Metal casting is an ancient yet highly refined technique used in manufacturing a wide range of parts and products. From car engine components to jewelry and industrial machinery, metal casting plays a crucial role in the production of complex parts with high precision. Whether you are a manufacturer, engineer, or simply curious about the process, this blog will provide an in-depth understanding of metal casting—what it is, how it works, and the benefits it offers.
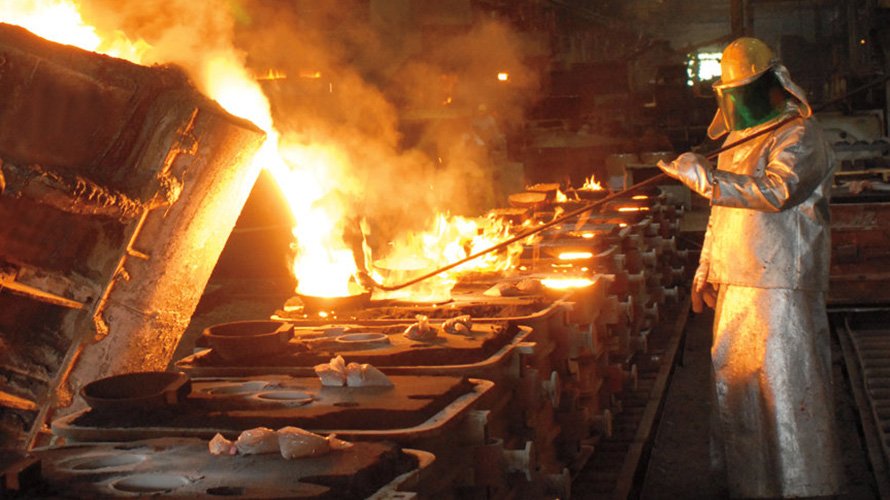
What is Metal Casting?
Metal casting is the process of pouring liquid metal into a mold to create a specific shape or form once it cools and solidifies. This technique has been used for thousands of years, dating back to ancient civilizations where molten metals were poured into stone or clay molds to create everything from weapons to decorative items.
The primary goal of metal casting is to create complex and detailed parts that are difficult or impossible to make with other manufacturing processes like machining or forging. Casting is essential for industries such as automotive, aerospace, construction, and energy, where precision and quality are paramount.
Types of Metals Used in Casting
The metal used in the casting process can vary depending on the product being created. Some of the most commonly used metals in casting include:
· Iron: Particularly cast iron and ductile iron, which are used in automotive and industrial applications.
· Aluminum: Known for its lightweight and corrosion-resistant properties, aluminum casting is commonly used in aerospace, automotive, and consumer goods.
· Copper: Brass and bronze, which are copper alloys, are often used for decorative and structural applications.
· Steel: Used for high-strength, high-durability parts like engine blocks or structural components in heavy machinery.
· Zinc: Typically used in die casting for producing high-precision parts with thin walls.
Each metal offers its unique properties and is chosen based on the specific requirements of the part being produced, such as strength, weight, or heat resistance.
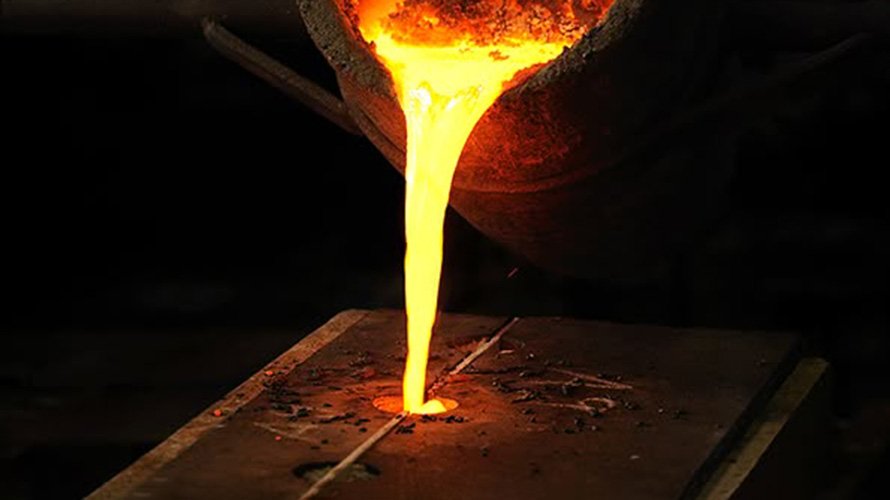
The Metal Casting Process
The first step in the casting process is the creation of a pattern. A pattern is a replica of the final product, typically made from metal, wood, or plastic. The pattern is designed to be slightly larger than the finished part to account for shrinkage during cooling.
