Metal casting is a fundamental process in manufacturing, providing the ability to create complex and precise metal components. Among the various casting techniques, investment casting and centrifugal casting are two widely used methods, each with distinct benefits and applications. Whether you are designing high-precision aerospace parts or durable industrial components, understanding the differences between these two casting methods is crucial. In this blog, we will explore the unique characteristics of investment casting and centrifugal casting, comparing their processes, advantages, and ideal applications.
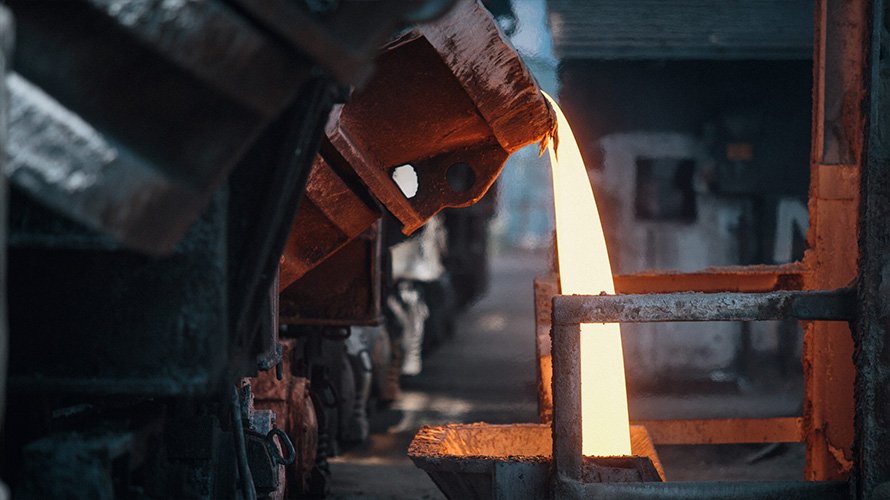
What is Investment Casting?
Investment casting, also known as lost wax casting, is a method that involves creating a detailed pattern from a wax or polymer material, which is then covered in a ceramic shell. After the shell hardens, the pattern is melted away, leaving a hollow cavity into which molten metal is poured. This process allows for the production of complex and high-precision components with excellent surface finishes and minimal material waste.
Investment Casting Process
The investment casting process begins with creating a pattern, typically made from wax or a similar material. Once the pattern is formed, it is coated with a ceramic slurry. The slurry is hardened and then baked at high temperatures to form a strong shell. Afterward, the wax is melted and drained out, leaving a precise cavity that is ready to receive molten metal. The metal is poured into this mold and allowed to cool, after which the ceramic shell is broken away, revealing the cast part.
Advantages of Investment Casting
Investment casting offers several advantages, making it ideal for high-precision components. One of the most significant benefits is the ability to produce intricate geometries that would be difficult or impossible to achieve with other casting methods. Additionally, investment casting allows for tight tolerances and excellent surface finishes, reducing the need for additional machining. It is particularly useful for producing parts in small to medium quantities where precision and complexity are paramount.
Ideal Applications of Investment Casting
Investment casting is commonly used in industries that require high-precision, intricate parts. These include aerospace, medical devices, automotive, and defense sectors, where the need for durability and accuracy is non-negotiable. The process is especially suitable for producing turbine blades, valve bodies, and other small, detailed components that require strength and durability.
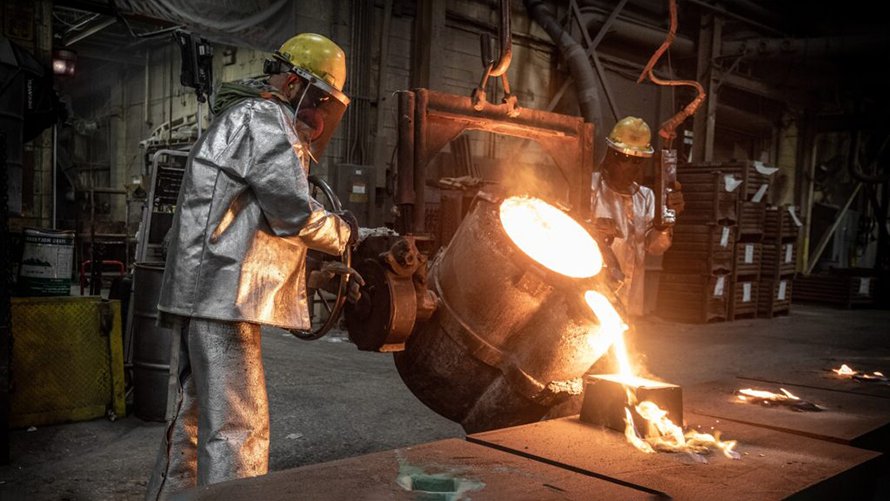
What is Centrifugal Casting?
