Introduction
In industrial production, the status of gray iron castings is crucial. It has good casting properties, mechanical properties, heat and wear resistance and corrosion resistance, low cost and suitable for mass production, widely used in many fields, laying the foundation for the development of the industry. At the same time, gray iron castings can be recycled, good environmental performance, the industry chain to drive the growth of related output, promote technological progress and employment, and have a positive effect on economic development. In view of this, an in-depth understanding of its performance to take advantage of the advantages of industrial production is very necessary.
The mechanical properties of gray iron casting
Gray iron castings mechanical properties data usually comes from a single casting test bar, but the test bar performance may not be fully representative of the actual castings, especially the shape, wall thickness and test bar different castings. In order to more accurately present the cooling rate due to the wall thickness caused by the different organization and performance changes, often use the fit test block. For castings with special requirements, test bars with similar cooling rates can be selected according to the wall thickness of critical areas to determine the properties. For example, the ground beam liquid iron casting castings in different cases, wall thickness and tensile strength of the relationship between the different embodiments; compressor body casting test can be seen, the wall thickness affects the pearlitic content, which affects the performance of the test block; brake drum casting test shows that the specific conditions of a single casting test bar test its performance is feasible.
Gray iron castings process performance
(A) Casting performance
Gray iron castings casting performance is excellent. Compared with other casting alloys, the solidification temperature range is narrow, low melting temperature, casting fluidity, easy to fill the complex casting, shrinkage is small, not easy to produce shrinkage, shrinkage and other defects, widely used thanks to these advantages.
(B) Cutting performance
Gray iron casting cutting performance is good, thanks to the flake graphite lubrication of the tool and chipbreaking effect. Its chip performance depends on the matrix organization and hardness, ferrite matrix cutting performance is the best, followed by pearlite matrix, free carburization is a sharp decline. Commonly used in the production of tensile strength and hardness ratio to control the chip performance, improve the strength of the hope that the hardness is low to maintain good cutting performance.
(C) Welding performance
Cast iron welding performance is worse than steel, but gray iron castings relative to ductile iron and other good. Cold welding can be used for unimportant small parts or surface defects welding. Because of the graphite and iron and carbon alloy crystallization properties of cast iron, its welding performance is affected, but gray iron castings performance is still available. Such as gray cast iron gas welding welding some small defects, cold welding method need to pay attention to avoid too much melting of the base material, welding, stirring the molten pool to help gas slag floating out can improve quality.
Gray iron castings of other performance characteristics
(A) Strength enhancement methods
Gray iron castings can be added to the raw material in a small amount of carbon, manganese, chromium and other trace elements or alloying to improve tensile strength. Determine the wall thickness, the appropriate amount of manganese (0.4% - 2%), and add trace alloying elements, while doing a good job of iron gestation treatment.
(B) Defects and repair
Casting surface loosening, shrinkage is easy to cause scrap, mostly due to structural irrationality, commonly found in large wall thickness or concave corner parts. Repair can use the traditional welding process or casting defect repair machine. Traditional process for unimportant small parts or surface defects; casting defect repair machine repair does not heat deformation, no cracks, welded patch metal dense, but the welding patch range is small, inefficient, recommended for machine tool casting defects with the use of both composite applications.
(C) Retest conditions
The first test does not meet the mechanical properties can be repeated when the test. If the results do not meet the requirements due to specimen mounting, test machine operation, specimen surface defects or improper processing, tensile specimen fracture location or port defects, etc., the test is invalid, should be re-sampled for testing.
(D) Properties and applications of different materials
Gray iron castings of different materials with different mechanical properties, applicable parts are different. HT150/35B material shock absorption performance is excellent, applicable to general stress mechanical machine tool castings; HT200/30B material is applicable to the more important mechanical equipment parts; HT150/25B material has wear-resistant corrosion-resistant ability, applicable to machine tools and equipment, etc., hardness of the parts can be quenched for hard parts; HT300/45B material is applicable to bear high stress parts; HT300/45B material is applicable to bear high stress parts; HT300/45B material is applicable to bear high stress parts. HT300/45B material is suitable for bear high stress parts. Each material supports a variety of heat treatment processes and nitriding treatment.
Conclusion
Gray iron castings have a variety of properties, mechanical properties of the data obtained in a special way and the test bar performance and the actual castings have differences; process performance is excellent, casting, cutting, welding and patching performance has its own characteristics; can be enhanced in a variety of ways to enhance the strength of the defects have the appropriate means of repair, the performance of different materials are different for different parts. Understanding these properties helps to play the advantages of gray iron castings to serve industrial production.
In conclusion, gray iron castings are a remarkable choice in the industrial realm due to their diverse and valuable properties. Their mechanical, process, and other characteristics make them suitable for a wide range of applications. When it comes to reliable and high-quality gray iron casting production, EATHU Foundry stands out as an excellent option. With its advanced technology, experienced team, and commitment to quality, EATHU Foundry can ensure that the gray iron castings produced meet the highest standards, providing customers with durable and efficient components for their various industrial needs. Whether it's for machinery manufacturing, automotive, construction, or other industries, EATHU Foundry has the capabilities to deliver top-notch gray iron castings that contribute to the success and functionality of the end products. Consider partnering with EATHU Foundry for all your gray iron casting requirements and experience the difference in quality and performance.
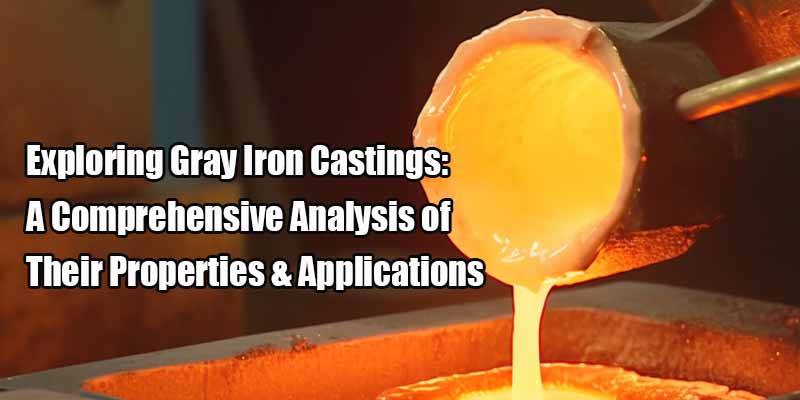