In some cases, a mold is made directly from the pattern, while in others, it may be used to form a sand mold or a die for more precise casting methods.
Mold Preparation
Once the pattern is complete, a mold is made to shape the liquid metal into the desired form. There are several types of molds used in metal casting:
· Sand Mold: A mixture of sand and binder is packed around the pattern, creating a mold that can be broken away after the metal has solidified.
· Die Casting Mold: A reusable mold is used, typically made of high-strength steel, for more intricate or high-volume parts.
· Shell Mold: A mold made from a fine ceramic material that allows for very precise and smooth castings.
The type of mold used depends on the production volume, complexity of the part, and the material being cast.
Pouring the Metal
Once the mold is prepared, the next step is pouring the molten metal into the mold. The metal is heated until it reaches a liquid state, typically in a furnace, and then poured into the mold through a pouring basin and channels designed to ensure an even distribution of molten metal.
The temperature, speed, and precision of pouring are critical, as any inconsistencies can lead to defects like air pockets or incomplete filling, which affect the strength and durability of the final part.
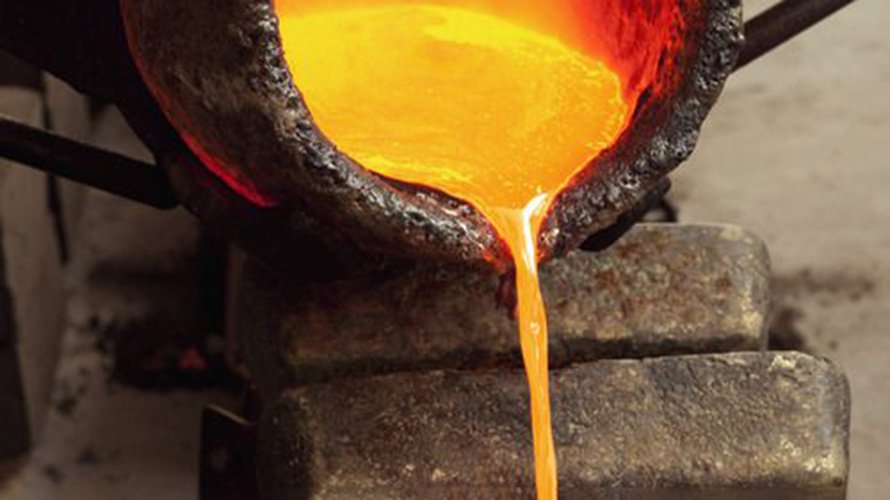
Cooling and Solidification
After the molten metal is poured into the mold, it begins to cool and solidify. The cooling rate varies depending on the type of metal, the size of the casting, and the type of mold used. It’s important to control the cooling process because uneven cooling can cause internal stresses or distortions in the casting.
Once the metal has solidified, the mold is broken open to reveal the cast part.
Finishing and Inspection
After the part has been removed from the mold, it undergoes finishing processes to remove any excess material, smooth rough edges, and ensure that the final part meets dimensional and surface quality requirements. Common finishing steps include:
· Grinding: Used to smooth out rough surfaces and sharp edges.
· Machining: Used to achieve precise dimensions or add additional features like holes or threads.
· Heat Treatment: Used to alter the metal’s physical properties, such as hardness and strength, depending on the intended application.
Once finished, the part undergoes inspection to ensure it meets the required specifications. This may include visual inspection, dimensional checks, and sometimes non-destructive testing techniques like x-ray or ultrasonic testing.
