Metal casting is an ancient manufacturing process that has evolved significantly over the centuries. Today, it remains one of the most important techniques used in producing a wide range of metal products, from small precision components to large industrial parts. In this blog, we will explore the key aspects of metal casting, from its history to the different types of casting methods, how the process works, and its various applications. Whether you’re an industry professional or someone curious about the technology behind the products you use every day, this guide will give you an in-depth understanding of the metal casting process.
History and Evolution of Metal Casting
The origins of metal casting date back over 5,000 years. Early civilizations, such as the Mesopotamians, Egyptians, and Chinese, were among the first to experiment with casting metals like bronze and iron. These early casting methods were rudimentary but laid the foundation for the development of more sophisticated techniques that would shape modern manufacturing processes.
Industrial Revolution and Advancements
During the Industrial Revolution, metal casting gained widespread significance due to the rise of factories and mass production. The introduction of steam power and machinery revolutionized the efficiency and scale of casting operations. Innovations in mold materials, like sand and later metal molds, made it possible to produce larger and more complex parts with greater precision.
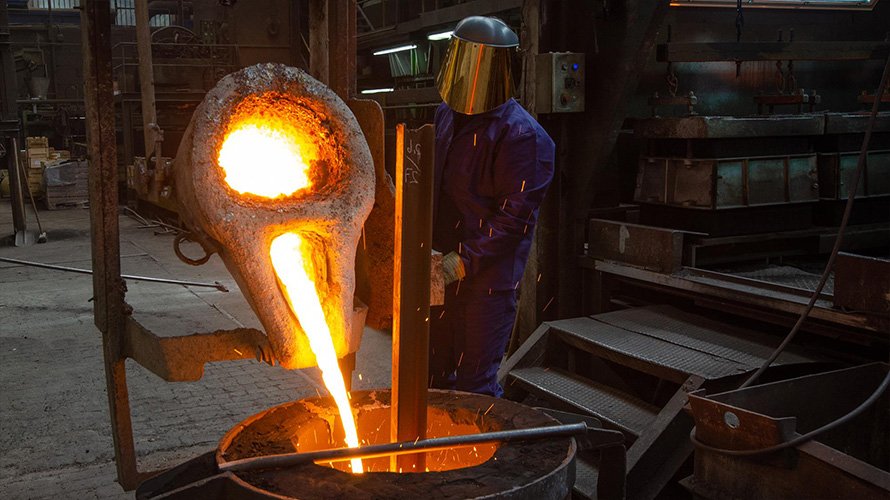
Types of Metal Casting Processes
Sand casting is one of the oldest and most widely used casting methods. In this process, a pattern of the desired part is made in sand, which is then compacted to form a mold. After the mold is created, molten metal is poured into it, filling the cavity and taking the shape of the pattern. Once the metal cools and solidifies, the mold is broken away to reveal the cast part.
Advantages of Sand Casting
Sand casting is highly versatile, capable of producing large or small parts with varying complexities. The process is also cost-effective and suitable for both short-run and large-scale production.
Limitations of Sand Casting
One of the main drawbacks of sand casting is the surface finish. Parts produced through sand casting typically require additional machining to achieve a smooth surface, which adds time and cost to the process.
