Overview of investment casting shell making process
Investment casting, also known as lost wax casting, is a high-precision casting method. Shell making process is the key link in investment casting, which mainly includes the steps of degreasing and degreasing of the die set, coating and sand spreading, drying and hardening of the shell, melting and losing the molten mold, and roasting the shell.
When wax-based molds are used to make molten molds, in order to improve the ability of the paint to wet the surface of the mold, it is necessary to remove the oil on the surface of the mold, which is the step of degreasing and degreasing of the mold. This step lays a good foundation for the subsequent process and ensures that the paint adheres better to the surface of the module.
The next step is to apply paint and sand on the module. Before applying the coating, the coating should be stirred well to minimize the precipitation of refractory material in the coating drum, and the viscosity or specific gravity of the coating should be adjusted so that the coating can fill and wet the mold well. When hanging the paint, immerse the module in the paint and shake it up and down from left to right so that the paint can wet the mold well and cover the surface of the module evenly. After the paint is applied, sanding can be carried out. This process is critical to the quality of the shell, which determines the thickness and uniformity of the shell.
After each layer of shell is applied, it is dried and hardened. This process transforms the binder in the coating from a sol to a gel or gel, holding the refractory together. The drying and hardening of the shell is a critical step, which directly affects the strength and stability of the shell.
After the shell is completely hardened, the die set needs to be melted away from the shell. Since the die set is often made of wax-based molding material, this process is also called dewaxing. Depending on the heating method, there are many methods of dewaxing, but the more commonly used methods are the hot water method and the co-pressure steam method.
If you need to molding (sand filling) casting, before baking, first after the molding shell buried box in the sand, and then loaded furnace baking. If the high-temperature strength of the shell, do not need to molding casting, can be demolded after the shell directly into the furnace roasting. Roasting gradually increase the furnace temperature, the shell heated to 800 - 1000 ℃, insulation for a period of time, can be poured.
Investment casting shell making process of each step are interrelated, together determine the quality and accuracy of the final castings. Only strict control of each link can produce high-quality castings.
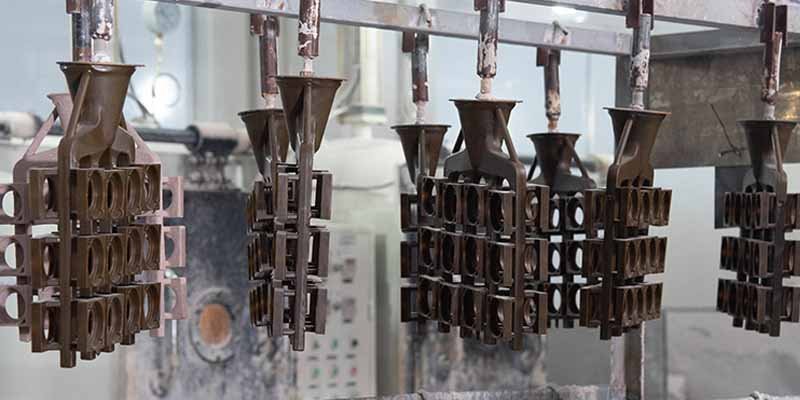
Specific steps in the shell making process
Degreasing and degreasing of the module
In order to improve the ability of the coating to wet the surface of the module, it is necessary to remove the oil from the surface of the module. This is a critical step in the production of molten molds using wax-based molding compounds, as oil on the surface of the module can affect the adhesion of the coating. Specific degreasing and degreasing processes ensure that the surface of the module is clean and provides a good foundation for the subsequent shell making process.
Hanging paint and sanding
Stir the paint to make it uniform, adjust the viscosity or specific gravity, and immerse the module in the paint to make it cover the surface of the module evenly. Before hanging the coating, stir the coating evenly to reduce the precipitation of refractory material, adjust the viscosity or specific gravity so that the coating can fill and wet the molten mold well. Soak the mold in the paint, shake it up and down from left to right to ensure that the paint evenly covers the surface of the mold. This process is crucial to the quality of the shell, which determines the thickness and uniformity of the shell.
Sanding after coating. After the paint is coated, sanding can be carried out. The purpose of sanding is to fix the coating layer with sand particles, increase the thickness of the shell, obtain the necessary strength, improve the permeability and concessions of the shell, and prevent the shell from cracking when hardening. The most commonly used sanding methods are fluidized sanding and rainfall sanding.
Shell drying and hardening
The binder in the coating is transformed from sol to gel and gel, which connects the refractory materials together. After each layer of shell is coated, it should be dried and hardened. During this process, the binder in the coating is transformed, joining the refractory materials together to form a strong shell. The drying and hardening of the shell is a critical step that directly affects the strength and stability of the shell.
