Metal casting is a fundamental manufacturing process used to create complex metal parts by pouring molten metal into a mold. To achieve high-quality castings, designers must consider multiple factors during the design phase. Proper metal casting design not only improves the structural integrity and performance of the final
product but also enhances manufacturability and cost efficiency. This article explores key aspects of metal casting design to ensure optimal results.
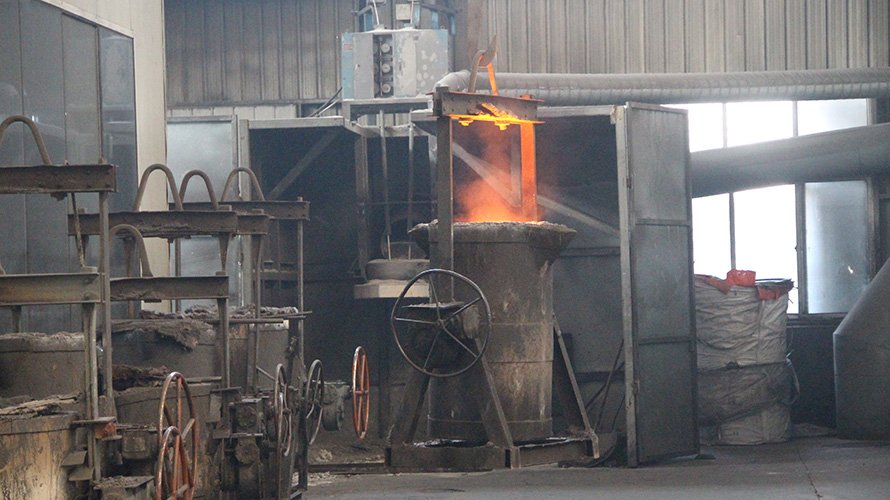
Material Selection and Properties
The selection of metal alloys significantly impacts the quality and functionality of the final cast product. Factors such as strength, corrosion resistance, thermal conductivity, and machinability should be evaluated based on the application requirements. Common casting materials include:
Iron-based alloys: Gray iron, ductile iron
Steel: Carbon steel, stainless steel
Non-ferrous metals: Aluminum, copper, magnesium, and zinc alloys
Thermal and Mechanical Properties
Understanding the thermal and mechanical properties of metals is essential to avoid defects such as shrinkage, warping, and cracking. Properties to consider include:
Castability of Materials
Different metals have varying degrees of castability, which affects their suitability for complex shapes. Factors such as fluidity, solidification behavior, and susceptibility to porosity should be considered when choosing a material.
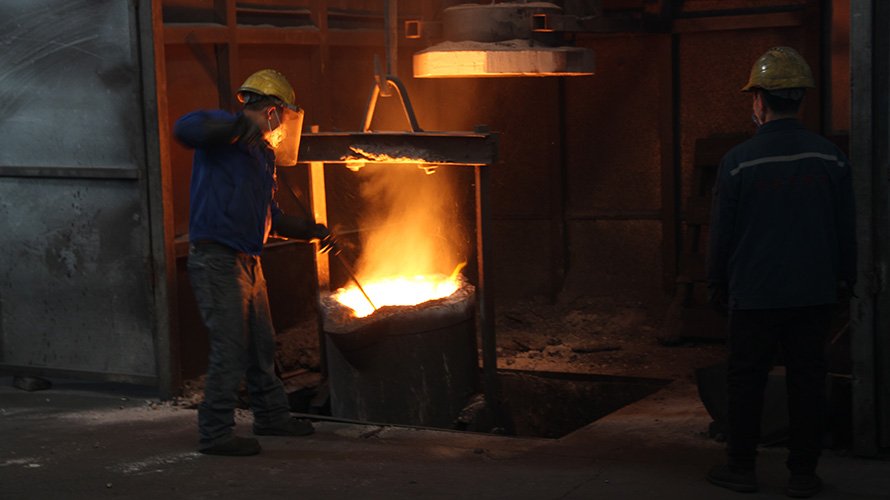
Mold and Pattern Design
The mold plays a critical role in metal casting as it defines the shape and surface quality of the final part. The choice of mold depends on factors like production volume, part complexity, and required dimensional accuracy. There are two primary types of molds:
Expendable molds: Sand casting, investment casting
Permanent molds: Die casting, gravity casting
Draft Angles and Parting Lines
Incorporating draft angles into the design facilitates the easy removal of the cast part from the mold. Without proper draft angles, the casting may experience defects or damage during extraction. Additionally, the positioning of the parting line must be carefully planned to avoid excessive flash or distortion.