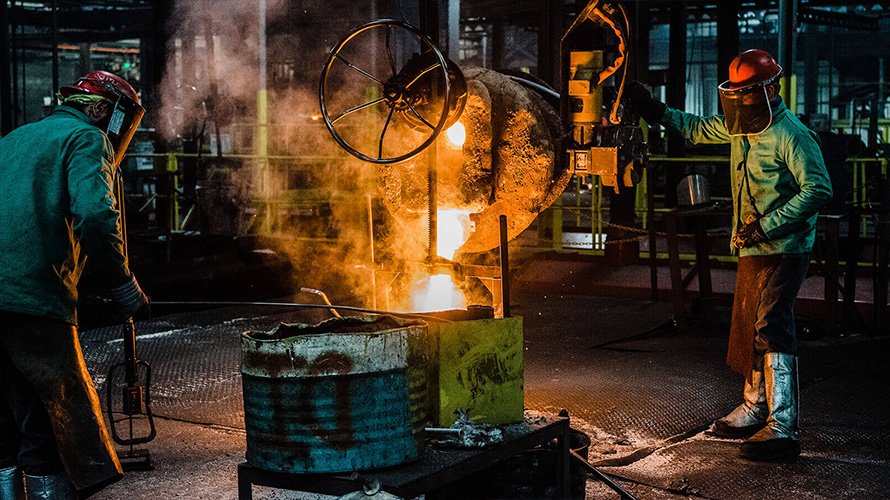
Investment Casting
Investment casting, also known as lost-wax casting, is a more precise and detailed casting method. It involves creating a wax model of the part, which is then coated in a ceramic shell. The wax is melted and drained away, leaving behind a hollow ceramic mold. Molten metal is poured into the mold, where it hardens and forms the part.
Advantages of Investment Casting
This process is highly accurate and capable of producing intricate and complex parts with smooth surfaces. It is ideal for industries that require precision, such as aerospace, medical devices, and high-performance automotive components.
Limitations of Investment Casting
Investment casting tends to be more expensive than other methods due to the high cost of materials and labor. It is also slower and generally only suitable for medium to low production volumes.
Die Casting
Die casting is a process where molten metal is injected into a metal mold under high pressure. This method is commonly used for producing parts made from non-ferrous metals like aluminum, zinc, and magnesium. Die casting is ideal for producing high volumes of small to medium-sized parts with a high degree of precision.
Advantages of Die Casting
The die casting process produces parts with excellent dimensional accuracy and smooth surface finishes. It is also highly efficient for mass production and can produce complex shapes that would be difficult or expensive to achieve with other methods.
Limitations of Die Casting
Die casting molds can be expensive to produce, making the process cost-effective only for high-volume production. Additionally, die casting is typically limited to non-ferrous metals.
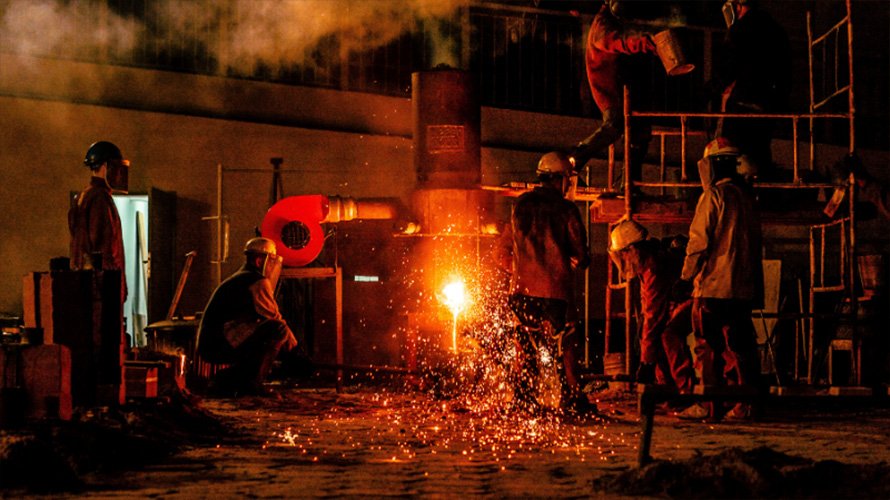
Pattern Creation
The first step in the metal casting process is creating a pattern of the part to be cast. This pattern is typically made from metal, wax, or sand, depending on the casting method being used. The pattern is a precise replica of the final part, and its dimensions must be accurate to ensure the casting process yields the correct shape.
Mold Formation
Once the pattern is ready, a mold is created around it. The mold serves as a cavity that will be filled with molten metal. In sand casting, this involves packing sand around the pattern to create a mold. In investment casting, a ceramic shell is built around the wax pattern. In die casting, a metal die is used to form the mold.
