Metal casting has been an essential manufacturing process for centuries, providing the backbone for industries such as automotive, aerospace, construction, and industrial machinery. Over the years, advancements in technology have significantly improved the efficiency, precision, and sustainability of metal casting. Innovations in materials, automation, digital modeling, and eco-friendly practices continue to reshape the industry. This article explores the latest trends and breakthroughs in metal casting technology that are driving the future of manufacturing.
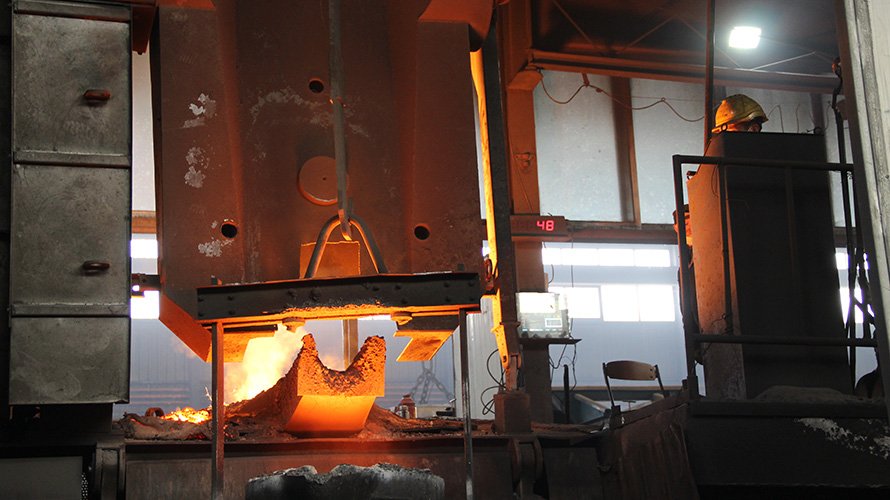
Advanced Casting Techniques
Additive manufacturing, particularly 3D printing, has transformed the metal casting industry by enabling the creation of complex molds and patterns with remarkable precision. By using sand, wax, or even direct metal printing, manufacturers can produce intricate components with reduced lead times and minimal material wastage.
Investment Casting with Enhanced Precision
Investment casting, also known as lost-wax casting, has seen significant innovations, including better ceramic shell materials and automation in wax pattern production. These advancements lead to improved accuracy, finer surface finishes, and greater consistency in high-precision applications such as aerospace and medical implants.
High-Pressure Die Casting Improvements
High-pressure die casting has evolved with the integration of vacuum-assisted technology, improving the density and structural integrity of metal parts. This trend is particularly beneficial for industries requiring lightweight yet strong components, such as automotive and consumer electronics.
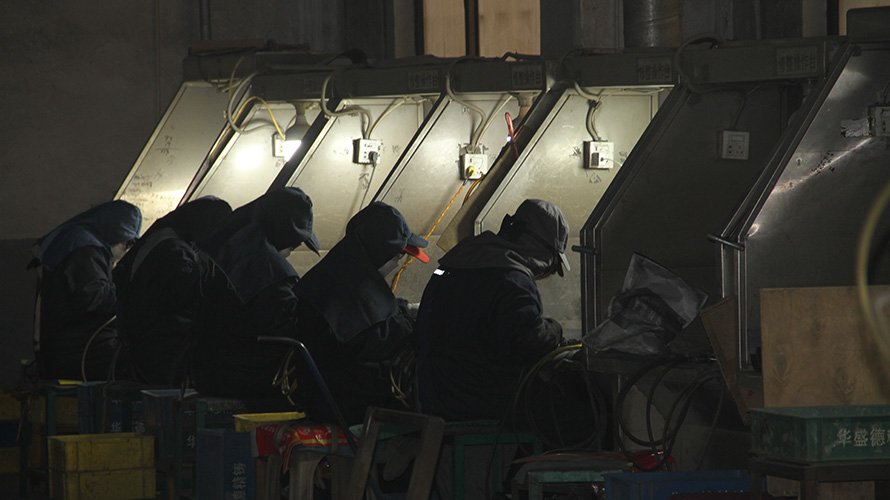
Smart Manufacturing & Automation
The Industrial Internet of Things (IIoT) has made a significant impact on foundries by enabling real-time monitoring of casting processes. Smart sensors and connected devices provide valuable data insights, allowing manufacturers to optimize efficiency, reduce defects, and minimize downtime.
Robotic Automation in Foundries
Robotics is revolutionizing metal casting through automated pouring, mold handling, and finishing processes. These robotic systems enhance precision, speed up production, and reduce the need for manual labor, improving workplace safety and consistency in manufacturing.
AI and Machine Learning in Quality Control
Artificial intelligence and machine learning are playing a crucial role in detecting defects and predicting potential failures in cast components. Advanced imaging and data analytics enable foundries to conduct real-time inspections, reducing scrap rates and ensuring higher-quality products.