Gate and Riser Placement
Gating and riser systems control the flow of molten metal into the mold and ensure complete filling. Proper placement prevents common defects such as:
Cold shuts: Incomplete fusion of metal streams
Shrinkage porosity: Caused by insufficient feeding of molten metal
Turbulence: Leading to trapped air and inclusions
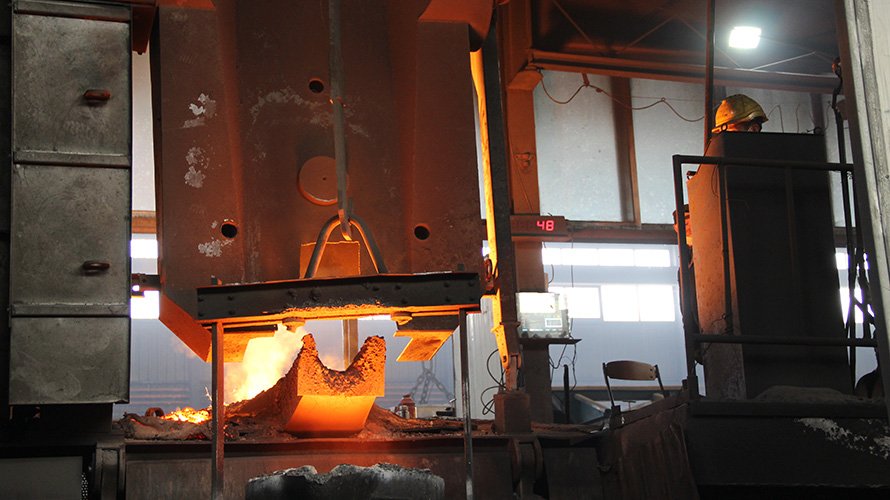
Solidification and Cooling Considerations
As metal cools and solidifies, it contracts, which can lead to shrinkage defects. To mitigate this, designers must:
Use risers to feed additional molten metal into shrinking areas
Optimize section thickness to promote uniform cooling
Incorporate fillets and radii to reduce stress concentration
Thermal Gradients and Heat Treatment
Managing thermal gradients is crucial in avoiding internal stresses and cracks. Some materials require post-casting heat treatment to improve mechanical properties. Common heat treatment processes include:
Annealing
Normalizing
Quenching and tempering
Simulation and Testing
Before production, conducting computer simulations of the solidification process helps predict defects and optimize design. Modern casting software can analyze factors like:
Mold filling behavior
Cooling rates
Stress distribution
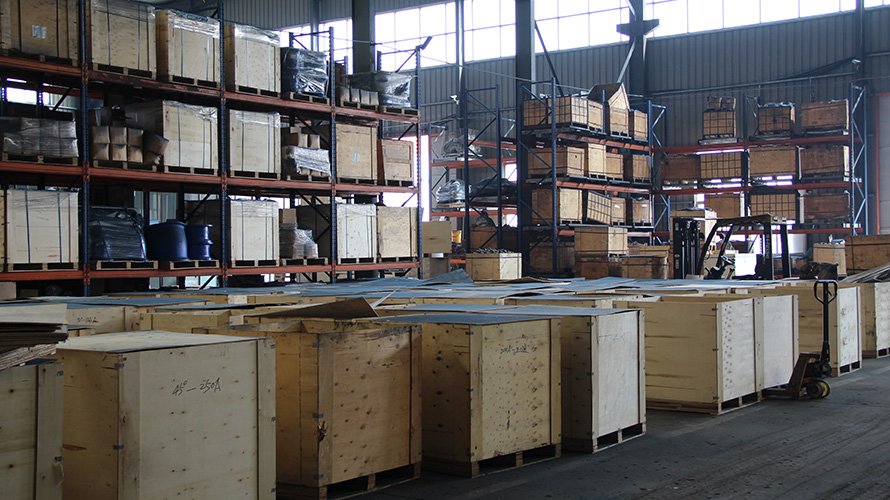
Design for Manufacturability and Cost Efficiency
Efficient casting design reduces material usage and post-processing requirements. Methods include:
Reducing Post-Casting Operations
To lower production costs, designers should consider reducing the need for extensive machining, polishing, or assembly. Net-shape or near-net-shape casting techniques can help achieve the final shape with minimal finishing work.
Mass Production vs. Custom Casting
The choice between mass production and custom casting impacts the design approach. For high-volume production, die casting or investment casting offers better consistency and efficiency. For specialized applications, sand casting or precision casting allows more design flexibility.
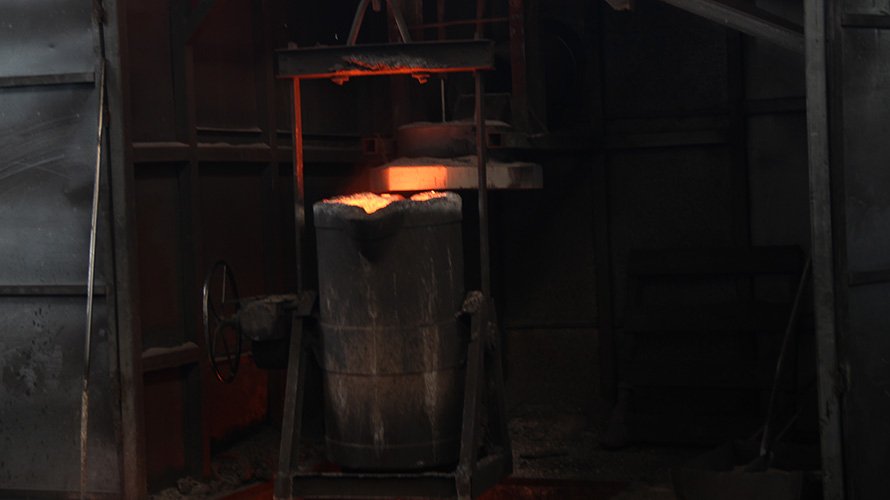
Conclusion
Effective metal casting design requires a deep understanding of materials, mold systems, cooling behavior, and manufacturability considerations. By carefully addressing these factors, manufacturers can achieve high-quality castings with minimal defects and optimal performance. Leveraging modern simulation tools and collaborating closely with foundries further enhances the success of metal casting projects. Whether designing for mass production or specialized applications, a well-thought-out approach ensures efficiency, reliability, and cost-effectiveness in metal casting processes.