Melting the Metal
Next, the metal selected for casting is heated to its molten state. The temperature at which the metal is melted depends on its composition. Common metals used in casting include aluminum, iron, steel, and bronze, each with specific melting points.
Pouring the Molten Metal
Once the metal reaches the appropriate temperature, it is poured into the mold. This must be done quickly and carefully to avoid introducing air pockets, impurities, or other defects into the casting. The molten metal then fills the cavity of the mold and begins to solidify.
Cooling and Solidification
After the molten metal has been poured into the mold, it is allowed to cool and solidify. The cooling time varies depending on the size of the part and the type of metal used. During this phase, the metal shrinks slightly as it solidifies, which is why molds are often made slightly larger than the desired final dimensions.
Mold Removal and Finishing
Once the metal has solidified and cooled, the mold is removed to reveal the cast part. Depending on the casting method, this could involve breaking the sand mold or removing the ceramic shell. The part may require additional processes such as trimming, grinding, or machining to remove any excess material and achieve the desired finish.
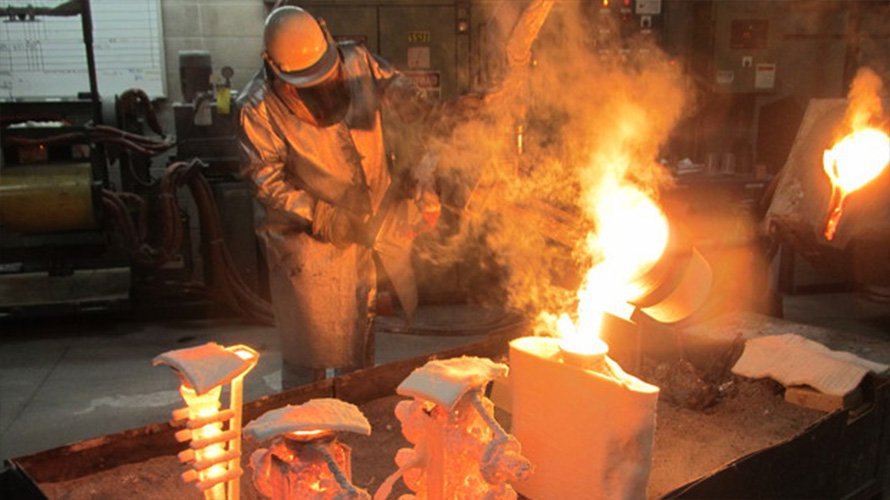
Applications of Metal Casting
The automotive industry relies heavily on metal casting for the production of critical components such as engine blocks, transmission cases, and suspension parts. These parts must be strong, durable, and lightweight, and casting allows manufacturers to achieve these characteristics while reducing material waste.
Aerospace and Aviation
In aerospace, precision and reliability are paramount. Metal casting plays a crucial role in producing parts such as turbine blades, landing gear components, and structural elements of aircraft. Investment casting, in particular, is widely used in this industry due to its ability to create complex, high-performance parts with excellent dimensional accuracy.
Medical Devices
Medical device manufacturers also rely on metal casting to produce components that require high precision and strength. Parts like surgical instruments, implants, and diagnostic equipment are often produced using investment casting, which can achieve the fine detail required for such sensitive applications.
Consumer Goods
From household appliances to electronics, metal casting is also used to manufacture a wide range of consumer goods. The versatility of metal casting allows for the creation of both functional and aesthetically pleasing products, including decorative elements and complex mechanical parts.
Conclusion
Metal casting is a versatile and essential manufacturing process that has stood the test of time. With a wide range of methods to choose from, each offering unique advantages and challenges, casting remains one of the most efficient ways to produce complex and high-precision parts. Whether it’s for the automotive, aerospace, medical, or consumer goods industries, metal casting will continue to play a critical role in shaping the products we rely on every day. By understanding the various types of casting methods, the steps involved in the process, and the industries that depend on it, you can better appreciate the importance of this technique in modern manufacturing.