Sand casting is one of the oldest and most versatile metal casting processes, and it remains widely used in a variety of industries due to its simplicity and cost-effectiveness. This method involves pouring molten metal into a sand mold, where it solidifies and takes the shape of the mold. Sand casting can be used for metals ranging from light, non-ferrous alloys to heavy-duty steels and cast irons, making it suitable for a wide array of applications. However, the choice of metal is one of the most crucial factors in determining the performance and functionality of the final product. Different metals offer unique properties that make them better suited for specific applications. In this blog post, we’ll explore which metals work best for sand casting, their advantages, and common use cases.
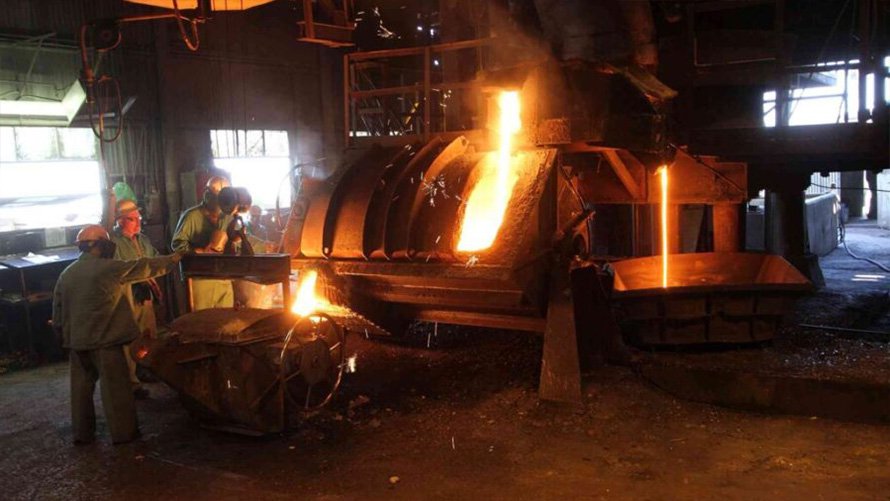
Aluminum: Lightweight and Versatile
Aluminum is one of the most popular metals used in sand casting due to its exceptional properties, which make it suitable for a variety of applications. As a non-ferrous metal, aluminum is known for its lightweight, good castability, and impressive strength-to-weight ratio.
Properties of Aluminum for Sand Casting
Aluminum stands out in sand casting because of its relatively low melting point (around 660°C or 1220°F), making it easier to work with compared to other metals like steel or cast iron. It also has excellent fluidity when molten, which allows it to fill intricate mold cavities easily and produce highly detailed castings. This is particularly important for industries like automotive, aerospace, and machinery, where precision and complex geometries are often required.
In addition to its excellent castability, aluminum is highly resistant to corrosion due to the natural oxide layer that forms on its surface. This oxide layer protects the metal from environmental factors, making it ideal for outdoor and marine applications. Aluminum is also non-toxic and fully recyclable, making it a sustainable choice for environmentally conscious manufacturing processes.
Common Applications of Aluminum Sand Castings
Aluminum castings are used in a wide variety of industries. In the automotive sector, aluminum is frequently used for engine blocks, cylinder heads, transmission housings, and wheels. The lightweight nature of aluminum helps reduce vehicle weight, leading to improved fuel efficiency and overall performance.
In the aerospace industry, aluminum alloys are employed for manufacturing lightweight structural components, such as brackets, housings, and panels. The combination of strength and low weight makes aluminum ideal for aircraft and spacecraft where every gram counts.
Aluminum is also used in the manufacturing of consumer goods like cookware, outdoor furniture, and industrial equipment, benefiting from its corrosion resistance and malleability.
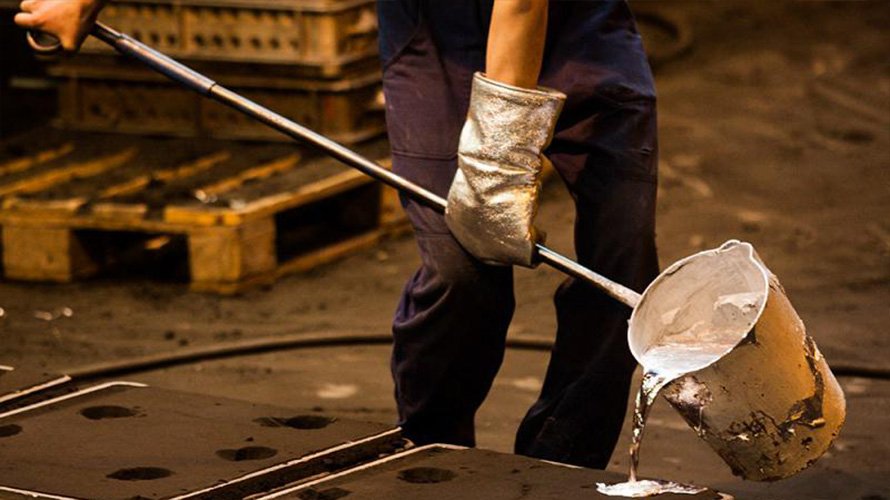
Cast Iron: Strong and Durable
Cast iron, particularly gray cast iron and ductile iron, is one of the oldest metals used in sand casting. Its strength, durability, and ability to absorb vibrations make it an ideal material for a range of demanding applications.