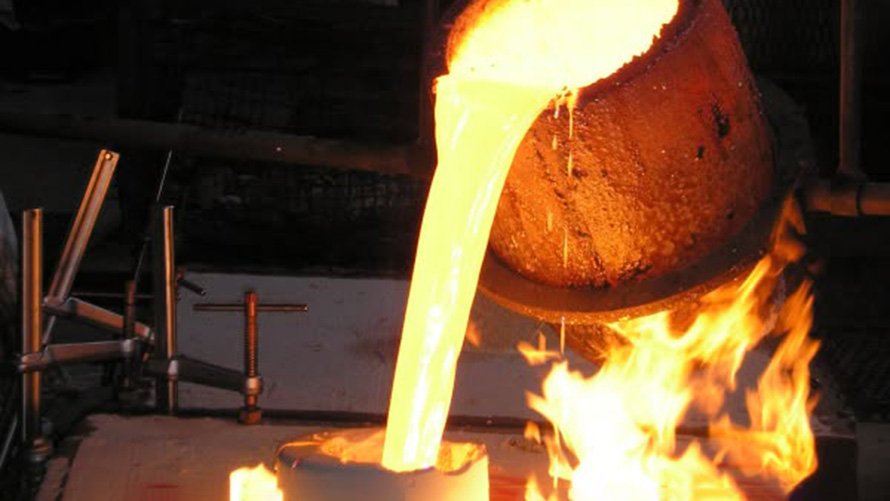
Advantages of Metal Casting
One of the primary advantages of metal casting is its ability to produce parts with complex geometries that would be difficult or impossible to create using other methods. For example, intricate internal features, thin walls, and detailed surface textures can be molded into the part without the need for additional manufacturing steps.
This capability is especially beneficial in industries like automotive and aerospace, where parts must fit into specific configurations and operate in challenging conditions.
Cost-Effectiveness for High-Volume Production
For large-scale manufacturing, metal casting can be a highly cost-effective method. Once the pattern and mold are created, the process can be repeated many times, allowing for high-volume production without significant increases in cost. This makes metal casting an ideal choice for parts that need to be produced in large quantities.
In addition, molds for casting processes like sand casting and die casting are durable and can be reused multiple times, further reducing production costs over time.
Versatility in Material Choices
Metal casting offers great versatility in terms of the materials that can be used, making it suitable for a wide range of applications. Different metals and alloys can be used depending on the desired properties of the finished part, including strength, corrosion resistance, or electrical conductivity.
For example, aluminum casting is favored for lightweight applications, while steel or iron casting is preferred for high-strength, durable parts. The ability to use various metals and alloys allows for a more customized approach to product development.
Reduced Material Waste
In comparison to processes like machining, which may involve cutting away large amounts of material, metal casting is more efficient in terms of material usage. Most of the material used in the casting process becomes part of the finished product, reducing waste and making it an environmentally friendlier option. The advent of advanced techniques like 3D printing for patterns and molds further reduces material waste and increases efficiency.
High Precision and Repeatability
Casting is known for producing parts with high precision, especially with methods like die casting, which are ideal for creating parts with tight tolerances and smooth surface finishes. The repeatability of the casting process makes it particularly suitable for mass production, where consistency across large batches of parts is critical.
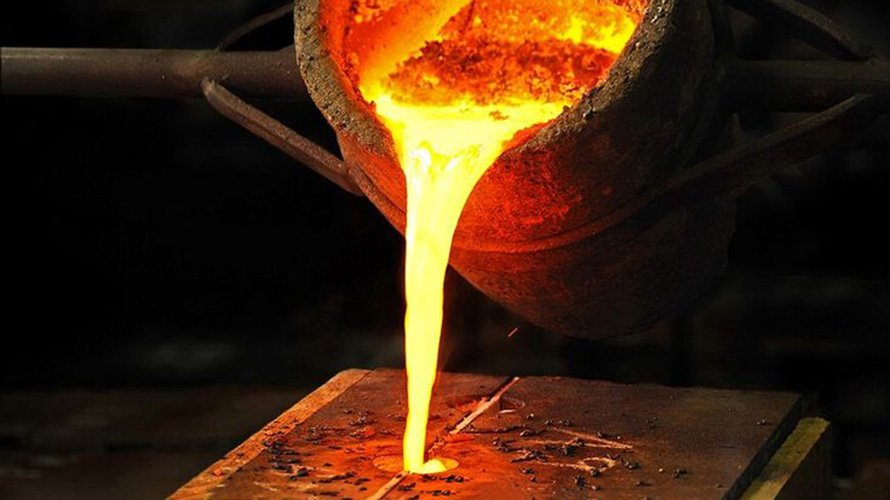
Conclusion
Metal casting is a cornerstone of modern manufacturing, allowing industries to create complex, high-quality parts efficiently and at scale. Whether you're looking to produce small, intricate parts for electronics or large, durable components for machinery, metal casting offers a versatile, cost-effective solution. By understanding the casting process and its advantages, you can better appreciate how this ancient technique has evolved to meet the demands of contemporary industry.
Whether you're involved in the design and production of cast parts or are simply looking to understand more about this vital process, metal casting remains one of the most efficient and adaptable methods of manufacturing available today.