Agricultural machinery plays a crucial role in ensuring that modern farming operations run smoothly and efficiently. From tractors to combine harvesters, these machines are essential for large-scale farming, and the wear parts they require must withstand extreme conditions. One of the most effective ways to produce these durable components is through the metal casting process. Agricultural wear parts casting ensures that essential components like gears, blades, and engine parts are designed to last and function optimally. In this blog, we’ll explore the casting process, the materials used, key agricultural wear parts, and best practices for designing and manufacturing high-performance parts for the agriculture industry.
The Role of Metal Casting in Agricultural Wear Parts
Metal casting is a well-established process in the manufacturing of agricultural wear parts. The process involves pouring molten metal into a mold to create complex shapes and precise parts that are used in a variety of farming equipment. Cast parts are essential for agricultural machines, as they must endure harsh environments, extreme wear, and constant exposure to high loads.
Why Metal Casting is Ideal for Agricultural Parts
Agricultural machinery operates in tough conditions, often in fields with rough terrain, dirt, and moisture. Metal casting offers a cost-effective and versatile solution for creating parts that can withstand these conditions. The casting process allows for the production of parts with excellent wear resistance, strength, and durability, making it an ideal choice for agricultural wear parts. Additionally, casting can produce parts in complex shapes that would be difficult or impossible to manufacture using other methods.
Types of Agricultural Wear Parts
Wear parts are components that experience high levels of stress and friction during operation, causing them to degrade over time. In agricultural machinery, wear parts include engine components, gears, blades, and various other moving parts that must be replaced periodically due to wear and tear. Metal casting is commonly used to manufacture parts like:
Engine Blocks and Cylinder Heads
Transmission Components
Gears and Bearings
Plows, Harrows, and Cutting Blades
Rotor Housings and Axles
Casting Materials for Agricultural Wear Parts
The materials used in agricultural wear parts casting significantly impact the performance and lifespan of these components. Different metals offer varying properties, such as strength, durability, resistance to corrosion, and heat tolerance. Selecting the right material for each application is critical to ensure that the parts perform optimally under the demanding conditions of agricultural machinery.
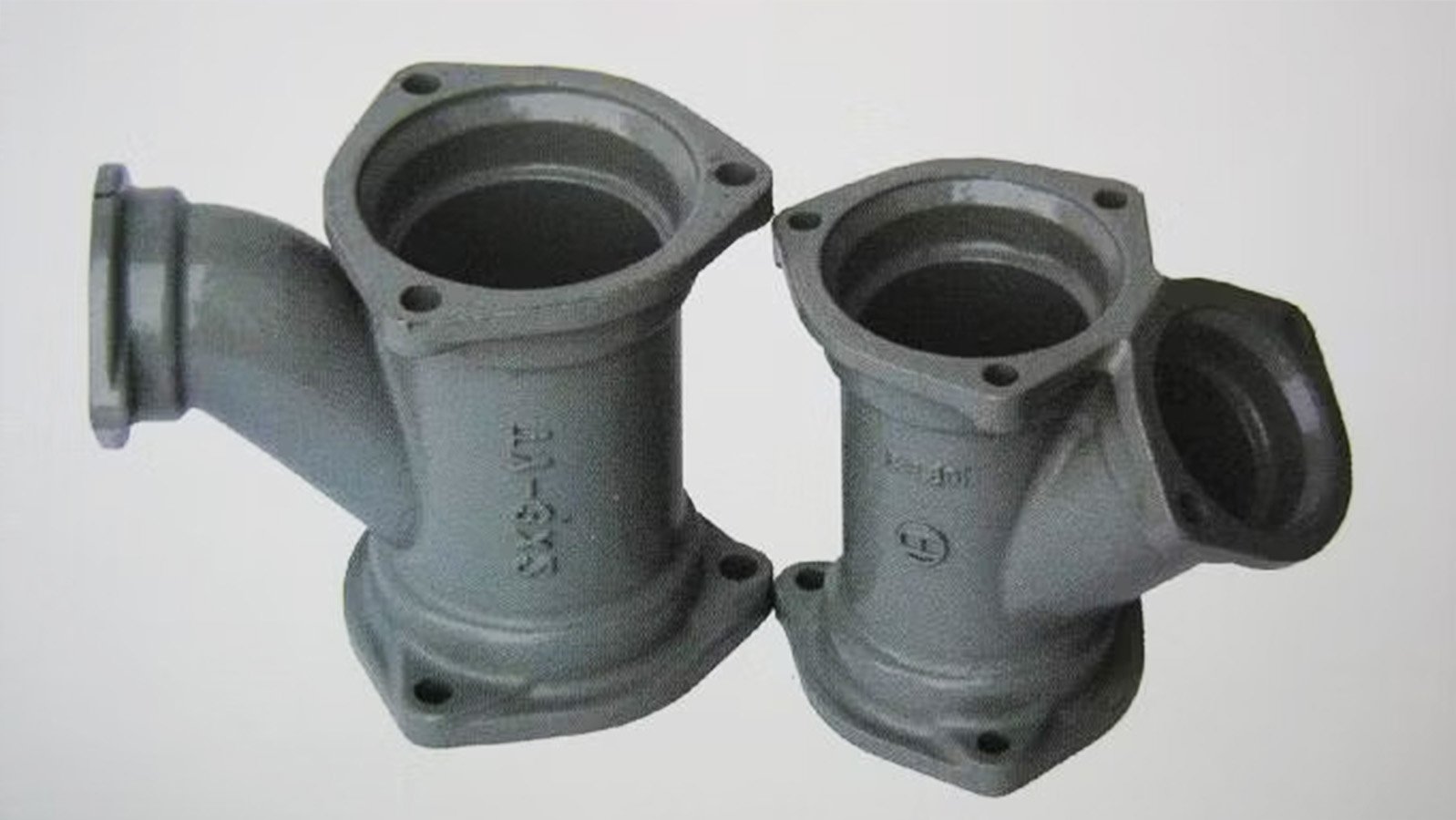
Gray Iron and Ductile Iron
Gray iron is a popular material for casting agricultural wear parts due to its excellent castability, wear resistance, and ability to absorb shock. It is particularly used for engine blocks, cylinder heads, and other high-stress components. Ductile iron, an advanced form of gray iron, offers increased strength and ductility, making it ideal for parts that are subject to high impact and pressure, such as gears and rotor housings.
Steel Alloys
Steel is often used for parts that require high tensile strength and resistance to abrasion. Steel alloys are more durable than iron and are often used for components like gears, axles, and shafts that experience high wear in agricultural applications. Steel casting also allows for customization in terms of hardness and wear resistance, making it suitable for a wide variety of agricultural machinery.
Aluminum Alloys
Aluminum is lighter than iron and steel, making it ideal for parts that need to be both strong and lightweight. It is often used in components such as housing units and parts that need to withstand corrosion. While aluminum alloys are not as strong as steel, they are often used in non-load-bearing components where weight reduction is a priority.
Bronze and Brass
Bronze and brass alloys are often used in agricultural parts that require corrosion resistance, especially in environments with high moisture or exposure to fertilizers and chemicals. These alloys are commonly used for components such as bearings, bushings, and fittings.
