Investment casting, also known as lost-wax casting, is a manufacturing process prized for its precision, ability to create intricate designs, and excellent surface finishes. However, selecting the right metal for investment casting is crucial to achieving the desired mechanical properties and functionality of the final product. In this blog, we’ll explore the metals commonly used in investment casting, their advantages, and how to choose the best material for specific applications.
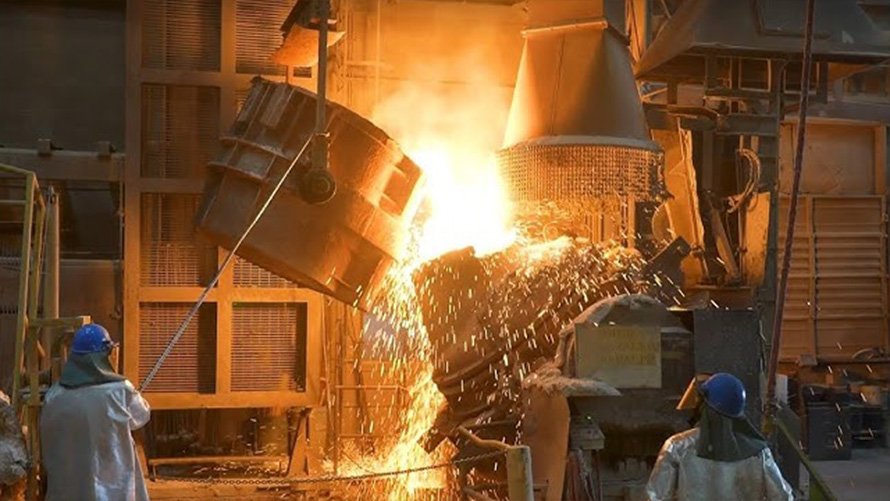
Why Material Selection Matters in Investment Casting
The material chosen for investment casting directly influences the strength, durability, and performance of the final component. Different metals offer unique mechanical properties, such as tensile strength, hardness, and corrosion resistance, making them suitable for various industrial applications. Understanding these properties helps manufacturers meet design and performance requirements effectively.
Matching Metals to Applications
Selecting the right metal ensures the cast part meets functional and environmental demands. For example, aerospace components require lightweight metals with high strength, while medical devices prioritize biocompatibility. The material also affects the ease of the casting process, including melting temperature and mold compatibility.
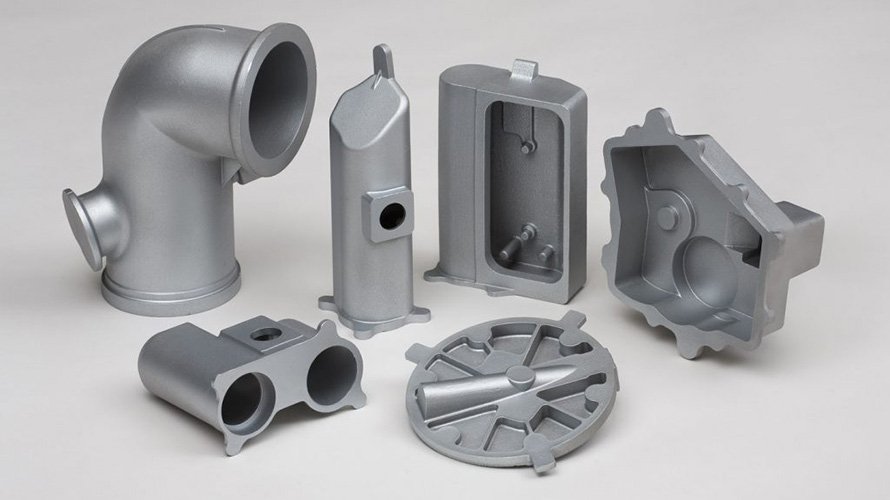
Metals Commonly Used in Investment Casting
Stainless steel is a popular choice for investment casting due to its excellent mechanical properties and versatility. It is widely used across industries that demand strength and corrosion resistance.
