The automotive industry is undergoing rapid transformation, propelled by advancements in manufacturing techniques and materials. A key element of this change is the casting of automotive parts, which is vital for creating high-quality, durable components that satisfy the needs of contemporary vehicles. In this blog, we'll examine the latest trends in metal casting, explore various techniques for casting automotive parts, and showcase innovations in automotive metal casting that are influencing the industry's future, supported by real-world examples and industry references.
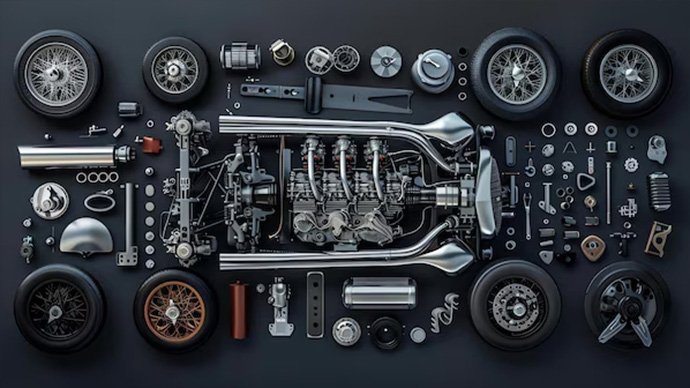
What Is Auto Parts Casting
Auto parts casting is a manufacturing process where molten metal is poured into molds to create specific automotive components. This technique allows for the production of complex shapes and high-strength parts, essential for modern vehicles' performance and durability. Common materials used include aluminum, iron, and steel.
Trends in Auto Parts Casting
Key trends in metal casting for vehicles are currently shaping the automotive industry. These trends aim to boost component performance, minimize environmental impact, and increase manufacturing efficiency. Here are some of the trends worth mentioning:
Adoption of New Materials
The adoption of new materials in auto parts casting has been significantly influenced by several factors, including advancements in technology, sustainability goals, and the need for improved performance. Here are some key trends:
Lightweight Materials
The adoption of lightweight materials in auto parts casting has become a significant trend, driven primarily by the automotive industry's need to enhance fuel efficiency and reduce emissions. A notable trend is the growing substitution of traditional steel parts with lightweight metals recognized for their superior strength-to-weight ratios, like aluminum castings and magnesium alloys.
High-strength Steel
High-strength steel (HSS) in automotive parts casting refers to steel grades that have higher yield strength and tensile strength compared to standard carbon steels. These materials are designed to improve the performance, safety, and efficiency of vehicles. The use of high-strength steel in automotive manufacturing is part of a broader trend toward lightweight materials that enhance performance while meeting stringent safety and environmental regulations.
Composite Materials
Composite materials in auto parts casting are materials made from two or more constituent materials with significantly different physical or chemical properties. When combined, they create a material that offers enhanced performance characteristics compared to the individual components. In the automotive industry, composites are increasingly used for various applications due to their lightweight nature, strength, and resistance to corrosion.
Additive Manufacturing
Additive manufacturing (AM), often referred to as 3D printing, is a process that creates objects layer by layer from digital models. In the context of auto parts casting, it represents a significant shift in how automotive components are designed and produced.
3D Printing for Prototyping
3D printing for prototyping in auto parts casting involves creating detailed and accurate prototypes of components that can be used to produce molds for casting. This process allows automotive engineers to rapidly iterate designs, test fit and functionality, and validate performance before committing to traditional manufacturing. By using 3D-printed patterns, manufacturers can achieve complex geometries and reduce lead times, making it easier to adapt designs based on testing outcomes. Ultimately, this approach enhances efficiency and precision in the development of automotive parts.
Direct Metal Laser Sintering (DMLS)
Direct Metal Laser Sintering (DMLS) is an additive manufacturing technology that uses a laser to fuse metal powder into solid parts. In the context of auto parts casting, DMLS allows for the rapid production of complex geometries that traditional casting methods might struggle to achieve.
Smart Manufacturing
Smart manufacturing in auto parts casting integrates advanced technologies and data-driven processes to enhance efficiency, quality, and flexibility in production. AI and machine learning enhance auto parts casting by optimizing design processes, predicting defects, and improving production efficiency. They analyze vast datasets to identify patterns, enabling better material selection and process parameters. Additionally, these technologies facilitate real-time monitoring and predictive maintenance, ultimately reducing costs and enhancing quality in the casting process.
Sustainability initiative
Sustainability initiatives in auto parts casting focus on reducing environmental impact, improving resource efficiency, and promoting social responsibility. By focusing on these areas, the auto parts casting industry can contribute to a more sustainable future while meeting the demands of modern automotive manufacturing.
Material Recycling
Recycling and reusing materials in auto parts casting is the processes of repurposing scrap materials and components to reduce waste, conserve resources, and lower production costs. Recycling and reusing materials in auto parts casting typically involves reclaiming scrap metal, using recycled alloys, and implementing closed-loop systems. The process starts with collecting waste materials from production and end-of-life vehicles. These materials are then melted down and purified before being recast into new components. This not only reduces waste but also lowers energy consumption and raw material costs, ultimately leading to more sustainable manufacturing practices.
Energy Efficiency
Energy efficiency in auto parts casting refers to optimizing processes to reduce energy consumption while maintaining quality and productivity. This can involve using advanced materials, improving furnace designs, implementing heat recovery systems, and adopting automated technologies. Delving into these practices can lead to the ultimate reduction in operational costs and environmental impact.
Conclusion
Casting automotive parts remains a fundamental aspect of the industry, with the latest trends and techniques in automotive metal casting playing a vital role in shaping its future. By keeping up with innovations and exploring advanced casting methods, manufacturers can improve efficiency, performance, and sustainability. Leading automotive companies provide real-world examples of these advancements, offering valuable insights into the future of parts manufacturing.
For those in automotive manufacturing, staying informed about these metal casting trends and understanding the latest processes is crucial for remaining competitive and meeting the demands of modern vehicle production.
We encourage you to delve deeper into these developments and consider their potential impact on your manufacturing processes. Staying updated on the latest advancements will help you implement best practices in automotive metal casting. At EATHU, we prioritize providing tailored advice to meet your specific needs. Reach out to an EATHU expert today to discover the best solutions for you.