In the modern casting field, resin sand casting occupies an important position with numerous advantages. However, its process is complex, and many key points need to be accurately controlled to produce high-quality castings. The following will conduct an in-depth analysis of its core process key points to help practitioners deepen their understanding and optimize the production process.
I. The Impact of Sand Temperature on Hardening and Control Strategies
(I) The Relationship between Hardening Principle and Sand Temperature
In the resin sand casting process, the hardening mechanism of furan resin self-hardening sand is unique. Resin, as the basic bonding material, undergoes a cross-linking reaction step by step under the "trigger" of the curing agent, just like building precise molecular bridges, gradually transforming from a loose state to a stable structure to achieve the goal of self-hardening. The curing agent plays the role of a "catalyst" in this process, and its catalytic efficiency is extremely sensitive to temperature changes. Temperature is like an invisible "speed regulator". When the temperature rises steadily, the activity of the curing agent molecules is fully stimulated, and the catalytic reaction accelerates rapidly; conversely, when the temperature drops, it is like pressing the "slowdown button" for the reaction, and the catalytic process slows down significantly.
This close relationship is directly reflected in the hardening reaction rate and the strength of the casting mold. A large number of production practice data show that under the "standard situation" where other variables are constant, for every 10°C increase in sand temperature, the hardening reaction rate almost doubles geometrically, and the available time is sharply shortened to half of the original time; if the sand temperature decreases by 10°C, the reaction rate is correspondingly halved, and the available time is doubled accordingly. Considering various factors comprehensively, the ideal "comfort zone" of sand temperature for self-hardening resin sand is in the range of 25 - 30°C. However, in actual large-scale production scenarios, considering environmental disturbances, equipment tolerances, etc., the sand temperature is usually controlled within the relatively wide but practical range of 20 - 35°C.
(II) Analysis of Sand Temperature Adjustment Methods
Equipment Adjustment: Standard and complete resin sand production lines are often equipped with professional "temperature control tools" such as sand temperature regulators or fluidized bed coolers. Take the sand temperature regulator as an example. Its operation principle contains an elaborate counter-current water circulation design. Inside the device, the sand follows the law of gravity and slides slowly from top to bottom, like a delicate "sand waterfall"; cold water flows steadily upward along the spiral pipe, against the flow direction of the sand, and the two complete efficient heat exchange through carefully arranged heat dissipation fins. However, in the sweltering summer, when the external environmental temperature soars above 30°C, to obtain low-temperature water that meets the cooling requirements, enterprises either have to spend a huge amount of money to dig deep wells to extract groundwater or add additional refrigeration devices, which is costly and difficult to implement for many foundries, resulting in the sand temperature regulator being "powerless" in the high-temperature summer, becoming a thorny "bottleneck" restricting efficient production and ensuring product quality.
Circulation Volume Adjustment: Flexibly adjusting the sand circulation volume based on different seasonal climate characteristics is a clever "adaptive strategy". In cold winter, when the temperature is low, reducing the sand circulation volume enables the newly generated shakeout sand with residual heat to quickly enter the recycling process, which is energy-saving and efficient; in the hot summer, when the climate is sweltering, appropriately increasing the sand circulation volume allows the sand "wrapped" by high temperature to have more sufficient time to "dissipate heat and cool down" in the sand bin or on the workshop floor and gradually return to the ideal state. However, this method also has "side effects". When the circulation volume is drastically reduced, the sand bin above the mixer is prone to the phenomenon of "temperature difference stratification", that is, the temperature difference between the sand retained from the previous working day and the newly delivered sand on the same day is significant. If the management and control are improper, it will easily lead to uneven hardening degrees in different parts of the sand mold, as if it is "patched together", seriously affecting the quality of the casting mold; when the circulation volume increases sharply, once the capacity of the sand treatment system is "overwhelmed", the redundant sand can only be helplessly "scattered" on the workshop floor, occupying precious production space and making the workshop environment "dusty" and messy.
Water Spray Cooling Method: Resin self-hardening sand has always adhered to strict standards for the water content of raw sand and recycled sand, requiring it to be controlled at a low level of < 0.2%. The old sand recycling process clearly prohibits water spraying operations. However, in the actual bustling production line, when the temperature soars and the reaction speed of the resin sand gets out of control, adding an appropriate amount of water to the curing agent has become a "wonderful emergency measure" for many experienced workers, and after long-term practice, there is no obvious fluctuation in product quality. The root cause lies in that the water content before mixing is the "key lifeline". As long as the recycling process can efficiently volatilize the water to the standard state, even if the initial sand is slightly damp, it will not affect the subsequent processes. Moreover, moderate water spraying can not only "cool down" the hot sand but also effectively suppress the annoying dust flying in the workshop, creating a relatively clean working environment. The physical characteristics of water endow it with powerful cooling efficiency. The specific heat capacity is about 4.18 Kj/kg.K, and the latent heat of vaporization is about 2400 kJ/kg, which means that the heat absorbed by the vaporization of a unit weight of water is 574 times that of the heat absorbed by a 1°C temperature rise. In the scenario where the shakeout temperature of castings is usually controlled below 400°C, accurately spraying water on the shakeout sand causes the water to vaporize instantly, and the subsequent recycling process continues to "dry and remove water". After years of production verification, there is no significant negative impact on the quality of castings. When operating, the choice of water spraying location is of great importance. The vibrating conveyor trough after the shakeout machine is a "golden point". The more than ten subsequent turnover links and dust extraction facilities work together to ensure that the sand after water spraying is fully dried and returns to a "dry and crisp" state; at the same time, the determination of the water spraying amount needs to be carefully calculated and repeatedly debugged in combination with multiple factors such as sand temperature and environmental humidity to accurately grasp the balance between "cooling" and "moisture control".