Centrifugal casting, as the name suggests, uses centrifugal force to mold molten metal into cylindrical parts. In this process, a mold is rotated at high speeds while molten metal is poured into it. The force of rotation pushes the metal towards the mold's walls, forming a dense, strong outer layer. As the metal cools, it solidifies into the desired shape. Centrifugal casting is especially useful for producing cylindrical or tubular parts that require uniform thickness and high strength.
Centrifugal Casting Process
The process of centrifugal casting begins by placing a mold (typically made of metal or sand) on a rotating spindle. The mold is spun at high speeds to generate centrifugal force. As molten metal is poured into the mold, the centrifugal force causes the metal to move outward, filling the mold’s cavity while pushing impurities toward the center. The result is a casting with a dense and strong outer layer and a relatively hollow center. This method can produce components with a high degree of homogeneity in material properties.
Advantages of Centrifugal Casting
Centrifugal casting offers several unique benefits, particularly when it comes to producing cylindrical parts. The centrifugal force naturally compacts the metal, resulting in a highly uniform material structure with minimal porosity and fewer defects. This process also allows for thicker walls and larger diameters compared to other casting methods, making it ideal for producing parts like pipes, tubes, and rings. Additionally, centrifugal casting typically involves lower tooling costs, which can be advantageous for high-volume production.
Ideal Applications of Centrifugal Casting
Centrifugal casting is often used for manufacturing parts that require high strength, uniformity, and the ability to withstand harsh conditions. Industries like piping, mining, automotive, and nuclear power frequently use centrifugal casting for the production of components like cylindrical pipes, gears, liners, and turbine rings. The ability to create parts with uniform material properties makes this technique ideal for applications where performance and reliability are critical.
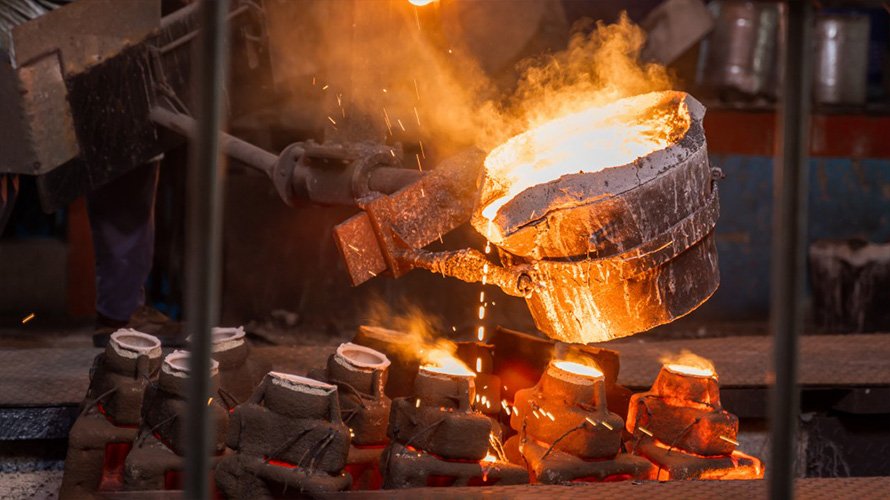
Key Differences Between Investment Casting and Centrifugal Casting
While both investment casting and centrifugal casting are effective methods for producing high-quality metal components, they differ significantly in their processes, advantages, and applications.
Process Complexity
The primary difference between the two methods is the complexity of the process. Investment casting requires the creation of a detailed pattern and the formation of a ceramic shell around it, making it a more intricate and labor-intensive process. In contrast, centrifugal casting involves pouring molten metal into a rotating mold, which is simpler and faster. This makes investment casting ideal for highly detailed parts, while centrifugal casting is better suited for parts with simpler geometries, particularly cylindrical shapes.
Material Homogeneity and Strength
Investment casting tends to produce parts with uniform material properties and excellent surface finishes, which are ideal for precision applications. However, the material can be more prone to porosity if not properly handled. In contrast, centrifugal casting's use of centrifugal force helps to create denser outer layers, reducing the risk of porosity and ensuring that parts have superior mechanical properties on the exterior. This makes centrifugal casting more suitable for parts that require high strength and durability in the outer layers.
