The casting industry relies on various processes to create metal components, each with unique characteristics and advantages. Among these, investment casting and sand casting are two of the most widely used techniques. This blog delves into the differences, applications, and benefits of each method, helping manufacturers and engineers choose the best solution for their needs.
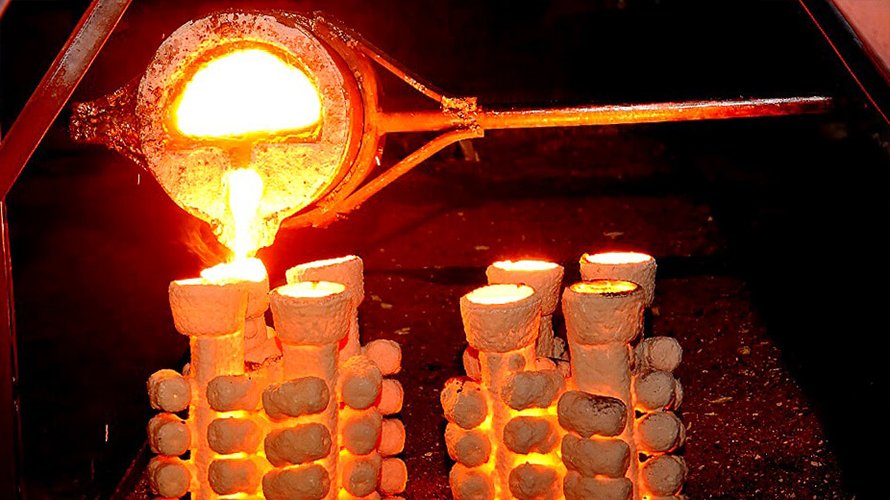
Understanding Investment Casting
Investment casting, also known as lost-wax casting, is a precision manufacturing process that dates back thousands of years. Despite its ancient origins, this method has evolved into a highly sophisticated technique, widely used across industries today.
The Investment Casting Process
Investment casting involves creating a wax pattern of the desired part. This wax model is coated with a ceramic shell to form a mold. Once the ceramic hardens, the wax is melted out, leaving a cavity for molten metal. After pouring and cooling, the mold is broken to reveal the final product.
Key steps include:
Crafting the wax pattern.
Building the ceramic mold through repeated dipping and drying.
Removing the wax and pouring molten metal.
Breaking the mold to retrieve the cast part.
Advantages of Investment Casting
Investment casting is renowned for its ability to produce intricate designs with exceptional dimensional accuracy. It can:
Accommodate complex geometries with fine details.
Achieve excellent surface finishes, reducing the need for secondary machining.
Work with a wide range of metals and alloys, including those difficult to machine.
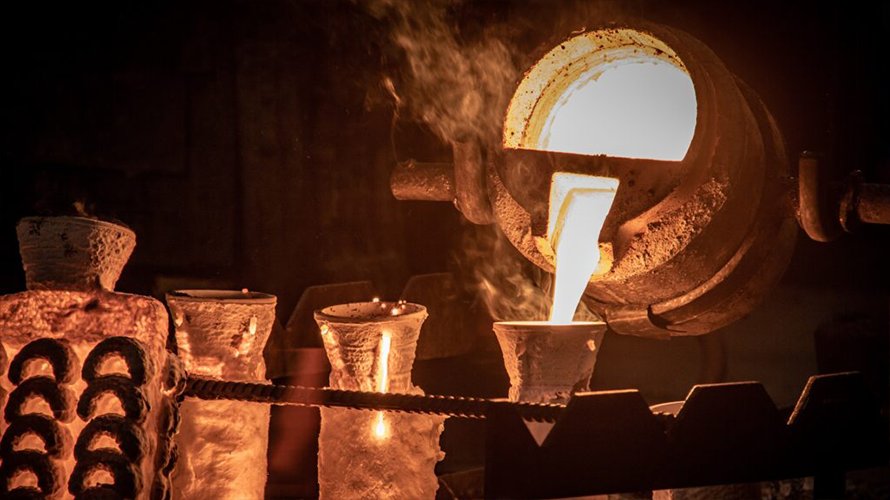
Understanding Sand Casting
Sand casting is one of the oldest and most versatile casting methods. It is widely used for producing large, heavy components and simpler designs.