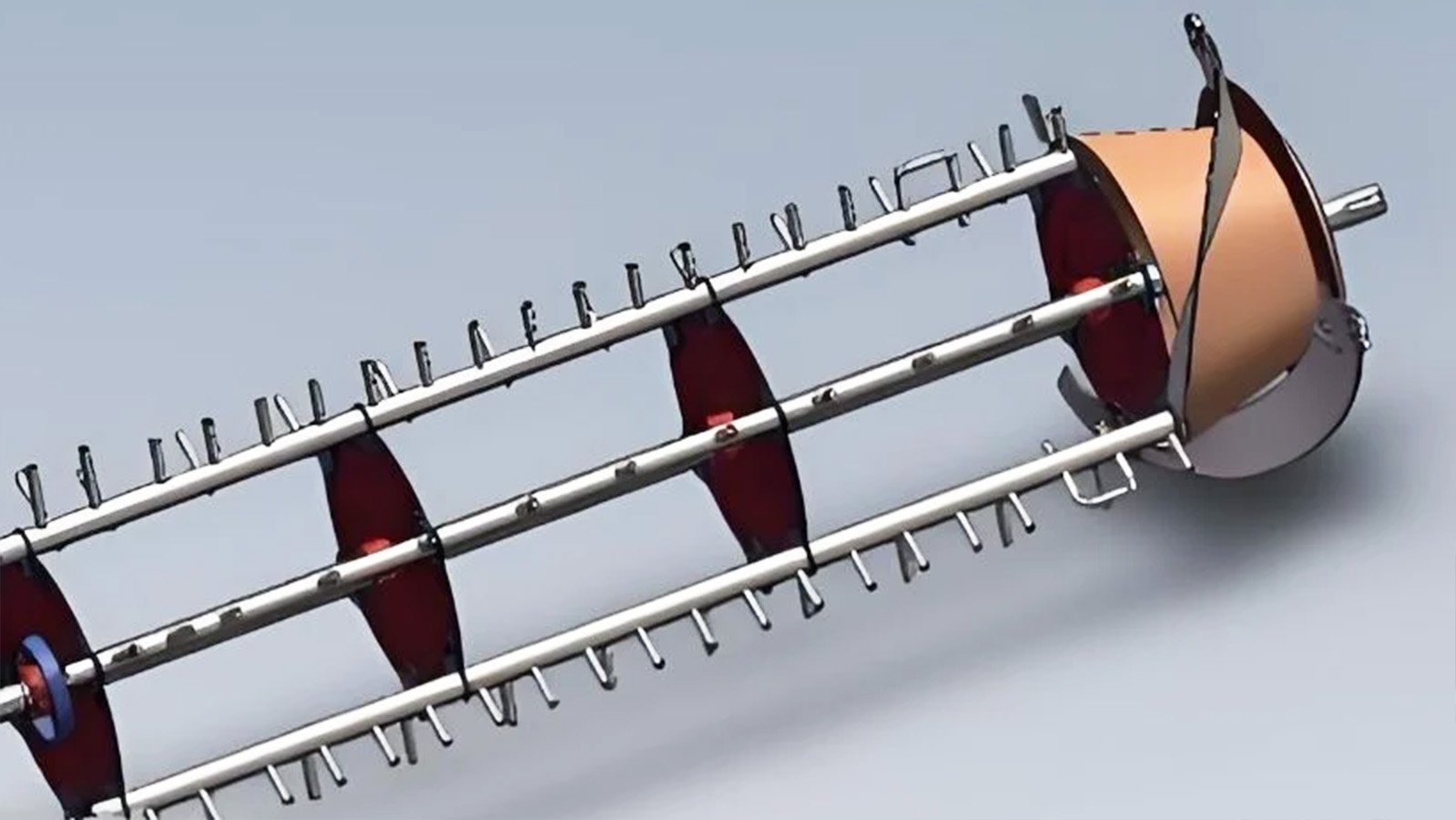
Casting Processes for Agricultural Wear Parts
The casting process plays a significant role in the quality and performance of agricultural wear parts. The choice of casting technique depends on the part’s complexity, size, and material requirements. There are several methods of metal casting commonly used in the production of agricultural parts.
Sand Casting
Sand casting is one of the oldest and most commonly used casting methods in the agricultural industry. It involves creating a mold from sand, which is then filled with molten metal to form the part. Sand casting is particularly suited for large and medium-sized agricultural parts, such as engine blocks and plow components. The process is highly versatile and cost-effective, allowing for the production of both simple and complex shapes.