Types of Cast Iron Used in Sand Casting
Gray Cast Iron: Gray cast iron is characterized by its graphite content, which gives the material its distinctive gray color. The graphite is present in the form of flakes, which gives the material excellent dampening properties. These properties make gray cast iron ideal for applications where vibration absorption is crucial, such as engine blocks, machine frames, and pump housings.
The high carbon content of gray cast iron makes it brittle and less ductile compared to other metals, but it compensates for this with its excellent castability, making it easy to produce intricate and complex shapes. The material’s excellent machinability also makes it easier to process and finish after casting.
Ductile Iron: Ductile iron, also known as nodular cast iron, is alloyed with small amounts of other elements such as magnesium, which causes the graphite to form spherical nodules instead of flakes. This improves the material’s strength and ductility, making it more suitable for applications that require higher impact resistance and toughness. Ductile iron is used in applications like automotive parts, industrial machinery, and pipes.
Applications of Cast Iron Sand Castings
Cast iron’s strength and durability make it a go-to material for many heavy-duty applications. In the automotive industry, gray cast iron is commonly used to manufacture engine blocks, cylinder heads, brake rotors, and other components that are subjected to high thermal and mechanical stresses.
Ductile iron is particularly valuable in industries that require parts to endure significant impact or stress. It is frequently used in the production of suspension components, gears, and heavy machinery parts. In addition, ductile iron is used for infrastructure projects such as water pipes and manhole covers, where strength and wear resistance are paramount.
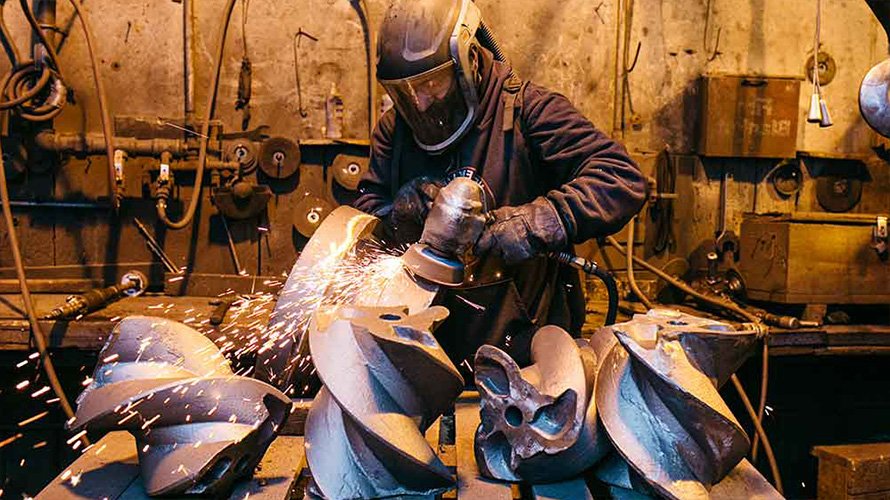
Steel: Tough and Versatile
Steel is one of the most versatile and widely used metals for sand casting. It has high tensile strength, toughness, and the ability to withstand extreme temperatures, making it ideal for a wide range of industrial and mechanical applications. While steel has a higher melting point (around 1370-1530°C or 2500-2800°F) compared to aluminum or cast iron, it is highly valued for its strength and performance under stress.
Benefits of Steel in Sand Casting
Steel offers a combination of toughness, strength, and flexibility that makes it suitable for a variety of applications. It can be alloyed with other metals, such as chromium, nickel, and molybdenum, to enhance its properties, such as corrosion resistance and heat resistance. This adaptability makes steel an excellent choice for sand casting in industries where parts must withstand high temperatures, heavy loads, and exposure to harsh environments.
Steel is also known for its weldability and machinability, which makes it easier to further process after casting. It can be used to produce parts with tight tolerances and complex geometries. Although the casting process for steel requires higher temperatures and more advanced techniques, the end result is a material that can handle heavy-duty applications that demand high mechanical properties.