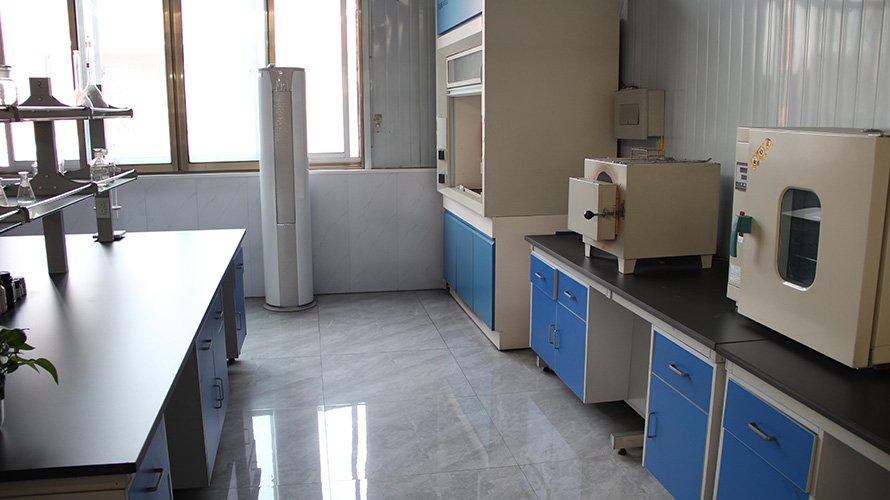
Sustainable Practices in Metal Casting
The push for sustainability has led to the development of biodegradable and recyclable casting materials. Foundries are experimenting with alternative sand compositions, organic binders, and environmentally friendly coatings to minimize the environmental impact of casting processes.
Energy Efficiency in Foundries
Energy consumption in metal casting is a major concern, prompting innovations in energy-efficient furnaces and heat recovery systems. Induction furnaces and regenerative burners are being widely adopted to lower fuel consumption and greenhouse gas emissions.
Waste Reduction & Recycling Initiatives
Sustainability efforts also focus on reducing waste and reusing casting byproducts. Many foundries now implement closed-loop recycling systems for sand, metals, and other materials, cutting costs and reducing landfill waste.
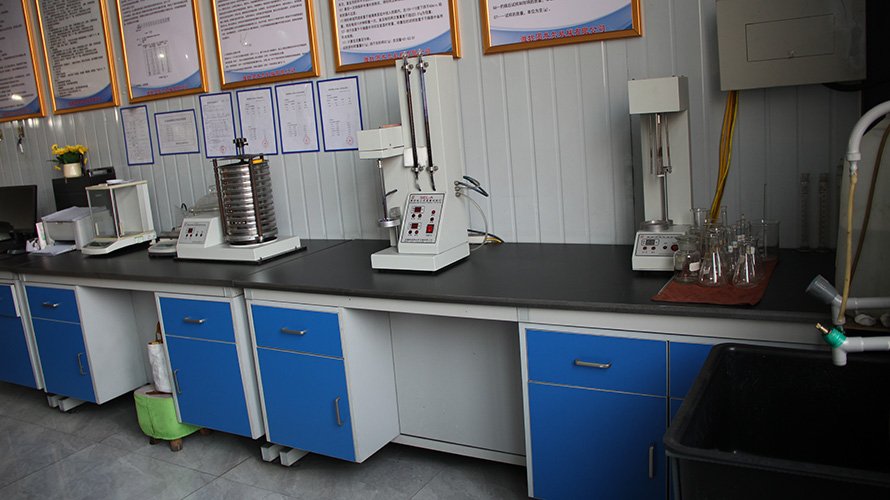
Future Outlook of Metal Casting Technology
Researchers are continuously developing new metal alloys with enhanced properties such as higher strength, better heat resistance, and improved machinability. These advancements expand the potential applications of cast components in demanding environments.
Digital Twin Technology in Casting
Digital twin technology is emerging as a game-changer in metal casting, enabling real-time simulations of casting processes. By creating virtual models of components and production lines, manufacturers can optimize designs, reduce errors, and improve efficiency.
Customized Casting Solutions for Industry 4.0
As industries move toward Industry 4.0, customized casting solutions are becoming more prevalent. Flexible manufacturing systems allow for the production of highly specialized components tailored to specific industrial needs, driving innovation and competitiveness in the metal casting sector.
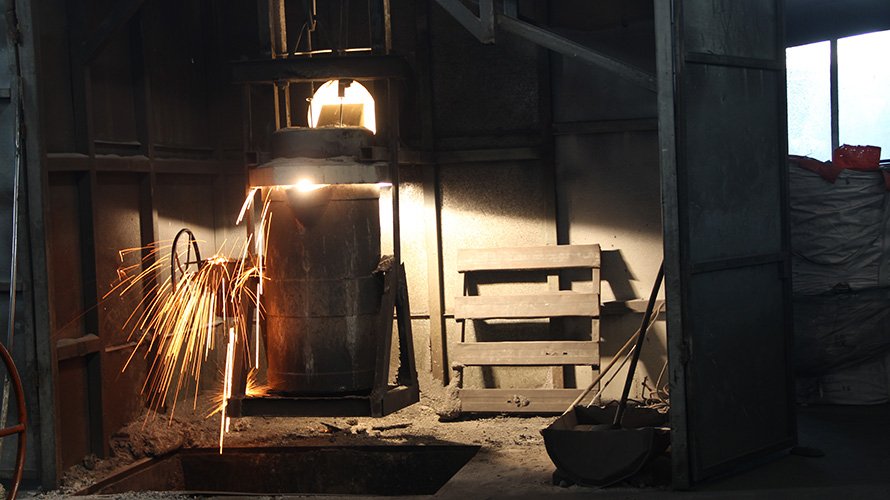
Conclusion
Metal casting is experiencing a transformation driven by technological advancements, automation, and sustainability initiatives. The integration of smart manufacturing, innovative materials, and eco-friendly practices ensures that the industry continues to evolve and meet the demands of modern manufacturing. By embracing these trends, foundries can enhance efficiency, reduce costs, and contribute to a more sustainable future in metal casting.