Grades of Stainless Steel
Different grades of stainless steel are available, each suited for specific applications. Austenitic stainless steels, such as 304 and 316, offer exceptional corrosion resistance, while martensitic grades provide enhanced hardness and wear resistance.
Applications of Stainless Steel in Investment Casting
Stainless steel is commonly used to produce components like valve bodies, impellers, and medical instruments. Its resistance to harsh environments makes it ideal for the chemical, marine, and food processing industries.
Carbon Steel
Carbon steel is another frequently used material for investment casting. Known for its strength and affordability, it is suitable for applications requiring high toughness and wear resistance.
Properties of Carbon Steel
The carbon content in steel significantly affects its characteristics. Low-carbon steels are malleable and easy to work with, while high-carbon steels offer superior strength and hardness but are less ductile.
Common Uses of Carbon Steel in Investment Casting
Carbon steel is often used to manufacture industrial machinery components, gears, and structural parts. Its affordability and reliability make it a go-to choice for high-volume production.
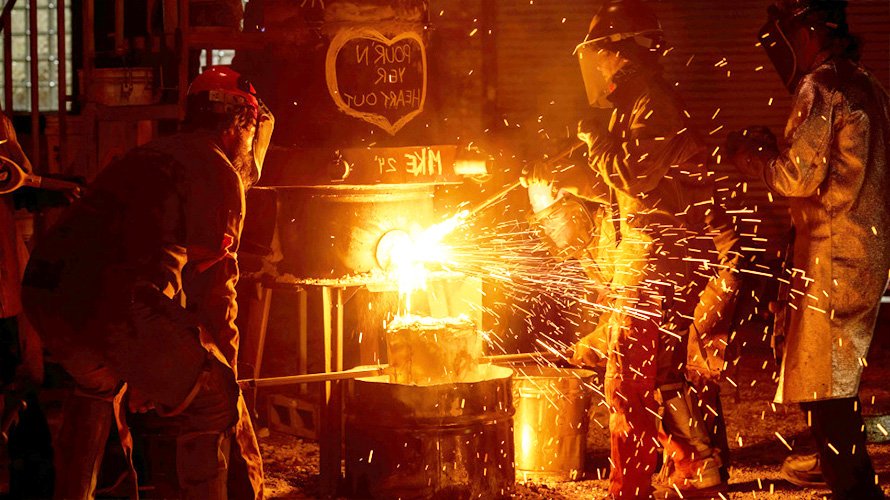
Aluminum Alloys
Aluminum alloys are lightweight, corrosion-resistant, and highly versatile, making them ideal for a range of investment casting applications.
Advantages of Aluminum in Investment Casting
Aluminum’s low density makes it an excellent option for components where weight reduction is critical. Additionally, it has good thermal conductivity and is resistant to oxidation, enhancing its suitability for automotive and aerospace applications.
Examples of Aluminum-Cast Components
Common aluminum-cast parts include engine components, housings, and brackets. These parts benefit from the material’s high strength-to-weight ratio and excellent machinability.
Exotic Metals and Alloys for Specialized Applications
Titanium alloys are renowned for their strength, light weight, and corrosion resistance. While they are more expensive and challenging to work with, they are indispensable in high-performance industries.
Benefits of Titanium in Investment Casting
Titanium is biocompatible, making it suitable for medical implants and prosthetics. Its high strength-to-weight ratio also makes it a preferred material for aerospace components.
Challenges in Casting Titanium
The high melting point of titanium requires specialized equipment and expertise, making the process more complex and costly. Despite these challenges, its superior properties often justify the investment.
Nickel-Based Alloys
Nickel-based alloys, such as Inconel and Hastelloy, are known for their exceptional resistance to heat and corrosion. These alloys are indispensable in industries requiring materials that can withstand extreme environments.