The Sand Casting Process
The sand casting process involves creating a mold from a mixture of sand and a binding agent. The mold cavity is formed by compressing sand around a pattern. Once the mold is ready, molten metal is poured into it. After cooling, the sand mold is broken to extract the cast part.
Steps in sand casting include:
Preparing the sand mold with a pattern.
Pouring molten metal into the mold cavity.
Allowing the metal to cool and solidify.
Breaking the mold to retrieve the casting.
Advantages of Sand Casting
Sand casting is valued for its simplicity and flexibility. Benefits include:
Cost-effectiveness for low-quantity production.
The ability to cast large, heavy parts.
Compatibility with a wide range of metals.
Short lead times compared to other casting methods.
Key Differences Between Investment Casting and Sand Casting
While both methods are essential to the casting industry, they differ significantly in terms of process, applications, and outcomes.
Dimensional Accuracy and Surface Finish
Investment casting is ideal for intricate designs and detailed components. Its ceramic molds allow for tight tolerances and smooth finishes, making it suitable for aerospace, medical, and automotive applications. In contrast, sand casting generally produces rougher surfaces and requires post-casting machining for finer details.
Production Size and Scale
Sand casting excels in producing large, heavy parts, such as engine blocks and industrial machinery components. Investment casting, on the other hand, is better suited for smaller, precision parts with complex shapes.
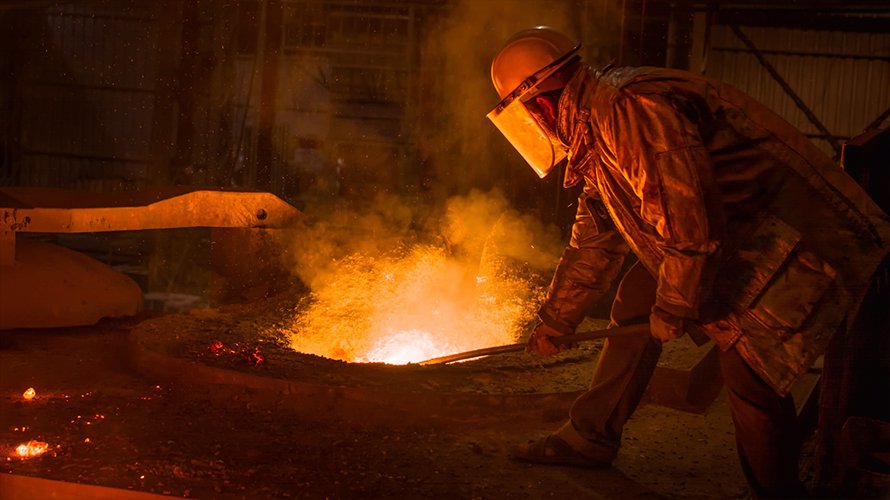
Material Versatility
Both methods accommodate a variety of metals. However, investment casting offers greater flexibility with high-performance alloys, making it suitable for demanding applications. Sand casting, while versatile, is often used with more common metals like aluminum, iron, and steel.
Cost Considerations
Investment casting tends to have higher upfront costs due to the intricate mold-making process. However, it reduces secondary machining expenses. Sand casting, being simpler and more cost-effective initially, is ideal for lower budgets and short production runs.
Applications of Investment Casting
Investment casting is used across various industries for its precision and adaptability.
Aerospace and Defense
In aerospace, investment casting is essential for producing turbine blades, engine components, and other high-precision parts. The process ensures that these critical components meet stringent quality and performance standards.
Medical Devices
The medical industry relies on investment casting for intricate surgical instruments and implants. Its ability to produce small, complex parts with biocompatible materials makes it invaluable.
