Coated sand is a kind of sand material widely used in the foundry industry, which is mainly combined by sand and resin, and commonly used in the manufacture of cast iron, cast steel and non-ferrous metal castings. According to the different needs of use and process characteristics, coated sand can be divided into several types, the following is a common classification and its professional characteristics:
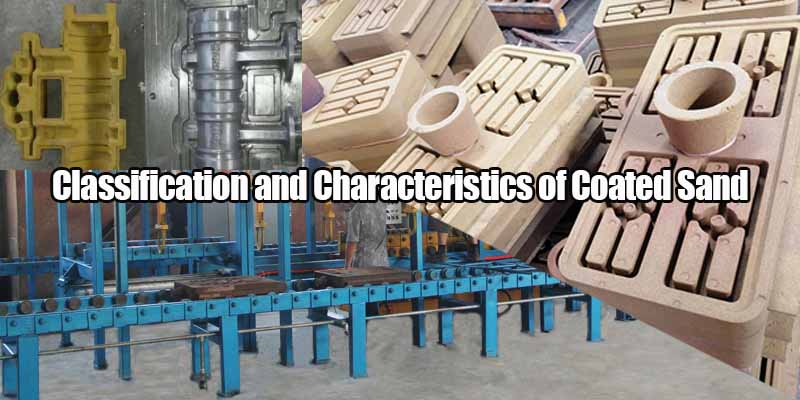
High-strength low outgassing coated sand
Main components:
Quartz sand, modified phenolic resin (such as Furan resin), calcium stearate and other additives.
Production method:
On the basis of ordinary coated sand, through the addition of “additives” with relevant characteristics and the use of new formulation process, the resin dosage is greatly reduced, the amount of gassing is significantly reduced, and the rate of gassing can be slowed down.
Characteristics:
High strength, low outgassing, low expansion, slower outgassing rate, better adaptability, able to maintain good core strength at higher casting temperatures.
Application:
It is suitable for cast iron and steel castings with high requirements for gas generation and strength, and is especially suitable for the manufacture of sand cores for small and medium-sized steel castings, such as valve cores.
Advantages:
It can effectively reduce the surface defects of castings, minimize the casting defects such as porosity and cracks, and ensure the quality of castings.
Ordinary coated sand
Main components:
Quartz sand thermoplastic phenolic resin, urotropin and calcium stearate, without adding relevant additives.
Characteristics:
Relatively high resin addition, large gas generation, moderate strength, suitable for conventional casting requirements.
Application areas:
Suitable for cast iron castings with relatively simple structure and general technical requirements, usually used for casting production with medium and low requirements.
Advantages:
Relatively low production costs, suitable for large-scale production, and has better modeling performance.
Centrifugal casting coated sand
Main components:
High-density quartz sand, phenolic resin, the right amount of additives.
Characteristics:
According to the material and diameter size of the casting pipe and different technical requirements, can be processed into different performance of the centrifugal casting sand. Sand density, strength and high temperature performance is better, lower gas generation, adapt to the characteristics of centrifugal casting, can be in the high-speed rotation of the centrifugal force to maintain the stability of the core.
Application areas:
Mainly used for centrifugal casting of cast pipes, cast rings and other products, especially suitable for the manufacture of medium and large castings and cast pipes.
Advantages:
Good core stability and low outgassing characteristics, to ensure the accuracy and surface quality of castings.
High temperature resistant coated sand
Main components:
Quartz sand, high temperature resistant additives (such as chromite, bauxite), phenolic resin, etc.
Characteristics:
This type of coated sand has excellent high-temperature strength and stability, and can keep its shape unchanged at higher temperatures, so it is suitable for high-temperature casting environments.
Application:
It is suitable for the production of complex thin-walled precision cast iron parts, high-precision and high-complexity cast iron, cast steel and non-ferrous metal castings, especially for castings used in high-temperature environments, such as engine blocks, train brake parts, and so on.
Advantages:
High temperature resistance, low expansion, low outgassing, slow outgassing, can effectively reduce defects due to thermal deformation in the casting process.
Wet hand-coated sand
Main components:
Quartz sand, wet phenolic resin, catalyst and so on. The wet compression strength of laminating sand can be adjusted arbitrarily within 0.1~0.3MPa. The storage period is more than 3 months. It is suitable for manual molding or core making (similar to tung oil sand and synthetic grease sand), after demolding at room temperature, the type (core) is put into the oven or furnace to be heated with a heating temperature of 250~350℃ and a heating time of 3~10min, and the type (core) is cured. In the type (core) heating curing, must wait for the furnace temperature to reach the required temperature before being put into the heating, do not heat up with the furnace heating.
Characteristics:
The wet state laminating sand can keep stability for a long time, and will not be cured by storing it for too long time, and it has the characteristics of strong adaptability, high strength, low outgassing, small creep deformation, and non-absorption of moisture.
Application areas:
Mainly used for manual molding, small batch casting and precision casting manufacturing, especially suitable for precision casting and complex castings, such as art casting, model casting, etc..
Advantages:
Suitable for non-automated production lines, with good mobility and modeling, and able to achieve high casting accuracy in small batch production.
Wet Mechanical Coated Sand
Main components:
Quartz sand, wet resin, appropriate amount of catalyst and stability enhancer.
Characteristics:
This type of coated sand can be stored in the wet state, has good processing performance and is suitable for mechanized production.
Applications:
Widely used in the production of large-scale castings, able to be used in automated casting production lines, replacing the traditional hot core box sand.
Advantages:
High production efficiency, adaptability, can provide a more stable quality of sand, reducing the complexity of manual operation.
Easy Disintegration Coated Sand
Main components:
High-strength quartz sand, dispersible resin, special additives.
Characteristics:
This type of coated sand has good dispersibility and can be easily removed after the casting is cooled down by simple knocking or wind blowing.
Applications:
It is especially suitable for the production of non-ferrous metal castings such as aluminum alloy, copper alloy, etc. It is widely used in precision casting and thin-walled castings.
Advantages:
Easy to remove sand, no need to reheat the casting to remove sand, only need to cool the casting after pouring for 24 hours, can vibrate the sand, reduce the cleaning workload, can improve the production efficiency and casting quality.
Conclusion
The types and characteristics of coated sand determine its application range in the casting process. By choosing the right type of coated sand, the casting quality can be effectively improved, the incidence of defects can be reduced, and the production process can be optimized. Choosing the right type of cladding sand not only improves the accuracy of castings, but also enhances production efficiency and reduces casting costs.
Commitment of EATHU Foundry
At EATHU Foundry, we are always committed to providing high quality casting solutions to our customers. With years of experience in the industry and advanced casting technology, we offer a wide range of coated sands to meet different casting needs. From high-strength coated sands to special sands that are high temperature resistant and easy to collapse, our products can help you improve the precision and surface quality of your castings. Whatever the size of your project, we can provide customized services to ensure that every casting meets the highest standards. When you choose EATHU Foundry, you get a trusted partner and quality casting products.