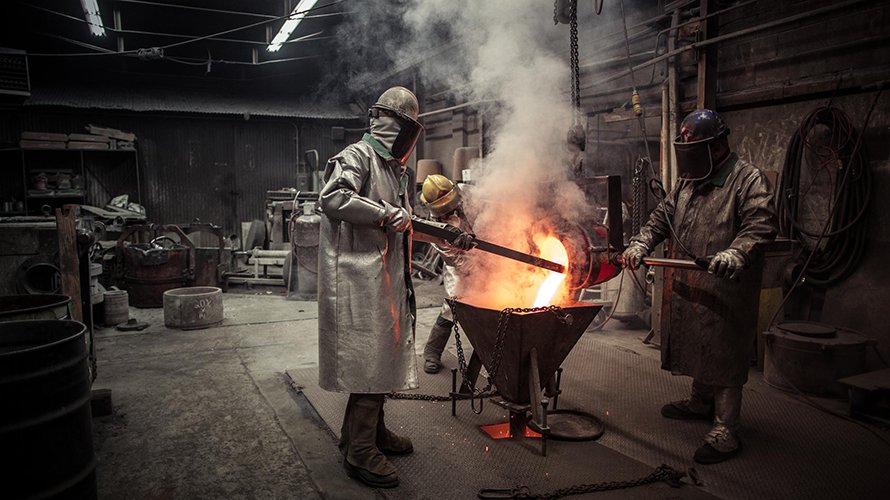
Properties of Brass
Brass has several desirable properties that make it ideal for metal casting, including:
· Corrosion Resistance: Brass is highly resistant to corrosion, particularly in water and marine environments.
· Malleability: Brass is easy to mold and shape, which is essential for casting intricate parts.
· Aesthetic Appeal: Brass has an attractive, yellowish appearance that resembles gold, making it popular for decorative items.
· Durability: Brass parts are durable and can withstand stress and wear over time.
Why Choose Brass for Casting?
Brass’s combination of strength, appearance, and corrosion resistance makes it suitable for a wide range of applications, from machinery parts to decorative fittings. In industries like automotive, aerospace, and plumbing, bras castings play a critical role in ensuring both functionality and longevity.
The Process of Metal Casting Brass
Sand casting is one of the most commonly used methods for brass casting. The process involves creating a mold from a mixture of sand and binder material. The molten brass is poured into the mold, where it solidifies and takes on the desired shape. Sand casting is ideal for both large and small parts and offers great flexibility in design.
Investment Casting (Lost Wax Casting)
Investment casting is another popular method for creating brass parts, particularly for intricate designs. In this method, a wax model of the part is coated in a ceramic shell. Once the shell hardens, the wax is melted and drained out, leaving a hollow mold that is then filled with molten brass. Investment casting offers high precision and excellent surface finish, making it suitable for detailed components.
Die Casting
In die casting, molten brass is forced into a steel mold under high pressure. The mold is typically made of two parts, and once the brass cools and solidifies, the mold is opened to reveal the final part. Die casting is perfect for mass production and is commonly used for parts that require high dimensional accuracy.
Continuous Casting
Continuous casting is a process in which brass is continuously poured into a mold, allowing for the creation of long sections of brass, such as rods or bars. This method is efficient for producing large quantities of the same part and is often used in industrial applications.
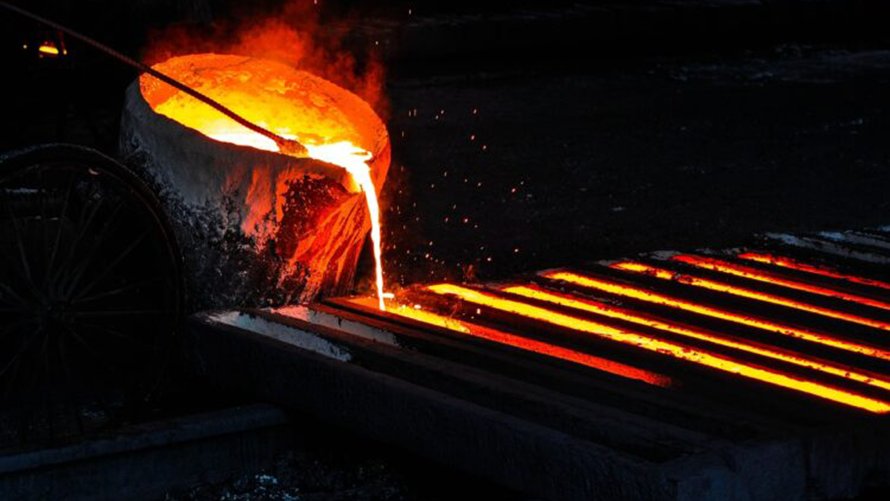
Applications of Brass Castings
Brass is commonly used for industrial applications such as:
· Gears and Bearings: The self-lubricating properties of brass make it an excellent choice for gears and bearings in machinery.