Die Casting
Die casting involves injecting molten metal into a steel mold under high pressure. This method is typically used for producing small to medium-sized parts that require high precision, such as gears, housings, and bearings. Die casting is ideal for producing parts with tight tolerances and smooth surfaces, making it suitable for high-performance components in agricultural machinery.
Investment Casting
Investment casting, also known as lost-wax casting, is a method used to produce highly detailed and complex parts. It involves coating a wax model with a ceramic shell, which is then heated to remove the wax and create a mold. Investment casting is often used for agricultural parts that require fine details and high precision, such as small components for engines, pumps, and valves.
Centrifugal Casting
Centrifugal casting is used to produce cylindrical components, such as pipes, shafts, and tubing. The process involves pouring molten metal into a rotating mold, allowing the centrifugal force to push the metal toward the mold’s outer surface. This results in parts with uniform thickness and excellent strength, making it ideal for components used in agricultural machinery that require high levels of structural integrity.
Designing Agricultural Wear Parts for Durability
When designing wear parts for agricultural machinery, several factors must be considered to ensure optimal performance and durability. Agricultural equipment operates in challenging environments, and wear parts must withstand a variety of stresses, including abrasion, impact, corrosion, and extreme temperatures. A well-designed part will enhance the efficiency and longevity of the machinery, minimizing downtime and reducing replacement costs.
Material Selection for Optimal Durability
Choosing the right material for wear parts is essential to ensure they perform well under harsh conditions. The material must have the right combination of strength, hardness, and wear resistance to handle the stresses encountered during operation. For example, materials like ductile iron are ideal for parts subject to high impact, while bronze may be used for parts exposed to high moisture levels.
Surface Treatments for Enhanced Performance
In addition to selecting the right material, surface treatments can significantly enhance the wear resistance and lifespan of agricultural parts. Processes such as heat treatment, nitriding, and coating with anti-corrosion materials can improve a part’s durability. These treatments help parts resist wear and corrosion, extending their service life and reducing the frequency of replacement.
Design for Easy Maintenance and Replacement
Wear parts in agricultural machinery need to be easily replaceable, as they undergo constant stress and wear. Designing parts that are easy to remove and replace can reduce downtime and improve the overall efficiency of farming operations. Components with simple attachment methods, such as bolts or quick-connect systems, can make maintenance easier and more cost-effective.
Trends in Agricultural Wear Parts Casting
The agricultural industry is constantly evolving, and so are the technologies used to create wear parts. There are several key trends transforming the casting process and the performance of agricultural components.
Automation in Casting
Automation is becoming more common in the metal casting industry. Robots and automated systems are used for tasks such as mold handling, pouring, and finishing. This leads to faster production times, improved accuracy, and reduced labor costs. In the agricultural sector, automation in casting can lead to a more efficient supply of high-quality wear parts.
Sustainability in Casting
Sustainability is a growing concern in manufacturing, and the agricultural wear parts casting industry is no exception. Foundries are increasingly adopting eco-friendly practices, such as recycling metal scraps and reducing energy consumption. This not only lowers costs but also helps reduce the environmental impact of the casting process.
Advanced Alloys for Better Performance
The development of new alloys with enhanced properties is driving improvements in agricultural wear parts. These advanced alloys offer better resistance to wear, corrosion, and fatigue, helping to extend the lifespan of critical components in agricultural machinery.
Conclusion
Agricultural wear parts casting is a vital process that ensures the durability and performance of farming machinery. From engine components to blades and gears, metal casting provides the precision and strength needed to create reliable parts that can withstand the harsh conditions of the agricultural environment. By understanding the materials, processes, and design considerations involved in casting agricultural wear parts, manufacturers can help improve the efficiency, sustainability, and cost-effectiveness of farming operations.
With the continued adoption of automation, sustainability initiatives, and advanced materials, the future of agricultural wear parts casting is bright. As technology advances, these trends will only continue to improve the performance and longevity of agricultural machinery, helping farmers worldwide increase productivity while minimizing costs.