Loss of mold from the shell
Dewaxing methods such as hot water and co-pressurized steam are commonly used to melt away the die set. After the shell is fully hardened, the mold is melted out of the shell. Depending on the heating method, there are many methods of dewaxing, but the hot water method and the co-pressure steam method are used more often. For example, a wax mold dewaxing device uses an electric heating wire to heat the dewaxing kettle, the wax mold with sand shell is placed in a material basket, the heating is warmed up by setting the temperature, activating the electric heating wire and circulating fan switch, and the solenoid valve is opened when the temperature reaches the preset temperature and the dewaxing is obvious, and the molten wax is transported to the wax treatment drum through the recycling pipeline.
Baking shell
According to the need, the molded shells after demolding will be buried in the sand grains in the box or directly sent to the furnace for roasting, heated to 800 - 1000 ℃, and then poured after heat preservation. If molding (sand filling) is needed for pouring, the molded shell will be buried in the sand inside the box before roasting, and then loaded into the furnace for roasting. If the high-temperature strength of the shell, do not need to molding pouring, the mold can be sent directly to the furnace after molding shell roasting. When roasting gradually increase the furnace temperature, the shell heated to 800 - 1000 ℃, insulation for a period of time, can be poured. During the roasting process, the temperature and time need to be controlled to ensure that the shell has sufficient strength and high temperature resistance.
Materials for the shell-making process
Refractories
The refractory materials used in the shell making process of investment casting are mainly quartz, corundum, aluminum silicate refractory materials and so on. Among them, electrofused corundum is made of industrial alumina or calcined alumina, melted at high temperature in electric arc furnace, which is an important raw material for making high-grade refractory materials, and is also widely used in abrasive industry. Electrofused corundum has the advantages of high refractory temperature, good chemical stability, and no phase change under high temperature conditions. In addition, brown corundum is made of bauxite, coke (anthracite) and iron filings as the main raw materials, which is purified and crystallized by high temperature melting in an electric arc furnace. It has the features of high hardness, high toughness, sharp particles, strong grinding force, high temperature resistance and high efficiency, and can be used as high-quality abrasive materials and high-grade refractories. White corundum is made of high-quality alumina powder (alumina powder) by high-temperature electro-melting and smelting, which has the characteristics of white color, high hardness, slightly lower toughness, high purity, excellent self-sharpness, strong grinding power, low heat, high efficiency, acid and alkali corrosion resistance, high temperature resistance, and good thermal stability, and it is widely used in the fields of precision casting, iron and steel refractory, and chemical refractory, and so on.
At the same time, in order to solve the problem of zirconium material shortage and rising cost in precision casting industry, the use of electrofused corundum to manufacture the shell surface layer of investment casting has better anti-sticking sand performance, but also has a wide range of resources and low price.
Binder
The most commonly used is silicate colloidal solution, such as water glass and silica sol. Silicone sol is a high-quality binder used in investment casting, which has the advantages of good high-temperature strength of the shell, high-temperature resistance to deformation, high thermal shock stability, and small surface roughness of the surface of the shell, smooth surface, and so on. The product is divided into three types: S-30 (ordinary type), S-830 (surface layer) and S-1430 (back layer), which are suitable for castings with different strength requirements. Silica particles contained in the silica sol are very small, with a large specific surface and a large surface energy, between the particles due to the surface with the same polarity of the charge and produce mutual repulsion, that is, to produce electrostatic repulsion and prevent each other from approaching, and at the same time the solvent film also prevents the particles from close contact with each other, so as to stabilize the solution. If the electrolyte is added to the silica sol, it will increase the total concentration of ions in the silica sol solution, so that the possibility of the charged particles attracting counter-ions increases, so that more diffusion counter-ions into the adsorption layer, so that the diffusion of the bilayer is thinned out, the potential is lowered, solvation decreases, the mutual repulsion between the particles decreases, and when the kinetic energy of the particles of Brownian motion can overcome the repulsive force, the particles collide with each other, resulting in the coalescence of the sol. When the kinetic energy of the particles can overcome the repulsive effect, the particles collide with each other, resulting in the condensation of the sol.
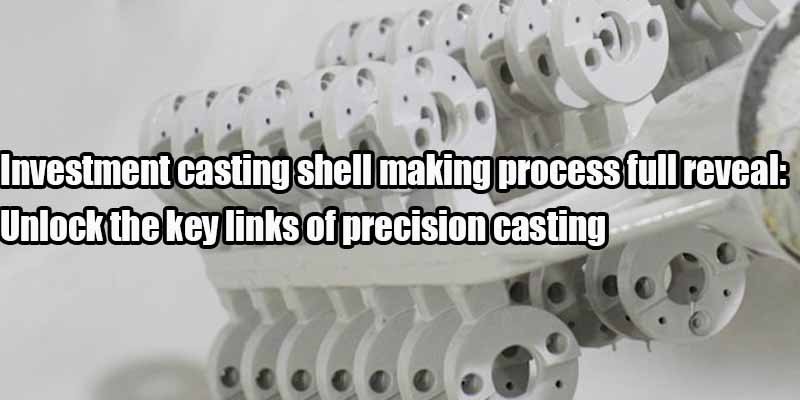