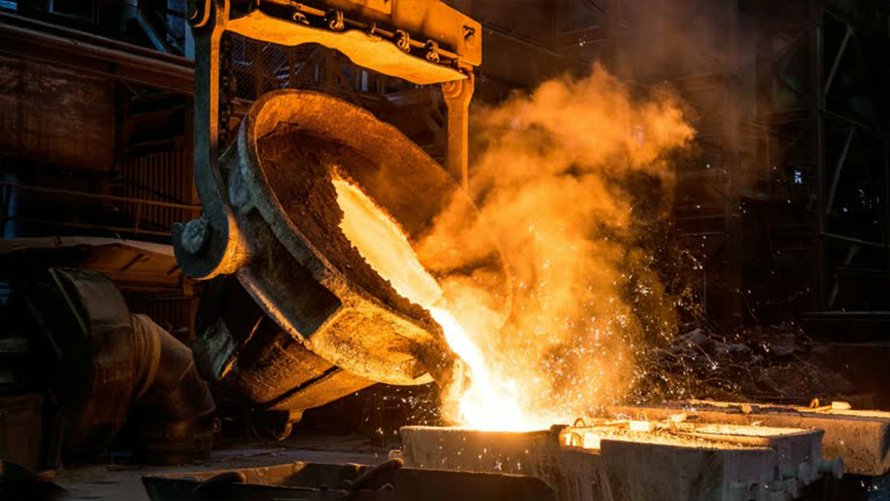
Cost Considerations: Which Casting Method is More Affordable?
When comparing the cost of investment casting versus centrifugal casting, several factors come into play. Investment casting is generally more expensive due to the complex pattern-making process and the need for high-quality molds and materials. However, its suitability for producing highly detailed, complex parts in small quantities makes it a cost-effective solution for specific applications.
Centrifugal casting, on the other hand, is generally more cost-effective for larger, simpler parts, especially in higher volumes. The lower tooling costs and shorter production times make it a more affordable option when producing cylindrical parts in bulk.
Tooling and Setup Costs
Investment casting typically requires expensive molds and tooling due to the complexity of the pattern-making and shell-building process. The initial setup can be more costly, but for small to medium production runs of intricate parts, it offers excellent value for money. Centrifugal casting, while having lower tooling costs, often requires high-capacity equipment that may be costly to operate and maintain.
Production Volume and Cost Efficiency
For high-volume production runs, centrifugal casting becomes increasingly cost-effective, especially when producing simple parts like pipes, tubes, or rings. The reduced material waste and faster cycle times contribute to cost savings. Conversely, investment casting is often more suitable for low to medium-volume production, where precision and intricate detail outweigh the higher initial setup costs.
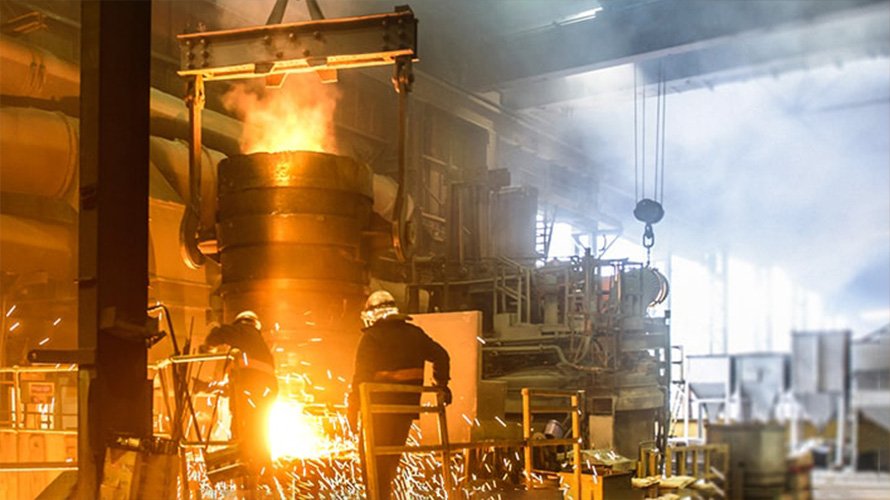
Choosing the Right Casting Method for Your Project
Choosing between investment casting and centrifugal casting depends largely on the specific requirements of your project. Key factors to consider include:
Part Complexity: If your part requires high precision and intricate features, investment casting is the best choice. For simpler, cylindrical shapes, centrifugal casting is often more efficient.
Material Properties: If you need parts with uniform density and high-strength outer layers, centrifugal casting is ideal. For applications requiring precise surface finishes and minimal post-processing, investment casting shines.
Production Volume: For small or medium production runs, investment casting provides high value, while centrifugal casting is more cost-effective for large-volume, simpler parts.
Conclusion
Both investment casting and centrifugal casting offer unique benefits, and each method is better suited for different applications. Investment casting excels at producing intricate, high-precision parts with excellent surface finishes, making it perfect for industries like aerospace, automotive, and medical devices. Centrifugal casting, on the other hand, is ideal for large-volume production of cylindrical or tubular parts, offering excellent material strength and uniformity at a lower cost.
Understanding the differences between these two casting methods is essential when selecting the right approach for your specific needs. Whether you prioritize precision, cost-effectiveness, or material properties, both investment casting and centrifugal casting have distinct advantages that can support your manufacturing goals.