Steel Sand Casting Applications
Steel castings are commonly used in the automotive, construction, and energy sectors. In the automotive industry, steel is used for manufacturing components such as gears, crankshafts, and suspension parts, where high strength and wear resistance are crucial. Steel castings are also used for producing industrial equipment parts such as pumps, turbines, and valves.
In the construction industry, steel castings are used for components in bridges, buildings, and infrastructure, where the material’s strength is essential for ensuring stability and durability. Additionally, in the energy sector, steel castings are employed in the manufacture of power plant components, including gas turbines and valves.
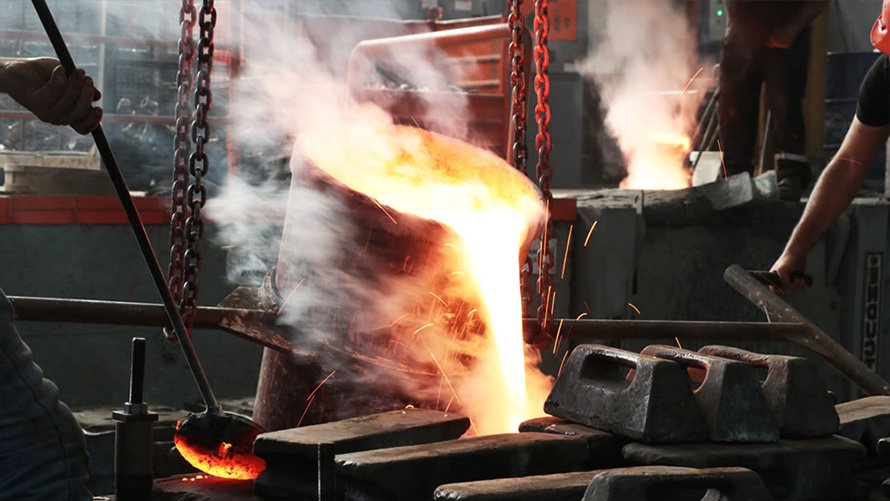
Copper Alloys: Corrosion-Resistant and Malleable
Copper alloys, including bronze and brass, are excellent materials for sand casting due to their high corrosion resistance, excellent thermal and electrical conductivity, and ease of machining. These alloys are particularly valued in applications that require parts that are resistant to corrosion or have high electrical conductivity.
Why Choose Copper Alloys for Sand Casting?
Copper alloys, such as bronze (an alloy of copper and tin) and brass (an alloy of copper and zinc), are prized for their excellent corrosion resistance, especially in marine environments. These alloys also have high ductility, meaning they can be easily shaped without breaking, and they offer excellent machinability, which is beneficial for post-casting operations.
Bronze, in particular, is known for its durability and resistance to wear and tear, which makes it a popular choice for bearings, bushings, and other components subjected to frequent friction. Brass, on the other hand, has a slightly lower corrosion resistance but is highly malleable and can be used for a wide variety of decorative and functional applications, including fittings, locks, and hardware.
Both copper alloys are also great at conducting electricity and heat, making them ideal for use in electrical and thermal applications.
Applications of Copper Alloy Sand Castings
Copper alloys are commonly used in the manufacturing of marine hardware, plumbing fittings, electrical components, and decorative items. Bronze, due to its strength and corrosion resistance, is often used to create bearings, bushings, gears, and statues. Brass, with its aesthetic appeal and machinability, is widely used for making electrical connectors, locks, and valves.
In the electrical industry, copper alloys are used to create components that require high electrical conductivity, such as connectors, terminals, and switchgear. Additionally, the marine industry relies on copper alloys for parts that need to resist seawater corrosion, including propellers, pumps, and valves.
Choosing the Right Metal for Your Sand Casting Project
When selecting a metal for sand casting, it’s important to consider the unique properties of the material and the specific requirements of your application. Aluminum is perfect for lightweight, corrosion-resistant components; cast iron offers strength and durability for heavy-duty applications; steel excels in high-stress and high-temperature environments; and copper alloys provide corrosion resistance and electrical conductivity.
Each metal offers distinct advantages and can be tailored to meet the needs of various industries. By understanding the properties of these metals and considering the operational conditions of the final product, manufacturers can make informed decisions that lead to the production of high-quality, reliable castings.
Whether you’re casting automotive parts, industrial machinery, or decorative items, choosing the right metal for your sand casting project is essential for ensuring optimal performance and longevity. Understanding the advantages and limitations of each metal will help you make the best choice for your casting needs, leading to better results and greater overall satisfaction with your final product.