Key Properties of Nickel Alloys
Nickel alloys maintain their strength and integrity at high temperatures, making them ideal for applications like gas turbines and chemical processing equipment. They also offer excellent resistance to oxidation and corrosion.
Applications of Nickel-Based Alloys in Investment Casting
Common uses include jet engine components, heat exchangers, and pumps. Their ability to perform under harsh conditions ensures the reliability of critical systems.
Copper-Based Alloys
Copper alloys, including bronze and brass, are valued for their excellent conductivity and aesthetic appeal. They are frequently used in both functional and decorative applications.
Advantages of Copper Alloys
Copper alloys offer high thermal and electrical conductivity, making them ideal for electrical components. They also have antimicrobial properties, which are advantageous for medical and plumbing applications.
Typical Copper Alloy Components
Investment casting of copper alloys is used to produce electrical connectors, plumbing fixtures, and architectural elements. The alloys’ versatility and ease of casting make them a preferred choice for a variety of industries.
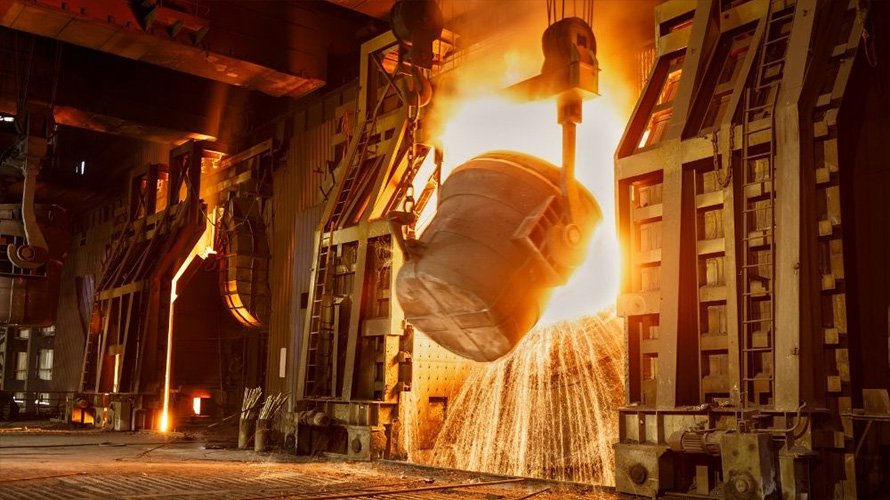
Factors to Consider When Selecting a Metal for Investment Casting
The specific mechanical properties required for the final product will significantly influence the choice of metal. Factors like tensile strength, hardness, and elasticity determine the suitability of a material for a given application.
Environmental Conditions
The operating environment of the cast part plays a critical role in material selection. Components exposed to corrosive substances, extreme temperatures, or high wear conditions require metals with appropriate resistance properties.
Cost and Availability
While performance is critical, cost and availability are practical considerations. Metals like aluminum and carbon steel are generally more affordable and readily available, while titanium and nickel alloys are costlier but offer superior performance for specialized needs.
Complexity of Design
The intricacy of the design may also impact the choice of metal. Some materials, like aluminum, are easier to cast into complex shapes, while others, like titanium, may require additional expertise and specialized equipment.
Conclusion
Investment casting offers unparalleled precision and versatility, but the success of the process heavily depends on selecting the right metal. Stainless steel and carbon steel provide reliable and affordable options for a wide range of applications. Aluminum alloys excel in lightweight designs, while titanium and nickel-based alloys are ideal for high-performance requirements. Copper-based alloys, with their unique properties, cater to both functional and decorative needs.
By carefully considering factors such as mechanical requirements, environmental conditions, and budget, manufacturers can choose the best material for their specific application. Investment casting continues to be a cornerstone of modern manufacturing, enabling the production of high-quality components across industries ranging from aerospace to consumer goods.