· Automotive Components: Brass is used for components like radiator cores, fuel system parts, and electrical connectors due to its durability and corrosion resistance.
· Plumbing Fittings: Brass is a common material for faucets, valves, and other plumbing fittings, as it is resistant to corrosion from water exposure.
Aesthetic and Decorative Applications
In addition to its practical applications, brass is frequently used in decorative items such as:
· Jewelry: Brass’s golden color and durability make it a popular choice for jewelry and fashion accessories.
· Architectural Details: Brass is often used for decorative elements in architecture, such as door hardware, light fixtures, and trim.
· Musical Instruments: Many brass musical instruments, such as trumpets and saxophones, are made from a brass alloy due to its resonance and aesthetic appeal.
Marine and Aerospace Applications
The corrosion resistance of brass makes it ideal for harsh environments, such as marine and aerospace industries. Brass castings are used in components that need to withstand exposure to saltwater or extreme temperatures, such as:
· Marine Hardware: Propellers, pump parts, and valves in marine environments are often made from brass due to its resistance to corrosion.
· Aerospace Parts: Brass is also used in aerospace applications for fittings, connectors, and valves that need to perform reliably under extreme conditions.
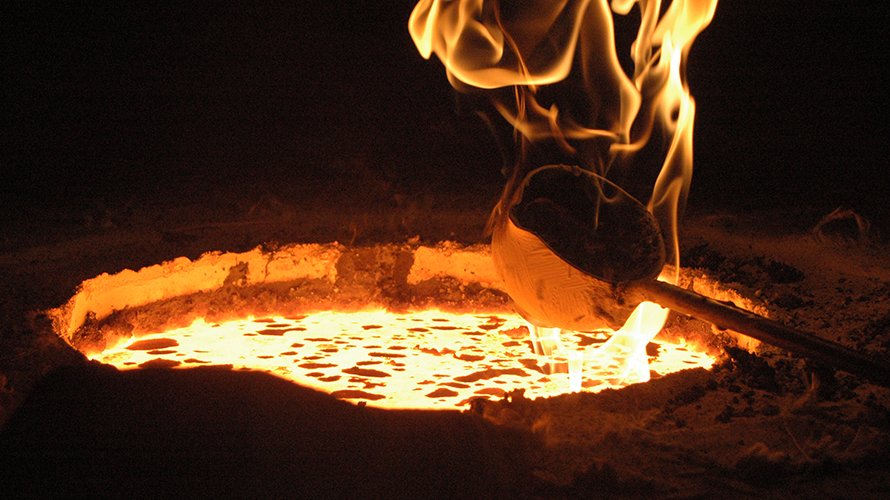
Advantages and Challenges of Brass Casting
· Excellent Durability: Brass castings are durable and resistant to wear, making them suitable for high-stress applications.
· Corrosion Resistance: Brass offers excellent resistance to corrosion, particularly in wet or salty environments, making it a preferred material in marine and plumbing applications.
· Aesthetic Value: Brass has a unique, attractive finish that is often valued for its visual appeal, especially in decorative items.
· Ease of Machining: Brass is easy to machine and work with, which makes it ideal for manufacturing parts that require precision.
Challenges of Brass Casting
· Cost: Brass is generally more expensive than other metals like aluminum or steel, especially in high quantities.
· Casting Defects: As with all casting processes, brass castings can suffer from defects like porosity, shrinkage, or surface imperfections, which require careful control of the casting process.
· Weight: Brass is heavier than other metals like aluminum, which can be a disadvantage for applications where weight is a critical factor.
Conclusion
Brass casting is a versatile and effective method for producing a wide range of components, from industrial parts to decorative items. With its strong, durable, and corrosion-resistant properties, brass continues to be a favored choice in various industries. Understanding the casting methods and applications of brass will help you make informed decisions when choosing this material for your projects. Whether you are producing parts for machinery or creating intricate jewelry, brass offers both functionality and aesthetic value that make it an excellent option for casting.