Automotive and Industrial Sectors
Automotive manufacturers use investment casting for gears, housings, and structural components that demand tight tolerances. The process also supports industrial applications requiring high-performance alloys.

Applications of Sand Casting
Sand casting’s versatility makes it a popular choice for diverse industrial applications.
Automotive Manufacturing
Sand casting is widely used in the automotive sector for producing large components like engine blocks, transmission cases, and cylinder heads. Its capacity for high-volume production meets the industry’s demands efficiently.
Construction and Infrastructure
The construction industry benefits from sand casting in creating structural components such as beams, columns, and connectors. Its ability to cast large and heavy parts ensures durability and strength.
Heavy Machinery
Manufacturers of heavy equipment rely on sand casting for machine bases, housings, and other robust components. The method’s cost-effectiveness for large-scale production makes it indispensable.
Choosing Between Investment Casting and Sand Casting
Selecting the right casting method depends on several factors, including the project’s requirements, budget, and production scale.
When to Choose Investment Casting
Investment casting is ideal for projects that require:
Complex geometries and fine details.
High precision and tight tolerances.
Superior surface finishes.
Use of high-performance alloys.
When to Choose Sand Casting
Sand casting is suitable for:
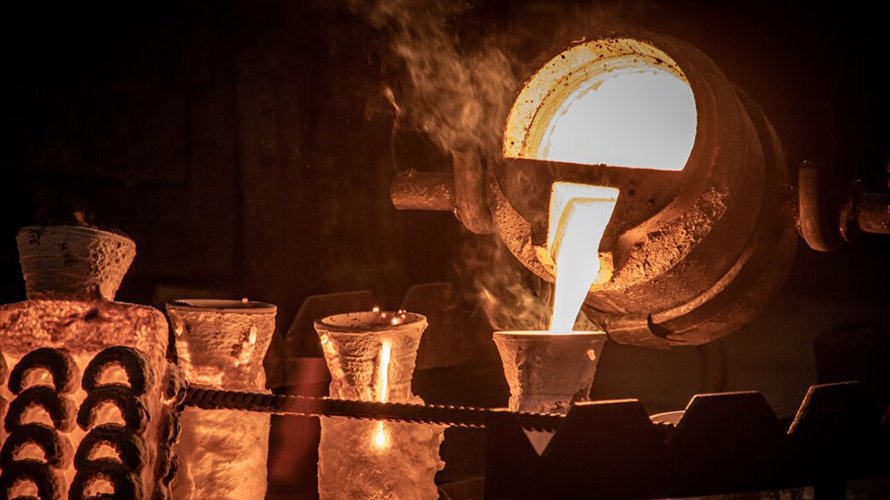
Modern Advancements in Casting Methods
Both investment casting and sand casting have evolved significantly, incorporating advanced technologies to improve efficiency and quality.
Automation and Digital Integration
Modern foundries employ automation, robotics, and computer-aided design (CAD) to streamline casting processes. These technologies enhance precision, reduce waste, and shorten lead times.
Material Science Innovations
Advancements in material science have expanded the range of alloys available for casting. High-strength, lightweight, and heat-resistant materials cater to the demands of industries such as aerospace and automotive.
Sustainability Efforts
Both casting methods are becoming more sustainable through the recycling of materials, energy-efficient processes, and waste reduction initiatives. These efforts align with global sustainability goals and reduce environmental impact.
Conclusion
Investment casting and sand casting are indispensable to the metalworking industry, each offering unique advantages. Investment casting stands out for its precision and ability to handle complex designs, making it ideal for high-performance applications. Sand casting, on the other hand, excels in producing large, heavy components cost-effectively.
Choosing between these methods requires a careful assessment of project requirements, budget, and production scale. With ongoing advancements in technology and materials, both processes continue to evolve, meeting the needs of modern industries while driving innovation and sustainability.
Whether you’re designing intricate aerospace components or constructing durable industrial machinery, understanding the strengths of investment casting and sand casting will guide you toward the best manufacturing solution.