II. The Management and Control of Curing Agent Dosage and Acid Value
(I) The Relationship between Dosage, Acid Value and Hardening Rate
In the resin sand system, the dosage ratio of the curing agent is accurately defined by the proportion of the resin. Just as the ratio of seasonings to ingredients determines the flavor when cooking a delicious dish, the addition amount and acid value of the curing agent jointly affect the hardening rate. Under the premise of a constant acid value, the addition amount of the curing agent is like the "accelerator pedal". The larger the addition amount, the hardening process is like a racing car "speeding at full throttle" and becomes faster; conversely, it is like a slow-moving snail, and the hardening becomes slower. When the addition amount is fixed, the acid value is like the "quality of fuel". The higher the acid value, the more sufficient the catalytic "power" and the faster the hardening rate, and vice versa, it is sluggish. It should be emphasized that the hardening rate is by no means the faster the better or the slower the more stable. Once it deviates from the reasonable range, too fast will easily lead to a "loose and fragile" internal structure of the casting mold, and too slow will be difficult to form a stable structure, both of which will mercilessly reduce the strength foundation of the casting mold after hardening.
(II) Reasonable Control of Curing Agent Parameters
In the normal production situation, the addition amount of the curing agent is like a flexible "float", adjusting with the "waves" of sand temperature and workshop environmental temperature. The overall control range is mostly set within 30 - 50% of the resin addition amount, just like sailing in a safe channel. In a high-temperature environment, in order to prevent the reaction from being "overly excited and out of control", the lower limit is taken to ensure a moderate hardening rhythm; when covered by low temperature, in order to activate the reaction "heat", the upper limit is taken to ensure that the hardening rate does not "drop the chain". For large castings with a long sand placement time, the addition amount of the curing agent needs to be carefully "restrained" to take the lower limit, reserving sufficient available time for the resin sand to avoid "hardening and setting" in advance during the long waiting process and affecting the smooth progress of subsequent processes.
III. Special Requirements of Resin Sand Casting for Molds
(I) Precise Setting of Machining Allowance
After hardening, the resin sand casting mold is like putting on "solid armor", with excellent stiffness, "pinpoint" dimensional accuracy, and outstanding deformation resistance. Based on this unique advantage, when finalizing the process parameter "blueprint", enterprises have the confidence to select a more delicate machining allowance. Such an operation is like "carving with great care", which can not only greatly reduce the unnecessary consumption of metal solution and lower the cost of raw materials but also simplify the machining process and duration and reduce the "burden" of machining costs, achieving a quality leap from "extensive" to "fine" by double efforts to improve the final dimensional accuracy of the casting.
(II) Adaptation of Draft Angle
Resin sand casting has unique characteristics. At the moment of mold removal, it already has considerable hardening strength, just like a "stubborn teenager" with weak yieldability and strong friction resistance. If the traditional knocking mold removal method is still used, it is like "brute force", which is extremely easy to cause irreversible damage to the mold, and the "fragile" repairability of the resin sand means that once it is "injured", the repair is difficult and costly. Therefore, at the beginning of resin sand molding planning, it is necessary to carefully consider increasing the draft angle of the mold according to the actual production conditions and the complex structure of the product, "paving a smooth road" for smooth mold removal and ensuring the integrity and high quality of the casting mold.
(III) Strict Control of Surface Roughness
The surface roughness of the mold is like the "mold" of the casting surface, having a decisive influence. The birth path of high-quality castings cannot be separated from the fine grinding of the mold surface. Making every effort to reduce its roughness value, carefully smoothing every fine scratch and every tiny bump is to lay a solid foundation and pave the way for casting high-quality castings.
IV. A Recommendation: EATHU Foundry
In the realm of resin sand casting, one name that stands out for its excellence and reliability is EATHU Foundry. With years of experience and a team of highly skilled professionals, EATHU Foundry has mastered the nuances of the resin sand casting process, consistently delivering top-quality castings that meet the most stringent industry requirements. Their state-of-the-art facilities are equipped with advanced machinery and temperature control systems, ensuring precise management of sand temperature, curing agent dosage, and all other critical parameters. Whether it's handling complex geometries or catering to large production runs, EATHU Foundry has the expertise and capacity to execute with precision and efficiency. Their commitment to quality is unwavering, and they go the extra mile to ensure that each casting not only meets but exceeds customer expectations. If you're in the market for resin sand casting services that combine technical prowess, reliability, and a customer-centric approach, EATHU Foundry is undoubtedly worth considering. They bring a wealth of knowledge and innovation to the table, making them a trusted partner for all your casting needs.
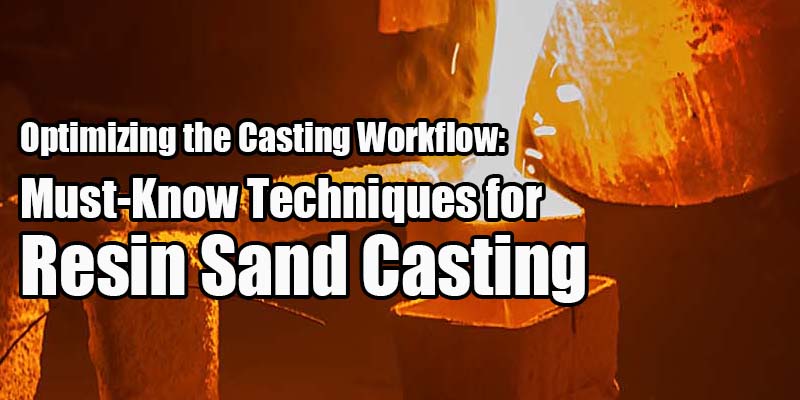